Embracing Slower Times - Part 5: Applying Standardized Work for Long-Term Success
Annah Godwin
In part five of the Peak Productivity series “Embracing Slower Times: Building Resiliency for Long-Term Success” I discuss standardized work and how to apply it during slower times. Standardized work is one of the foundational tools in lean and can be applied to create new processes or improve existing ones by minimizing the waste within them. It allows an organization to establish the least wasteful way of completing the process steps while meeting the customer’s demand.
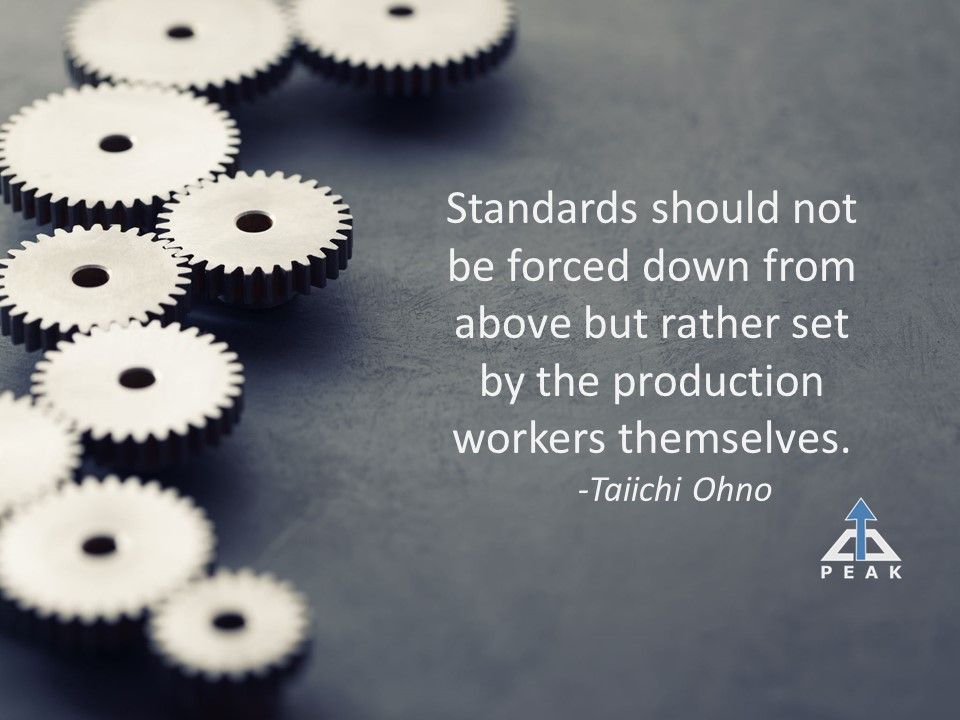
In part five of the Peak Productivity series “Embracing Slower Times: Building Resiliency for Long-Term Success” I discuss standardized work and how to apply it during slower times. Standardized work is one of the foundational tools in lean and can be applied to create new processes or improve existing ones by minimizing the waste within them. It allows an organization to establish the least wasteful way of completing the process steps while meeting the customer’s demand.
First let’s review the three components of standardized work: work sequence, WIP (work in process inventory), and Takt time. Takt time is the time required to meet the customer’s demand per unit. The calculation is the work time available divided by the customer demand. For a process to achieve customer demand the cycle time per part must be equal to or slightly less than the takt time. When the cycle time is greater than the takt time, the customer demand will not be met. WIP is the amount of inventory needed within the process steps to get the process running smoothly. Work sequence is the order in which the process steps are performed.
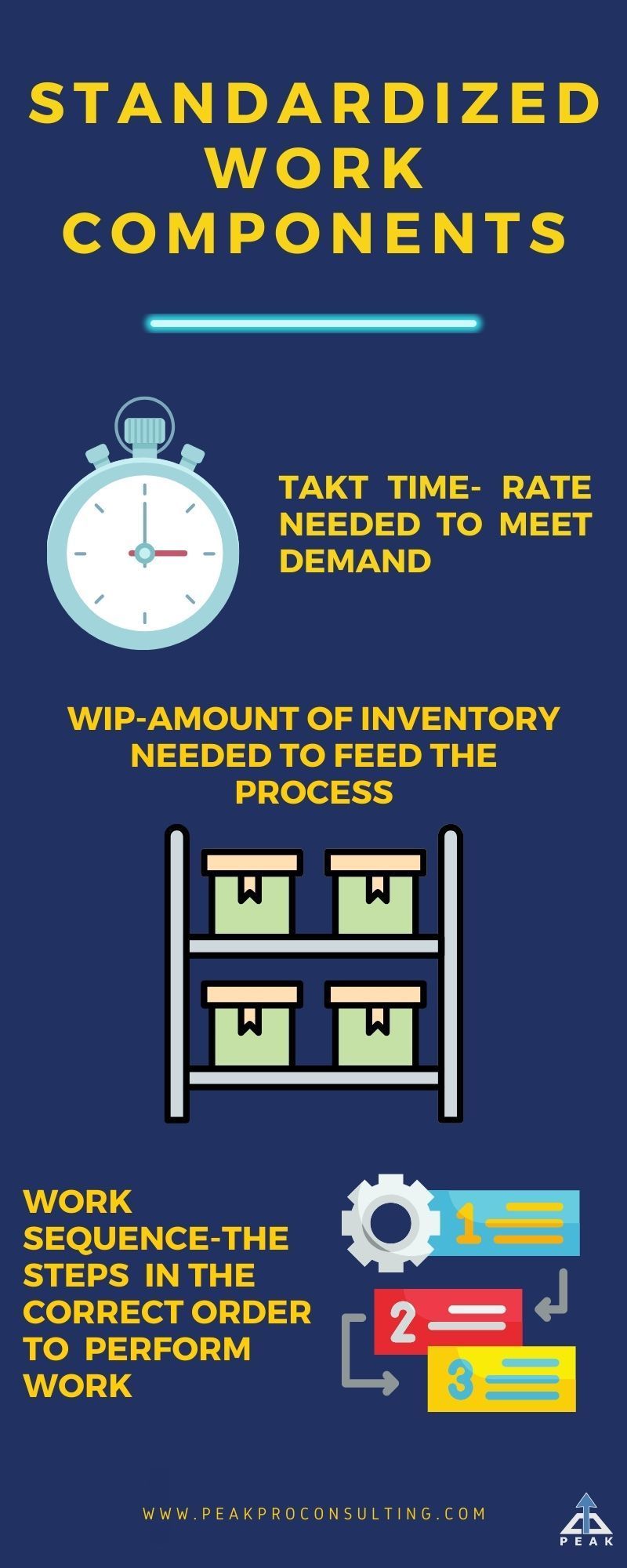
How do you determine if standardized work is currently being followed? When you go to the Gemba and observe a process, it will become apparent if there are standards in place. An area that has standardized work is going to be very consistent with a controlled amount of WIP. The process area will be neat and organized. People will understand the process steps for work to be completed, the sequence of those steps, and who is completing them. The standardized work will be posted at the location where the work occurs and should include the rate at which the process must flow to satisfy the customer’s demand. Even if standardization exists takt time and WIP should be adjusted to match the new lower demand.
