Value-Focused Insight - Design Efficiency In, Not Waste
Annah Godwin
In this week's blog, we start a new series from Peak Productivity titled, "Value-Focused Insights - Hard-Learned Lessons from Gemba. In it, I discuss the need to spend the time and energy to create a plan that builds efficiency in the design and layout phase of the process, not remove waste after the equipment, flow, and processes are set.
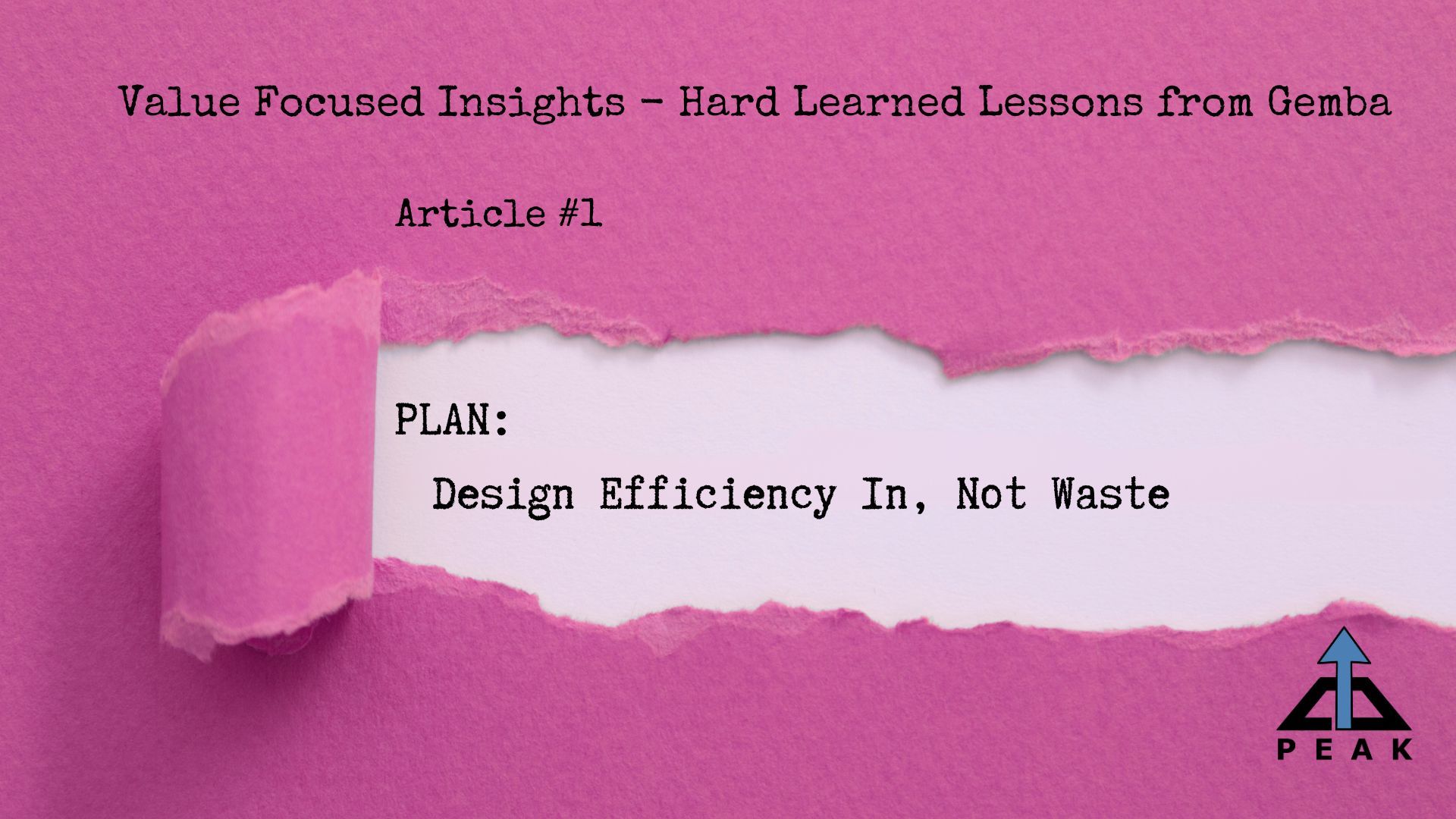
Wack-a-Mole, Tetris, or create a plan? Which describes your approach to lean design and layout?
The goal is to design in efficiency, not waste.
A poor design will haunt you for years to come. How often have you seen a company unbolt equipment and move it to provide more optimum flow and efficiency? I have sat in many meetings where equipment movement was discussed with great passion. Discussions around downtime, loss of production, idle employees, customer needs, cost, etc., with a final decision of “No, just make do with the space you have.” In fact, in my career, I have only seen a piece of machinery moved once to provide better flow.
So that brings up the question, how much time and energy are you spending on designing in efficiency and flow to your process? Does it resemble a game of Tetris or Wack-A-Mole? Does anyone have a 5, 10, or 15-year plan that could be used to model the facility's layout? It will not be a perfect plan, but it will be better than just dropping in equipment based on the given available space. If that is the approach then you are doomed to live with a wacky and inefficient flow, lots of inventory, and excessive material conveyance for the life of those machines and products, which could be 20-50 years.
Why do we do this to ourselves? I believe it is in part due to a false belief that we can drive the waste out later. Now, if you are in continuous improvement this sounds like job security until you retire, but it is a hard journey to take because the process will only be as good as the broken layout will allow. Maybe you can design automated conveyance systems while creating kanbans and visual inventory management, but one-piece flow or batch size reduction will be stymied. A bad layout will add significant material handling costs along with operating costs. Since the company cares about cost, you can’t afford to not spend time, energy, and money to create a great layout.
