Value Focused Insights – Hard Learned Lessons from Gemba
Tim Upchurch
There is an alarming statistic that 90% of lean transformations will fail. According to McKinsey, 74% of private-sector business initiatives will not achieve their objectives. In the public sector, similar types of projects can have failure rates as high as 80%.
At best, your next change initiative has around a 70% chance of failure. How do you change the odds in your favor?
Join Peak Productivity as we provide the answers in our upcoming series of articles, entitled: "Value Focused Insights – Hard Learned Lessons from Gemba".
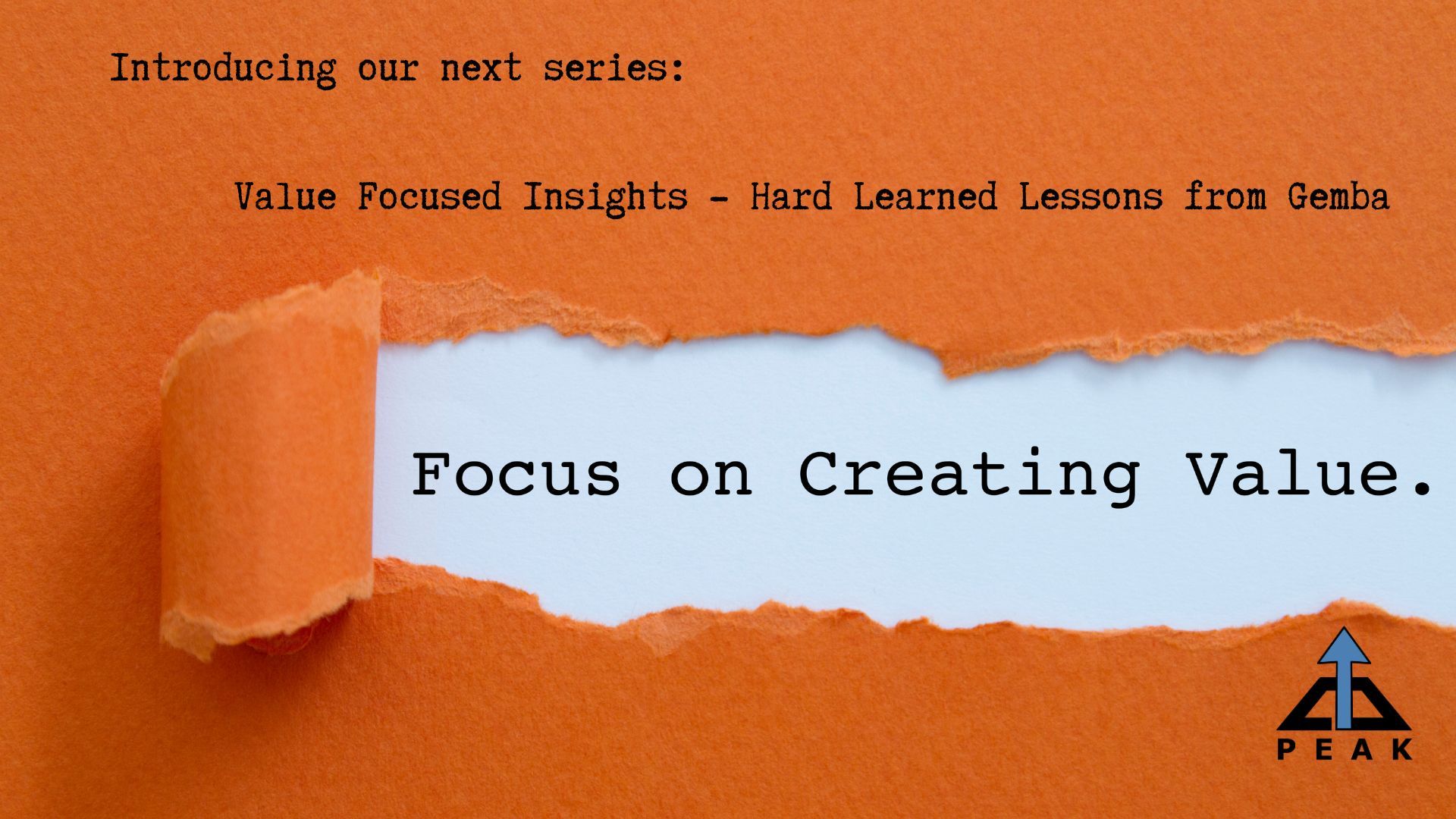
The Reality
There is an alarming statistic that 90% of lean transformations will fail. According to McKinsey, 74% of private-sector business initiatives will not achieve their objectives. In the public sector, similar types of projects can have failure rates as high as 80%.