So, an area that has no standardized work will look very different from the one just described. There will be a lot of variation in what the operators do in the process, which may lead to confusion about who is completing the work, or even what steps are required to complete the work. You may see an overabundance of some WIP and a shortage of others. The rate of output may not be understood as well. Based on your observations, you can determine the areas that are lacking standardized work.
Why should an organization work on updating or creating standardized work when things are slower? One reason is time. It is fairly time intensive to build standardized work from scratch. This means that instead of sending a person(s) home when things are slow, you can have them help create improvement through standardization of the processes. Usually, this involves the team members performing the required steps while someone performs the time studies. Doing so could lead to an increase in inventory, which is one of the downsides during a slow period. Make sure to validate there is ample space for the additional inventory along with confirming there is enough WIP for the process to run smoothly. One trick to mitigate the inventory dilemma is to have the operators walk through the steps in sequence but not have them produce the materials. Just remember, if the lines are not running you will need to add the machine times into the elemental or step times to show when the operators are waiting on the machinery and to provide the correct cycle times.
Another pro to standardized work is the limited materials needed to build the standardized work. Basic supplies include a stopwatch, clipboard, pencil, and log sheet to record the steps and times. The upfront cost is mainly the inventory and salaries. Once you complete the time studies and are ready to build the standardized work you will need:
- Camera (take pictures of elemental steps/machinery)
- Computer
- Printer
- Work combination sheet
- Workplace layout sheet
- Work sequence sheet
With the supplies and team members ready to go, it is time to create standardized work. Here are my steps for developing standardized work.
1. Go to the Gemba. Before I start the time studies, I go to Gemba for several hours to just observe the process. This gives me a feel for the frequency of a cycle, the intensity, and the sequence of work. I can also see how much movement is involved along with raw material or work in process flow into the area.
2. Calculate Takt time and determine inventory levels. When I come back from the Gemba, I will calculate the takt time. I may need to consult with the production or planning department about the actual customer demand. Sometimes this can be very tricky since a lot of organizations don’t run to customer demand. Instead, they may run to an artificially created demand that is determined by forecasts, pending orders, etc. It is important to know if you are building to an actual or a theoretical demand.
Also, I will discuss the WIP and the raw materials levels with the production or supply chain department. The slowdown may create issues for either WIP or raw material thus requiring calculations to establish the new inventory levels. The change could add inventory to cover some slowdowns from other departments or a reduction of materials.
I will meet with management about any changes to the work schedule that will impact the available hours in the Takt time calculation. I typically don’t include overtime in the available time since it may create a pull toward adding waste in the process. If you include overtime, it may cloud and obscure the root causes. With all this information I am now ready to calculate the rate.
3. Create a rough draft of the work sequence. Before I begin the time studies, I like to get the order of steps on paper. This allows me to focus on the stopwatch and the work instead of having to record the steps along with tracking the time.
4. Perform time studies. I watch and record the times for each step. I try to capture between 5-10 cycles with a couple of different operators. This will help build a better picture since there tend to be slight variations from person to person. However, if the cycle times are long, I watch 3-5 cycles. Just remember that you want to observe an average cycle without much variation.
In previous blogs, I've talked about the importance of being in the Gemba and some ways to approach basic observation. Observations that are performed with stopwatches can be nerve-wracking for all involved. No one likes to be timed or notes recorded about the observations. To help everyone feel comfortable in that situation I make sure to explain to everyone in the area what I am doing and why. I will do a couple of dry runs with the team before I start the watch. If things don't go smoothly, it's not a problem, just continue practicing until everyone is comfortable.
5. Review the results with the team members and modify them as needed. After the time studies are completed, I pull the team back together to review the results. Everyone can see the notes from the studies and then provide me with valuable feedback on how the process went and if further studies or modifications are needed.
6. Create and post the standardized work and review it with all team members in the area. Now the data has been collected, the takt time calculated and the WIP levels determined, it's time to pull all the information together into the standardized work packet. At this point I take pencil and paper to create the work combination sheet, the workplace layout sheet, and the work sequence sheet. If needed, I go back to Gemba and take photos to include in the workplace layout and work sequence sheets. The completed sheets are taken to the Gemba and posted in the location where the work is done. I review it with all the team members in the area along with management and include a reminder that they are living documents and should be updated anytime a change is made to the process.
Once the standardized work is complete, follow-up to reinforce sustainment is critical. The follow-up doesn’t only occur at the Gemba but also with management. As the demand changes, the WIP and Takt time should be updated to reflect it. Standardized work will provide better visibility of the process and highlight issues that occur within it. This in turn will lead to better output and higher quality. So, the next time your demand drops and things slow down, take the opportunity to improve your business and build standardized work for your processes.
I am always interested in hearing how other people deploy lean tools, so feel free to add your thoughts about standardized work in the comments section. As always, we at Peak Productivity are more than happy to answer questions and discuss in more detail this tool, its application, and its benefits.
Peaks and Valleys.....