If a company does invest the time upfront to create a plan and layout for the process and equipment, who is involved or leads the plan? Hopefully, the answer is a cross-functional team, but unfortunately, many times the task is delegated to one person: an engineer, a project lead, or the blueprint owner, etc. All these people are very important to a successful layout or design, but a more diverse team is needed to ensure all perspectives are represented and optimized. What about adding a maintenance team member to work on accessibility to the equipment during repairs or TPM work, a line operator to look at operator controls, inventory drop points, and needed tooling, or someone who conveys materials through the area to look for pinch points, maneuverability issues, or staging areas? Also, include an industrial engineer to look at the overall flow of material, people, and inventory through the area. A good check is to review the overall shape that is formed with the flow of materials through the process steps. O, U, L, or Z are always good choices because they don’t require the products or people to backtrack in the process or travel great distances for the next process. If the overall layout looks like a Wack-a-Mole game, more work needs to be done to optimize the layout and design. The better the design and layout the less waste exists in the process which is the goal.
Please post your thoughts and experiences on lean design and layout in the comment section. As always, if you want to learn more information check out more blogs at Peak Productivity.
Peaks and Valleys.....
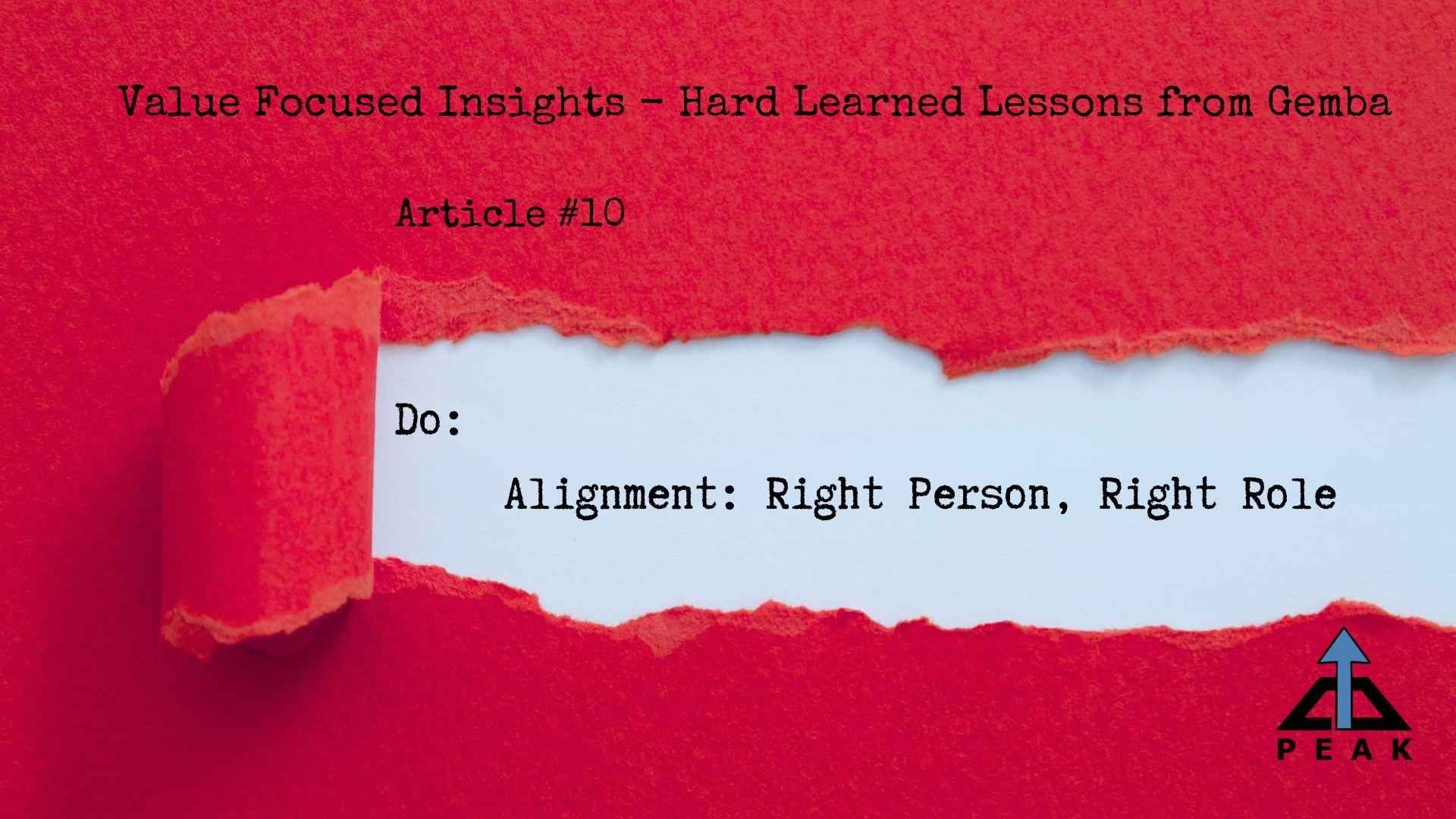
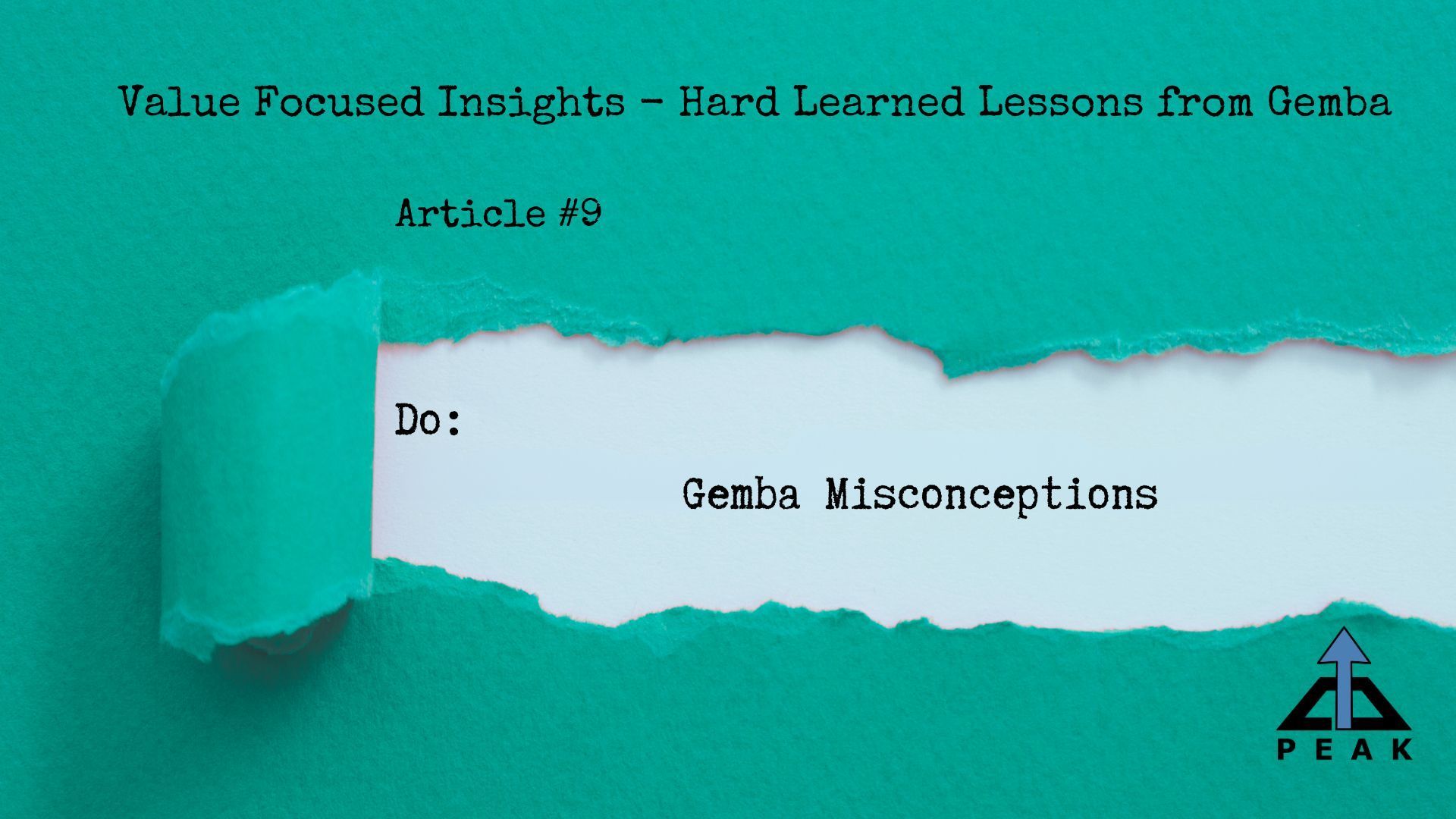
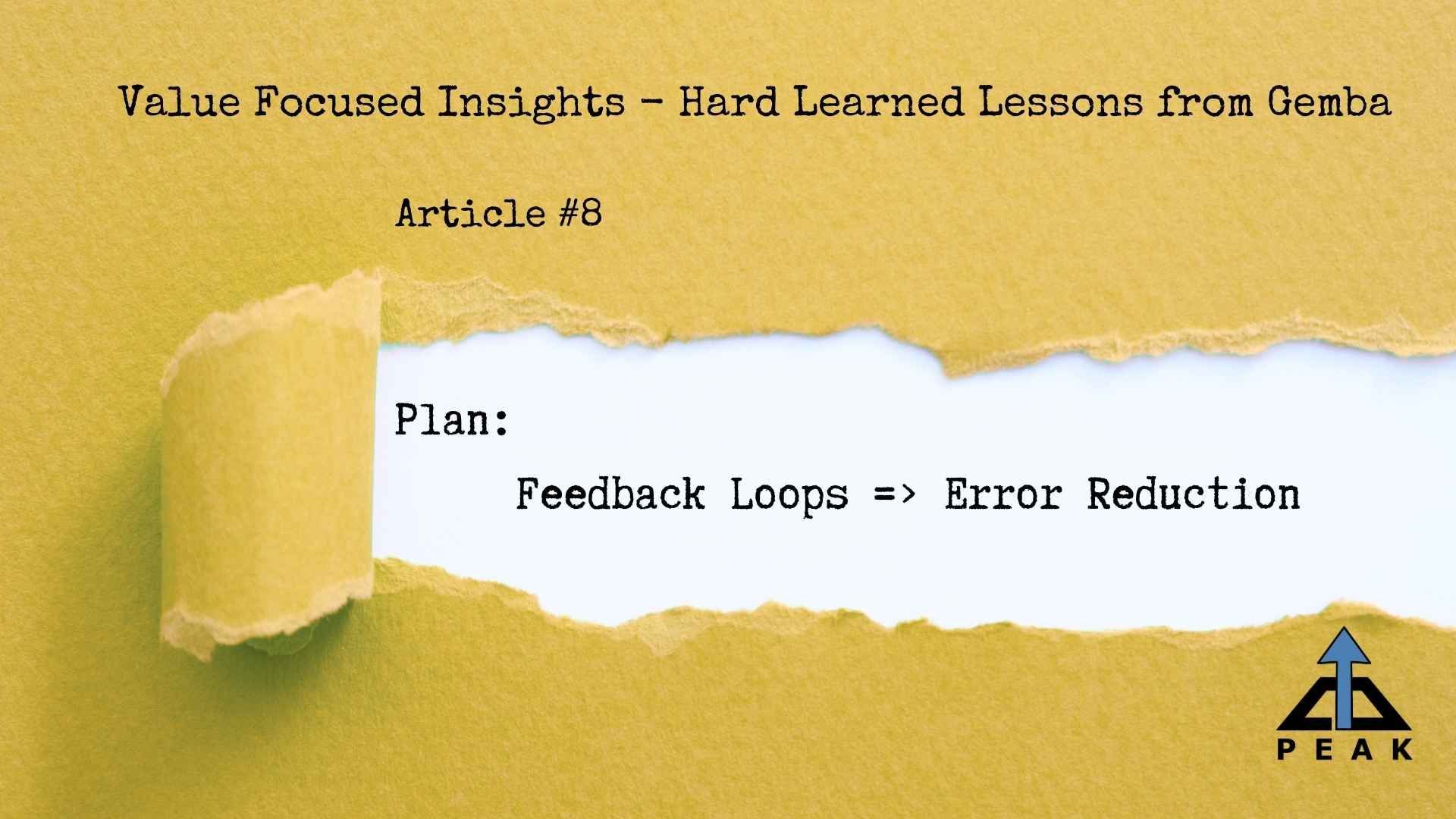