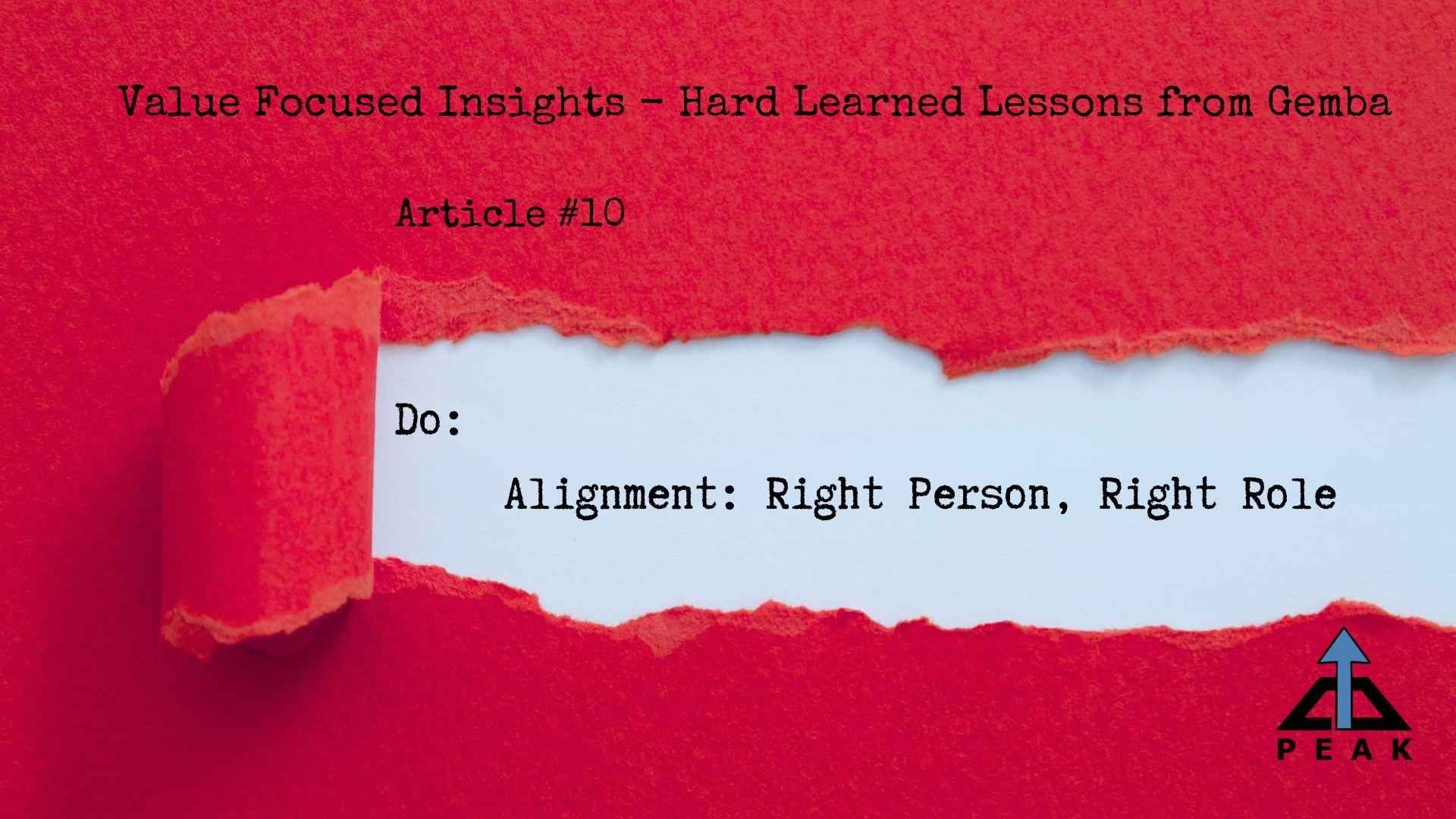
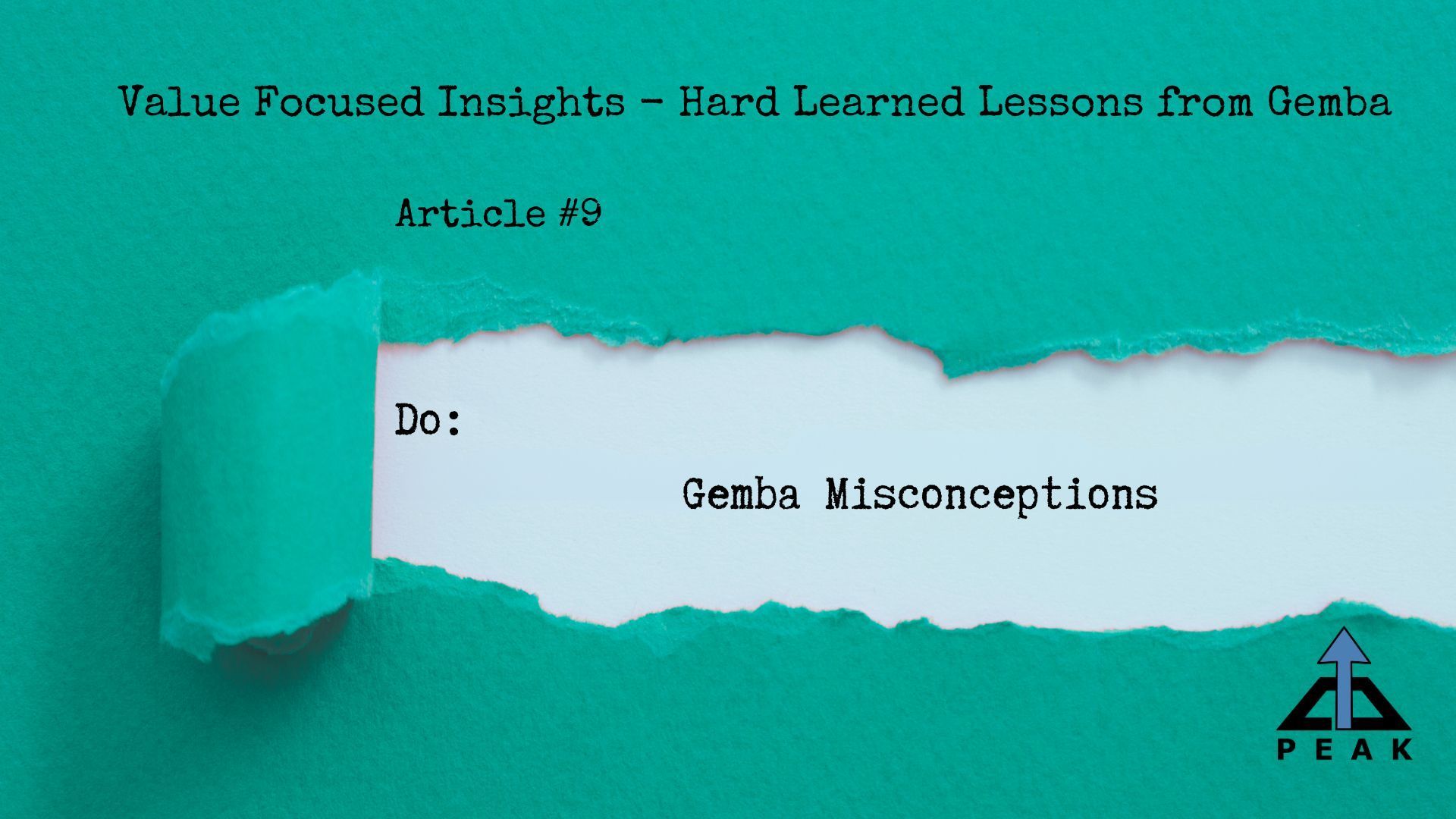