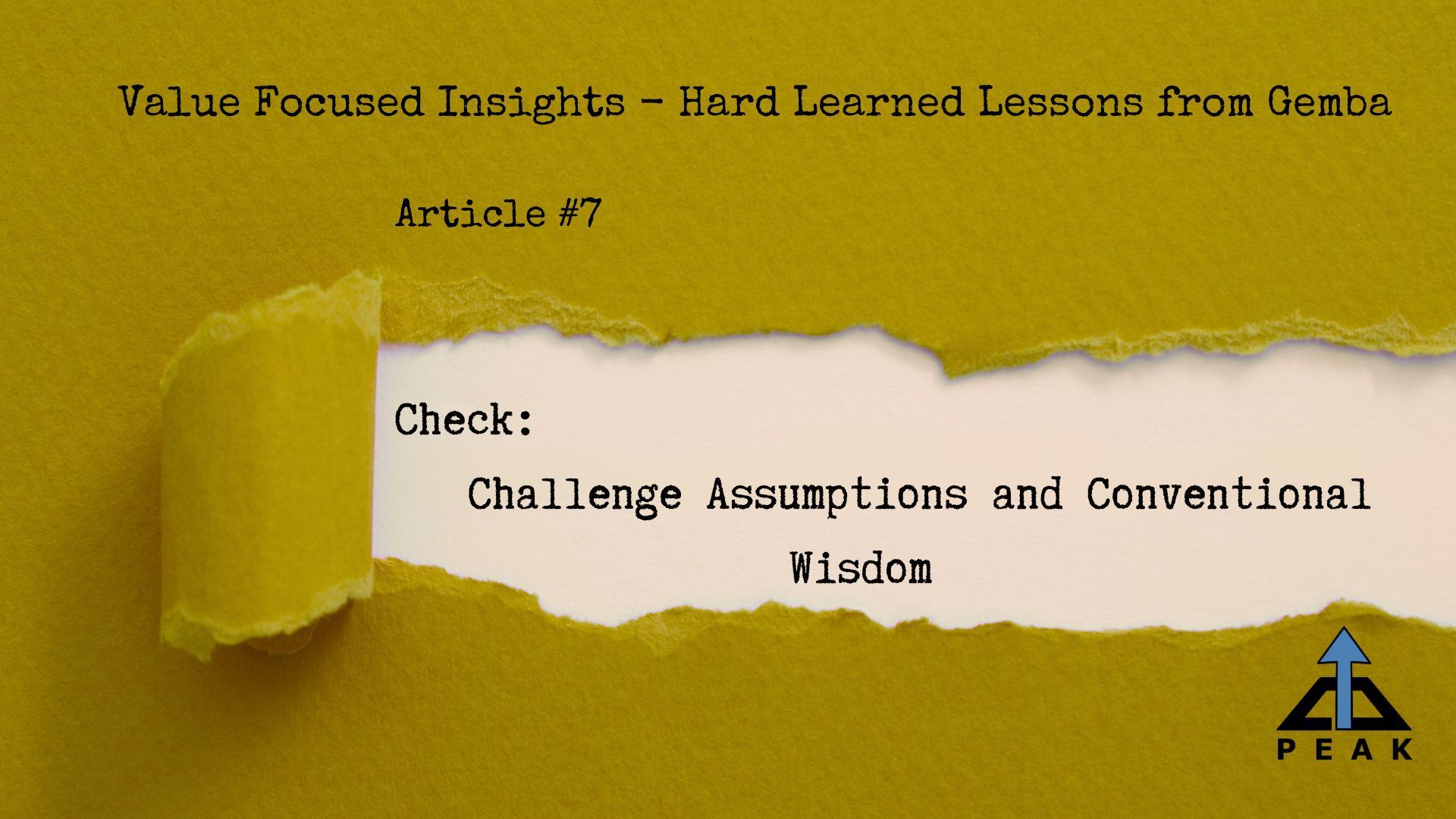
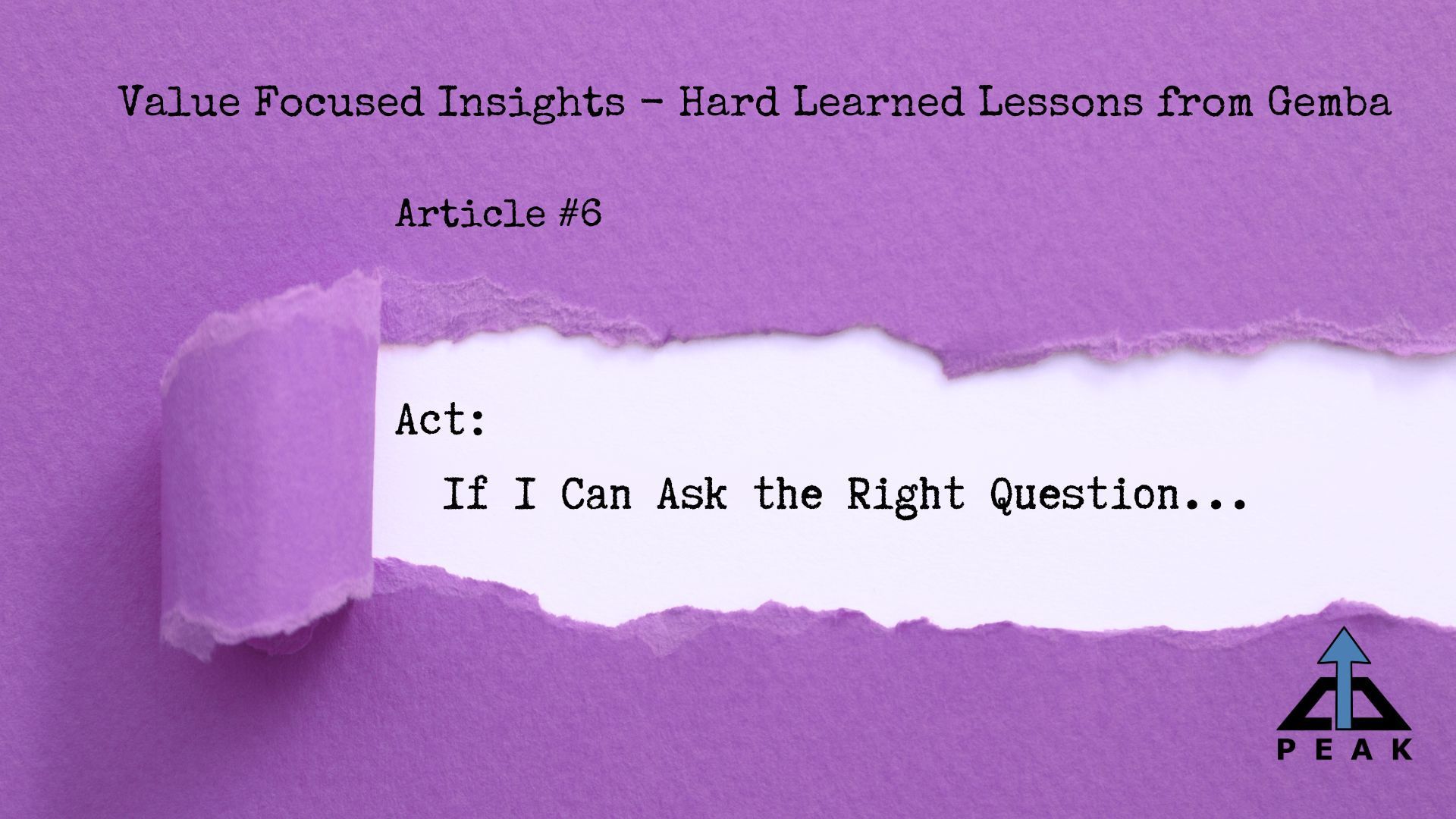
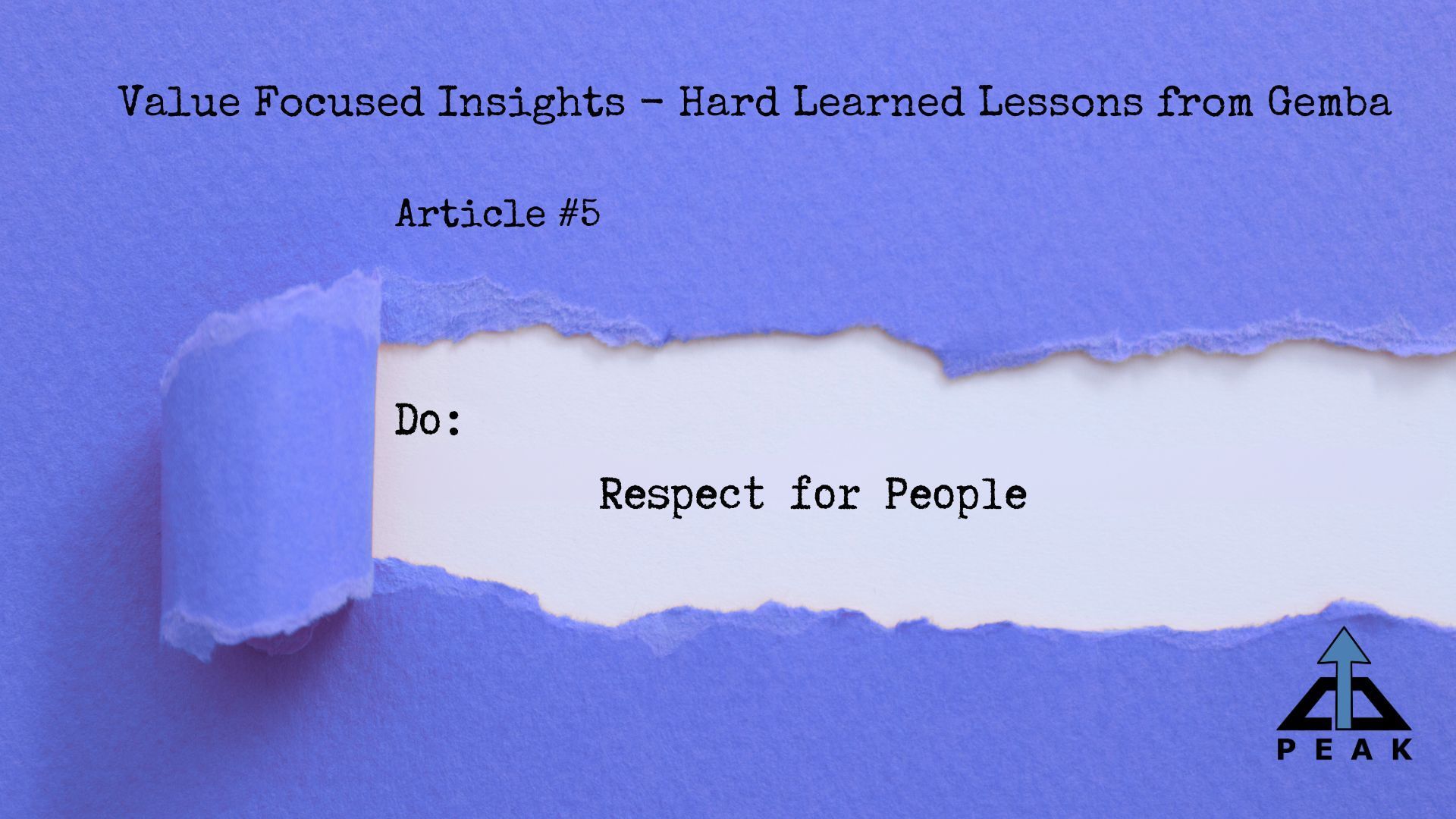
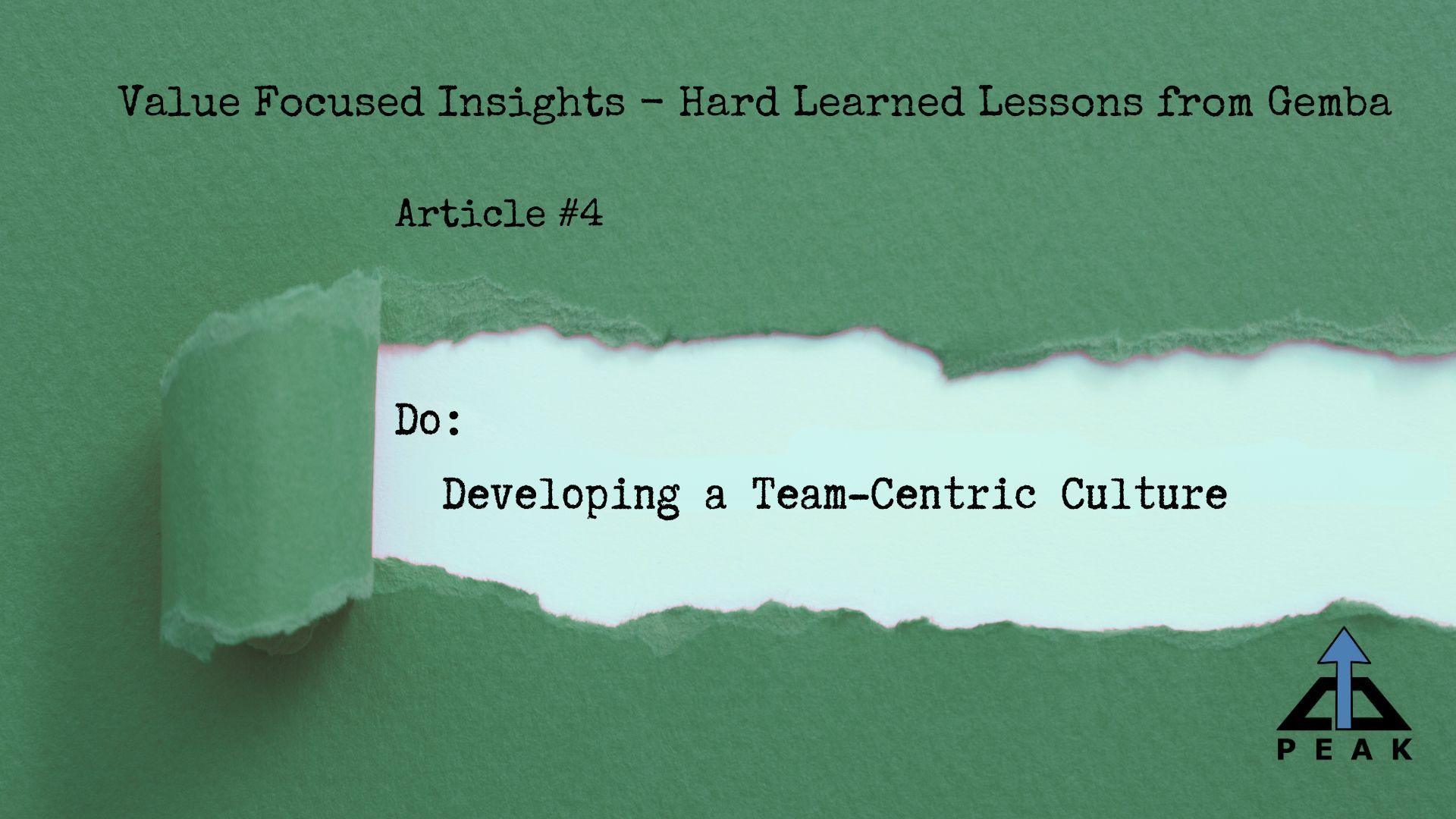
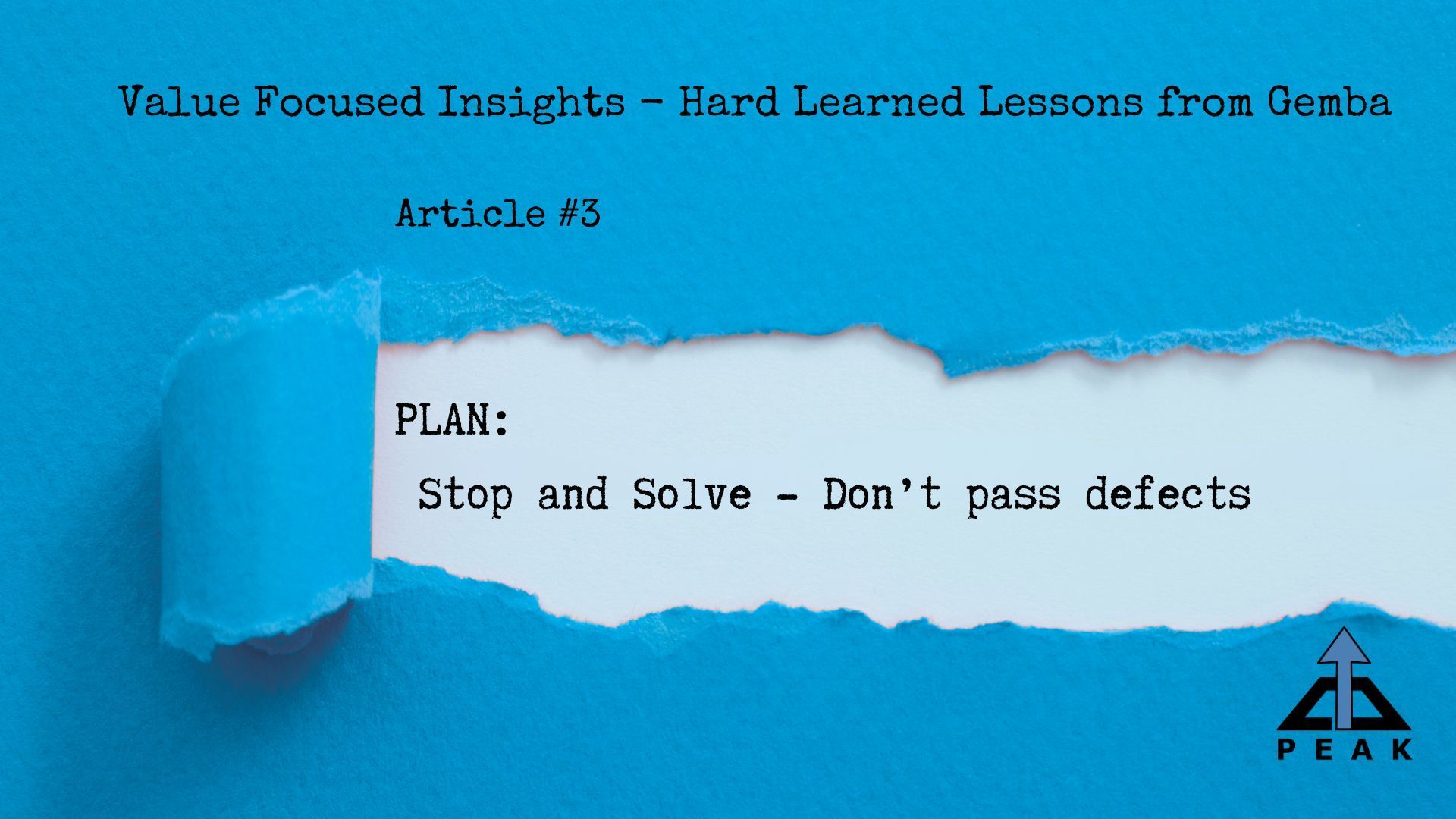
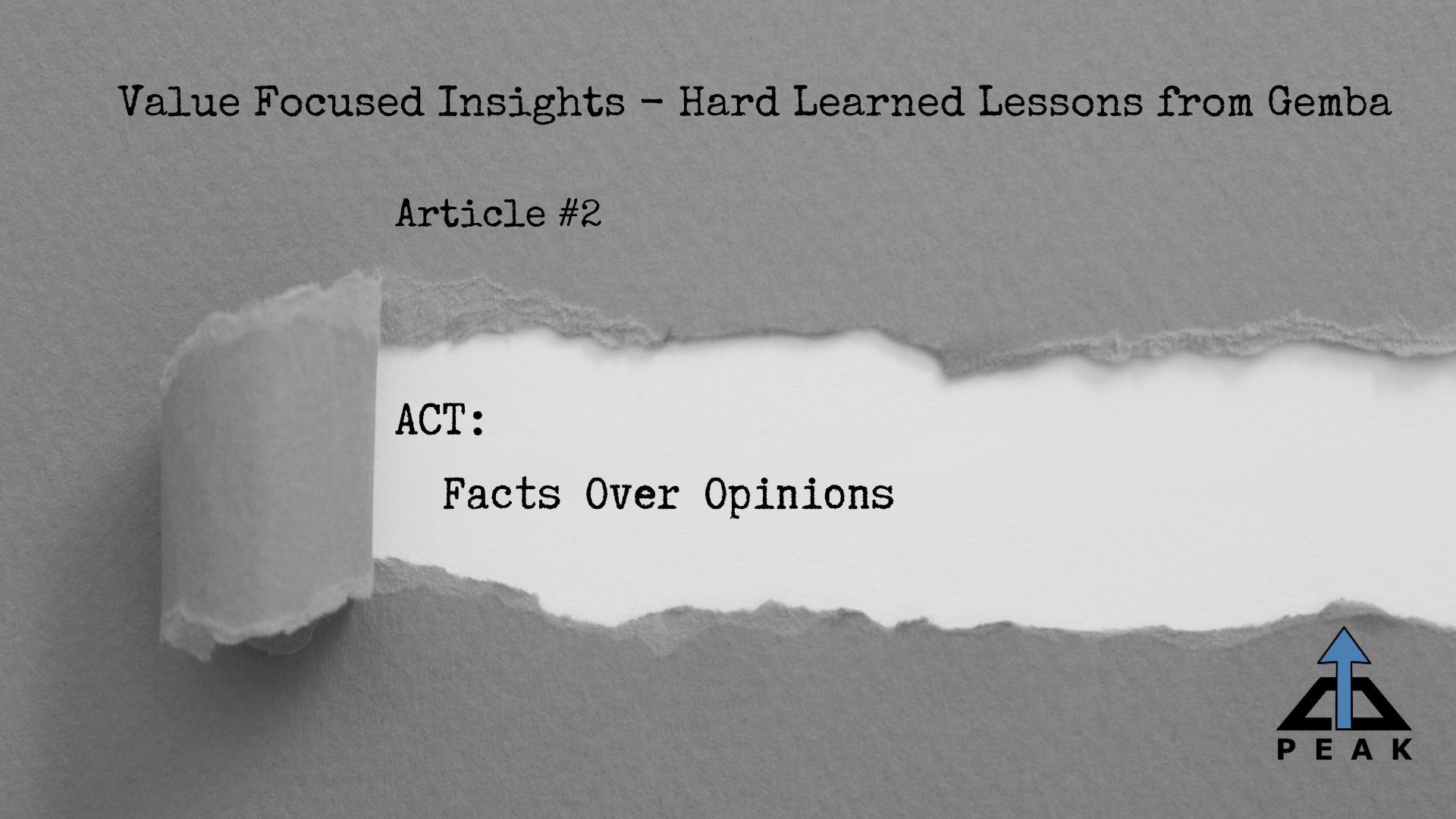
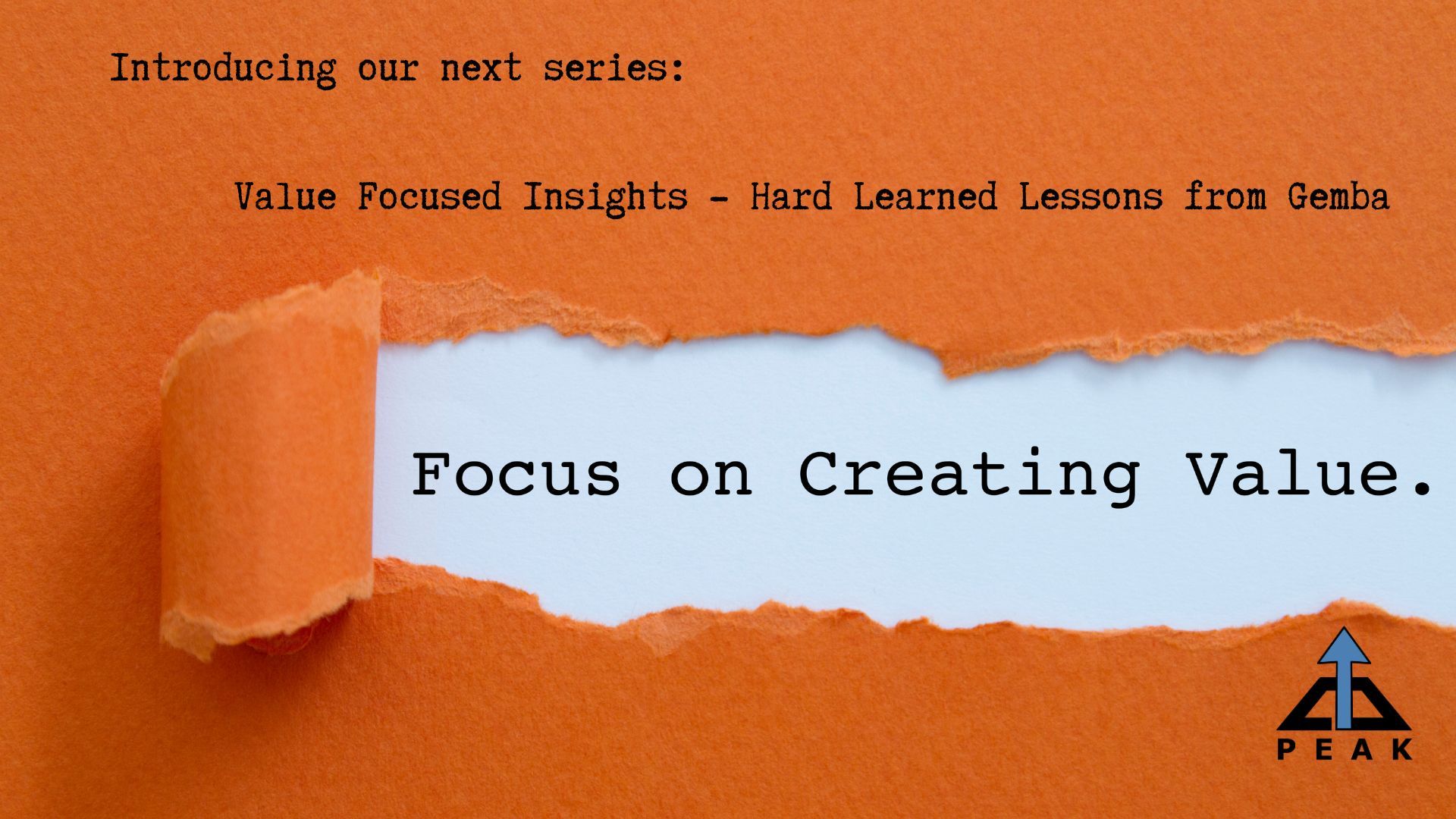