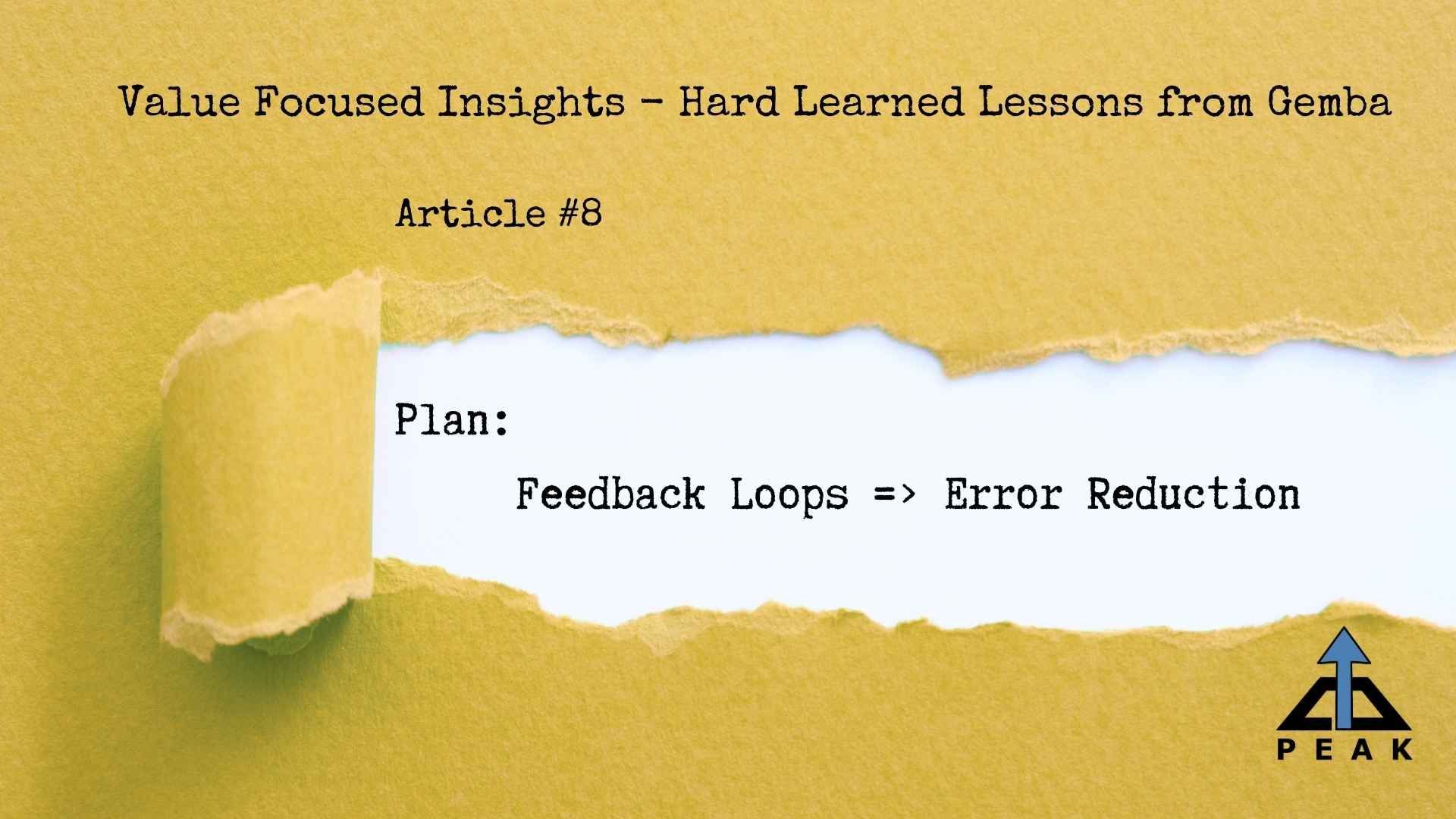
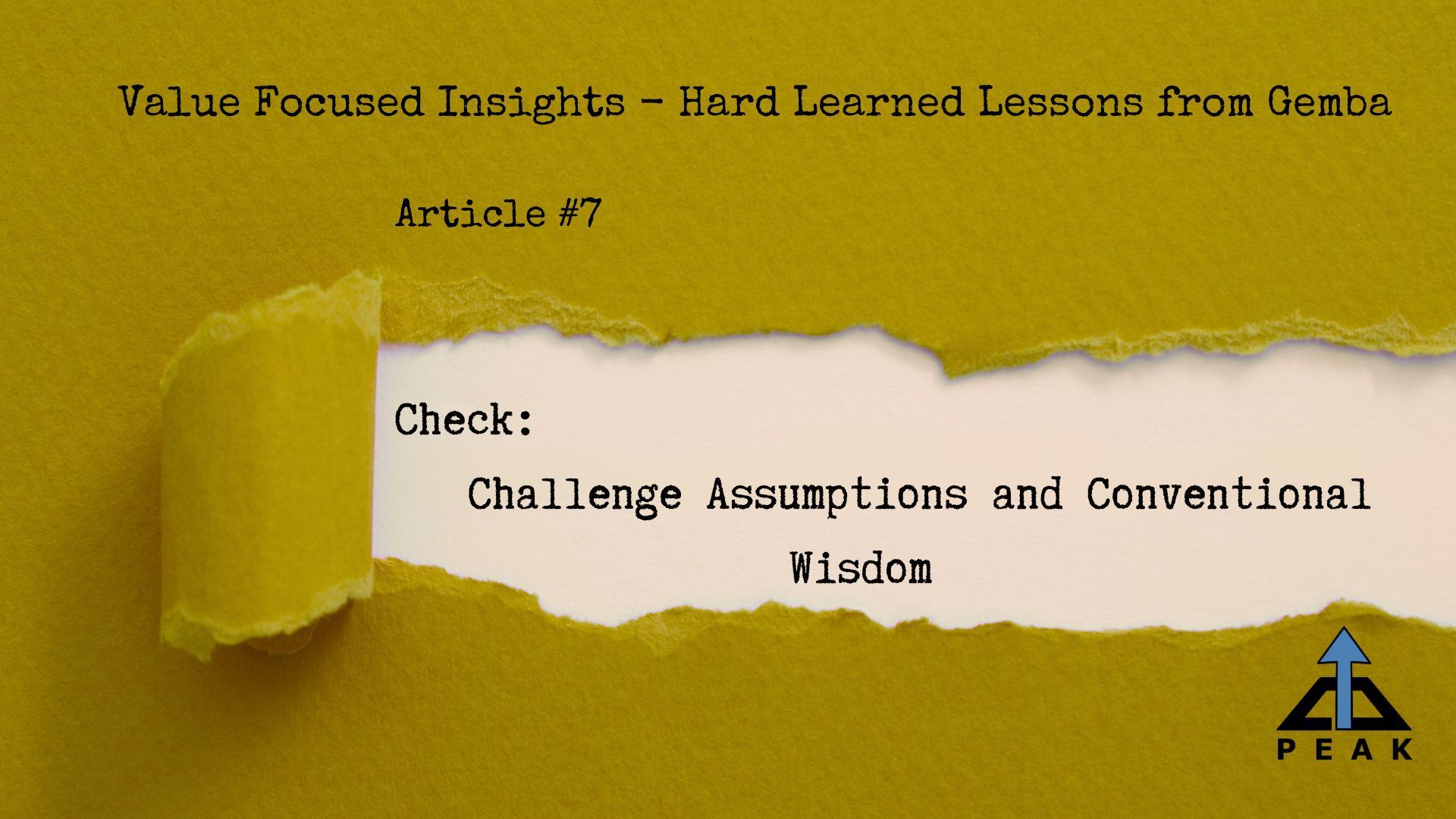
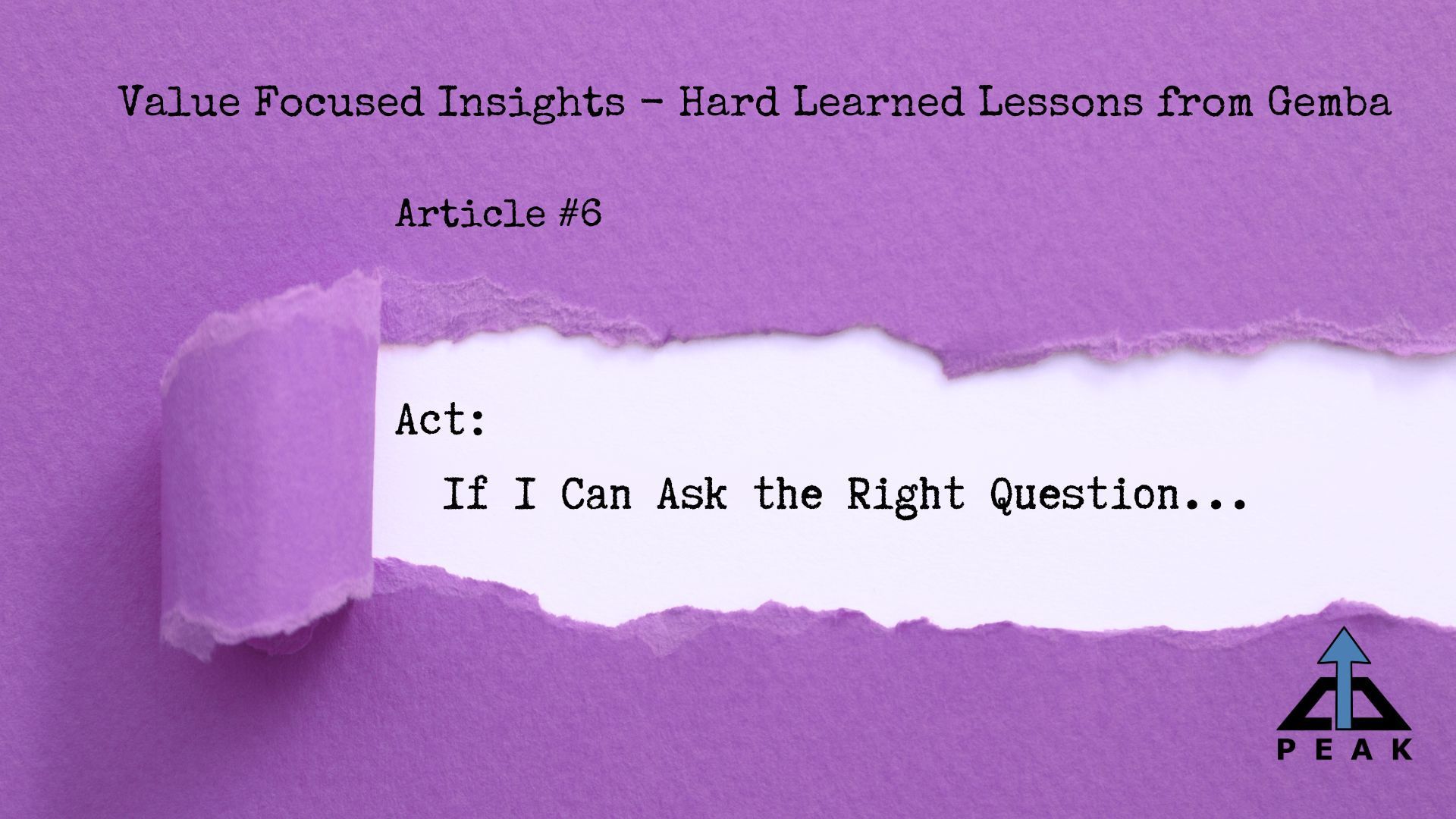
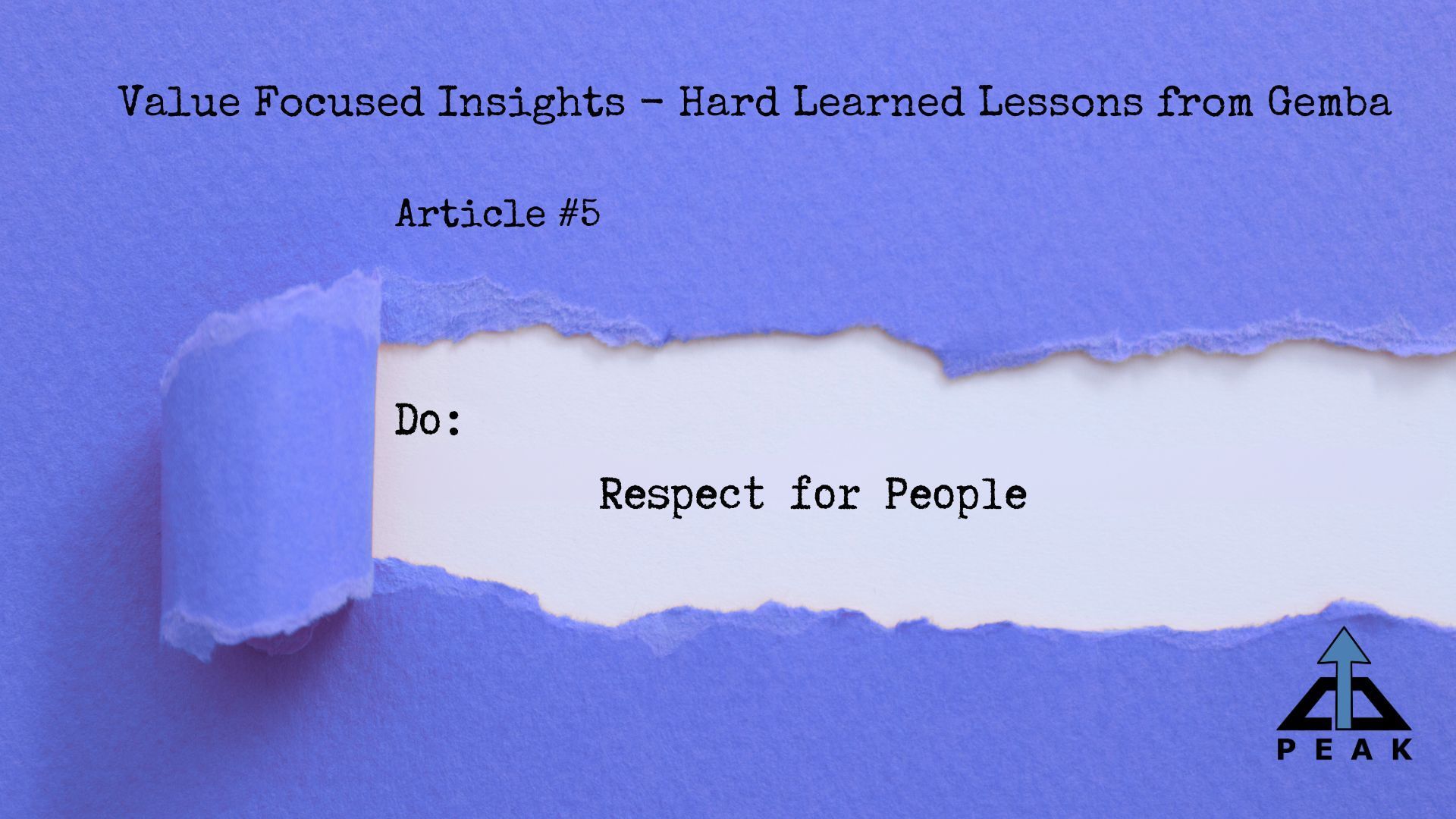
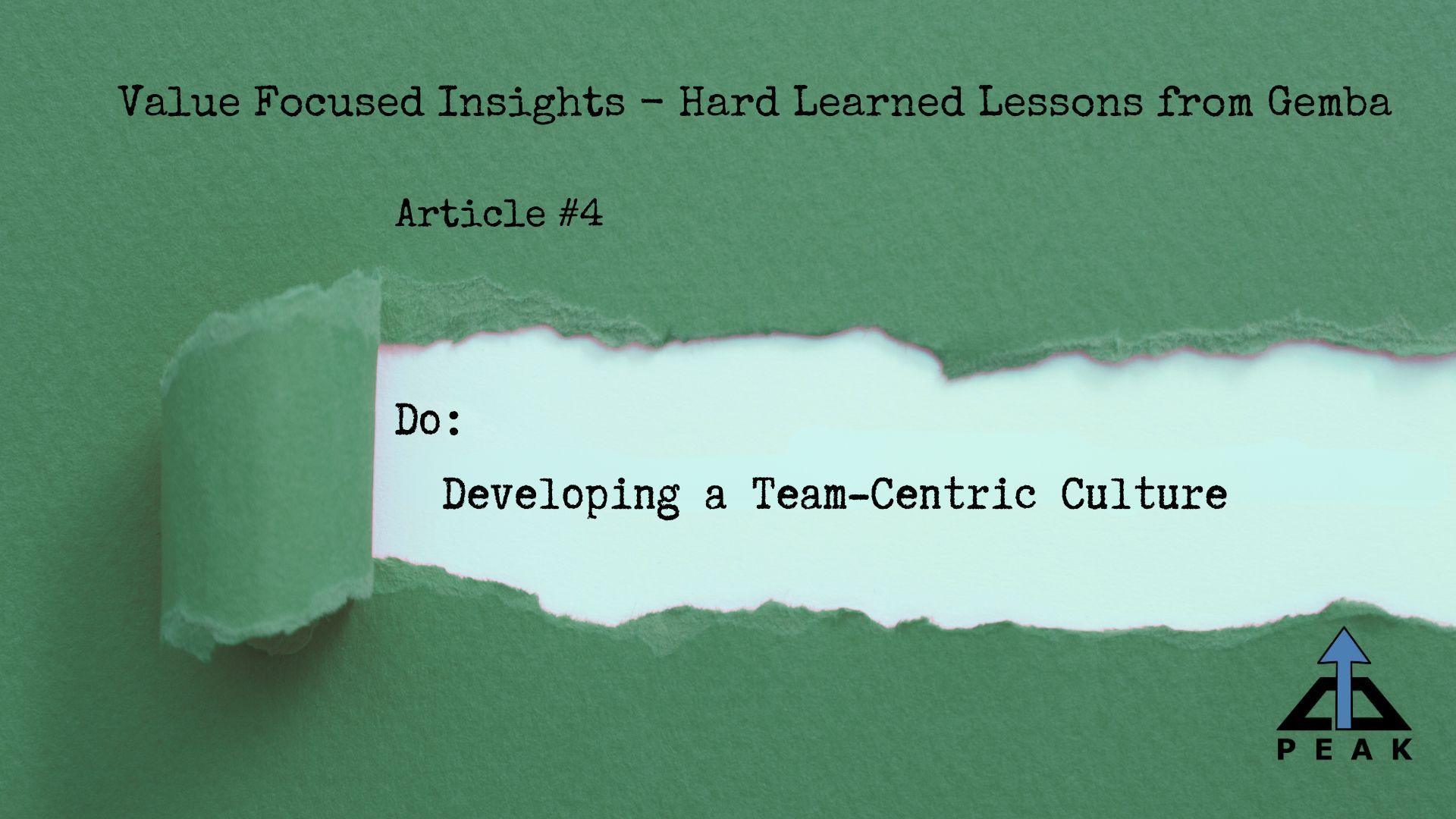
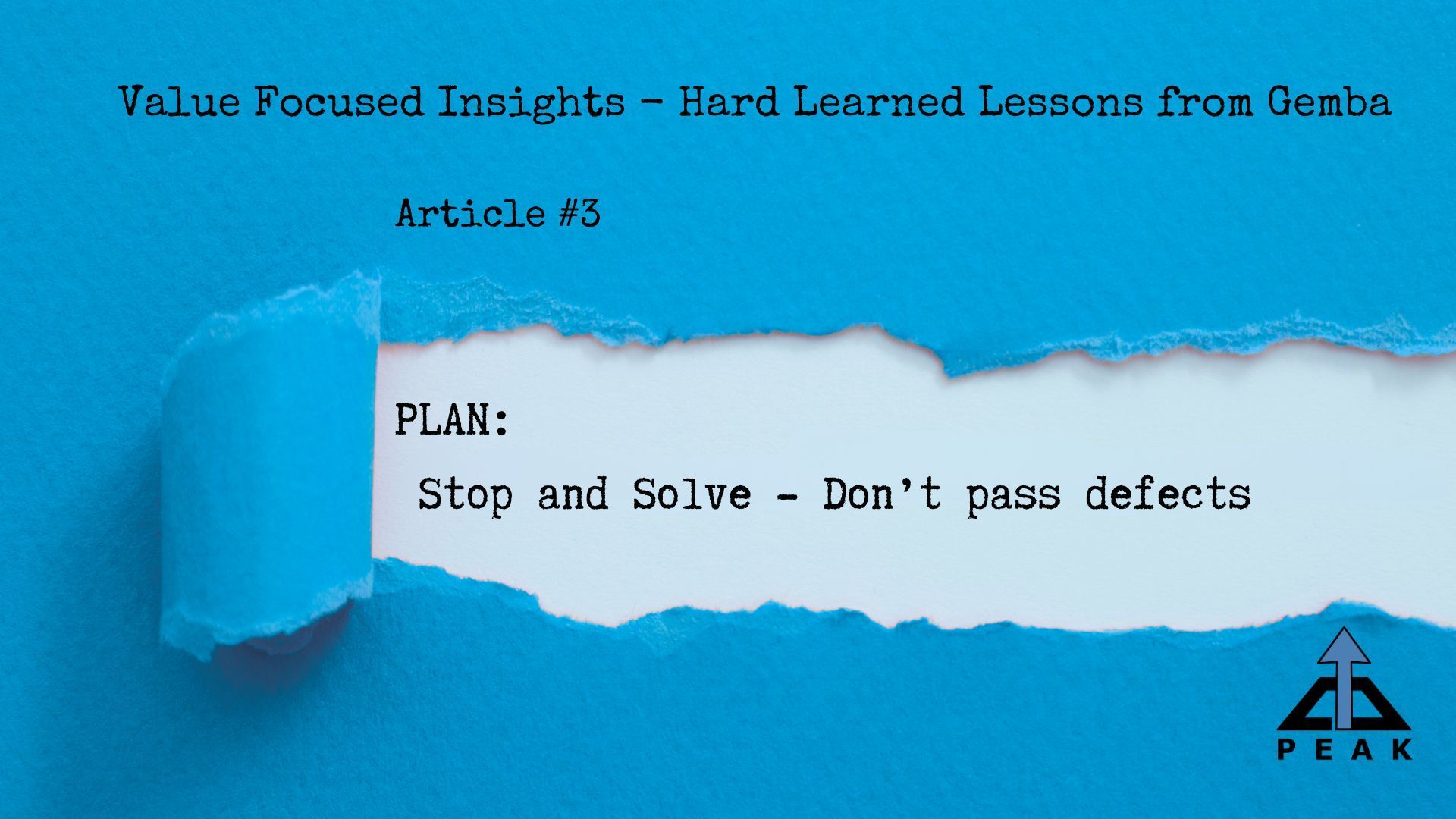
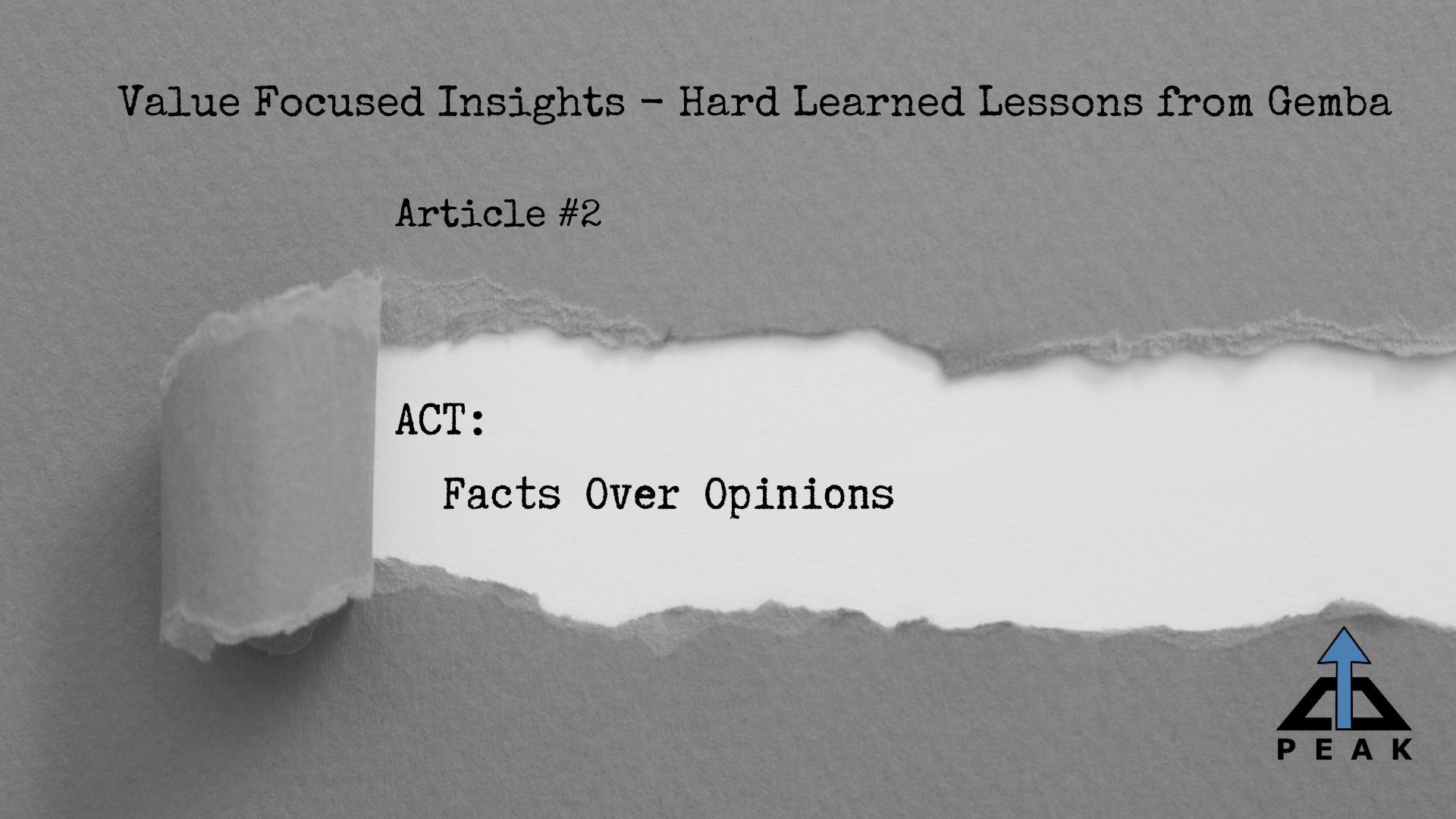
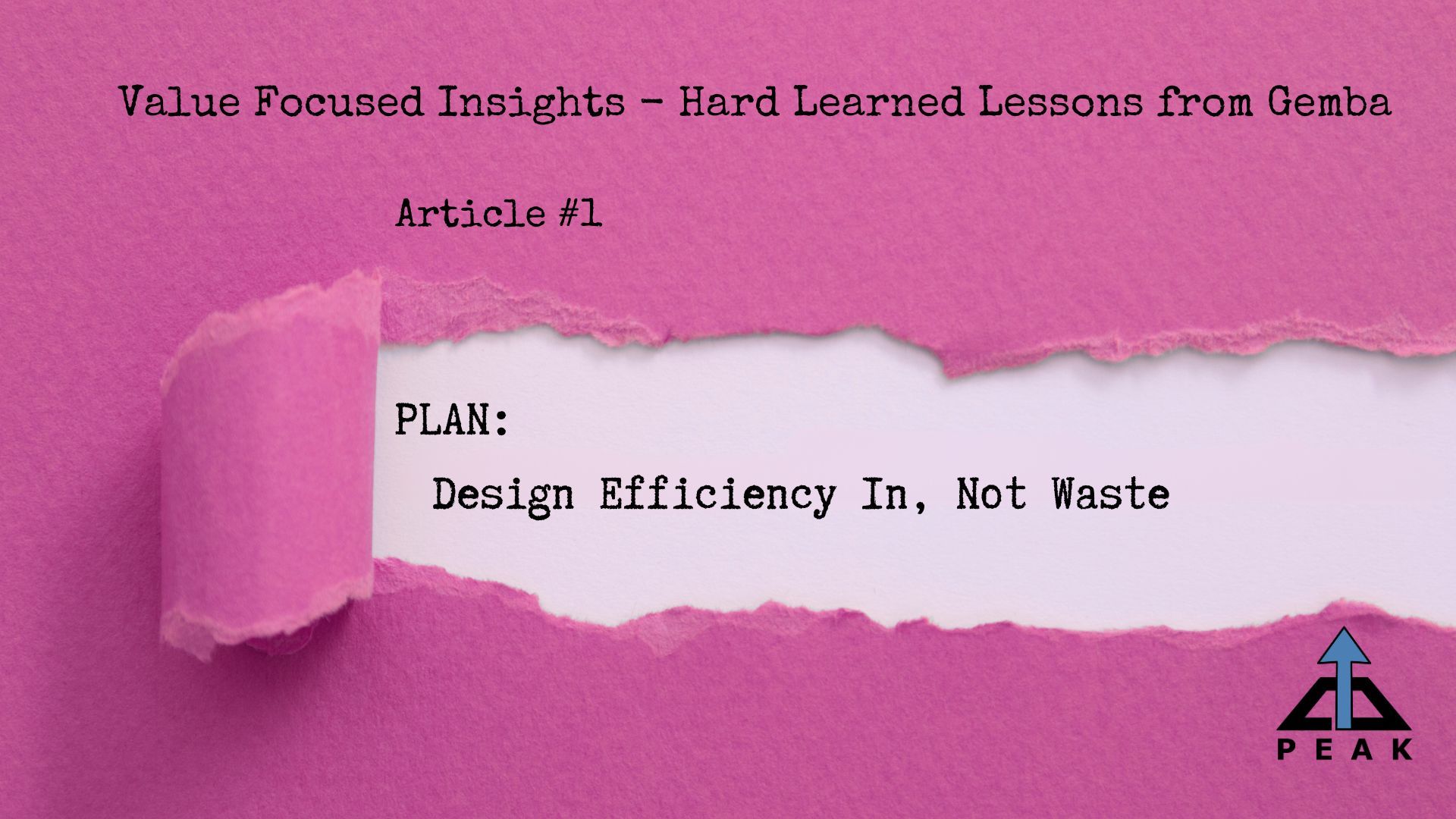