These are the complex, large-scale strategic plans we often are a part of in our professional lives. In the beginning, we are all pulled into a large room where we are given promises for all the pain and stress that will be removed from our daily jobs, provided with the customary water bottle emblazed with the approved project name/slogan, and introduced to a fantasy timeline for execution. We are told how everything will be different this time because we are going to be using XXX (insert your favorite buzzword – AI, synergy, deep diving, etc.). On opening day, every fan is excited by the prospect of the coming season. But by the end of that first day, half of us could already be frustrated due to a lack of execution or poor design.
At best, your next change initiative has around a 70% chance of failure. There are a variety of reasons you will not succeed according to the literature. Every organization’s unique problems are clumped together into 4-6 major categories.
It would be helpful to develop countermeasures for these before you begin, but the literature is written at a very high level and not always relevant or actionable. The conclusions are not specific enough to help you because your situation is unique, and the business landscape constantly changes. But you must do something to achieve financial targets, right? So, millions of dollars and resources will be wasted on the next round of inherently flawed programs.
What you need is a way to generate more value, in a manner that is both faster and cheaper. It is often said that you can only have two of the following: FAST, GOOD, CHEAP. That statement is wrong – it is possible to have all three simultaneously. You will need to think differently about your problem. Even then, it’s not always easy to do. Good news, there are those who know how to crack the code.
The Decision
With that issue in mind, Peak Productivity decided to introduce a new series of articles/blogs to provide help on how you can supercharge your improvement initiatives. We will let you in on how to generate multiple returns in value and do so on a budget – both in time and money.
These are not just simple guides to follow; they are the blueprints, the profound lessons, the secret sauce, the "aha" moments, and the best tactics/strategies that we have either developed or learned from some very smart people over our 50 years of collective lean working experience. In this series, we will explore lean thinking and improvement scenarios through the PDCA lens, providing you with these best practices, shortcuts, hacks, and force multipliers that have consistently delivered value.
Our goal will be to communicate the deeper level lessons in a way that you can use them effectively today, but without having to spend many years on practice or reflection. We hope to do so in a manner that clearly delivers both fundamental and actionable knowledge for you but allows you to retain the inherent humility that comes with time.
Plan
In the "Plan" phase, we start by unraveling how to generate value through stability. One higher level goal is we want to always support our customers. What better way than to develop stable and robust processes that will consistently achieve the needs of our customers? Everyone has internal and external customers – we need to understand how to effectively meet all demands and requirements, 100% of the time. To achieve that, we will develop hypotheses about our processes. Some of the higher level needs to be addressed will be reliability, quality, flow, and system designs.
Do
In the course of fulfilling demand, we will need to continually test our hypotheses. Normal variation and randomness will identify weak points in our systems and create fluctuations in output. To counteract this, we must introduce strong people systems to support our "Do" phase, to effectively react and counter for standard deviations. It's more than just introducing concepts like backing-up someone; it's about developing the chemistry and understanding the unique dynamics that transform a group of individuals into a high-performing team.
- How and when do they react to adversity?
- What is the standard approach to reduce overcorrections?
- What is my deliverable?
We will explore detailed strategies for fostering engagement, initiative, collaboration, and a shared commitment to lean excellence. We must uncover the subtle yet powerful elements that enable meaningful cultural shifts. These will become magnified when working across functional and organizational boundaries.
Check
As we transition into the "Check" phase, speed of execution becomes our focus. But it isn't just about speed; it's about integrating seamlessly with the “Do” systems for impact. Understand how an action-biased approach, coupled with a strategic sense of urgency, accelerates learning and the improvement process. Dive into strategies for swift, effective tests that stand up to scrutiny. Every data point comes at the cost of valuable resources. We need to make sure our processes can take advantage of and learn from every cycle.
It is vitally important not only to know when to react, but also when NOT to react. Knowing what we think we know is true – testing it to make sure that it is still valid. We need to respect the process, but not be afraid to grab the reins when needed to keep it under control.
Act
In the "Act" phase, we unveil the lessons of leverage. It's not just about implementing solutions; it's about strategically placing them for system level leaps in effectiveness. We will explore how targeted improvements, when strategically applied, create a ripple effect, multiplying their impact across the entire value stream.
Staying within the "Act" phase, the focus shifts to the Lean Innovation Process. Discover how to foster an environment where experimentation is not just encouraged but becomes the lifeblood of your lean journey. There is no end to improvement, and we should never rest on our laurels. Learn the art of embracing failures as opportunities for learning and growth. And always make sure you cross the finish line and don’t get distracted with the next thing too early.
Conclusion
As we discuss the power of these lessons, we invite you to not just read but to engage, reflect, and apply. Each lesson has been tested in the real world and stood up to the challenge. Stay tuned for the first installment.
We appreciate feedback. Please share your thoughts and experiences related to these upcoming lessons in the comments section. Let's build a dynamic repository of insights and wisdom that contributes to the collective understanding of lean principles and continuous improvement. Stay tuned for a series that promises not just knowledge but actionable strategies for transforming your Lean journey.
Peaks and Valleys.....
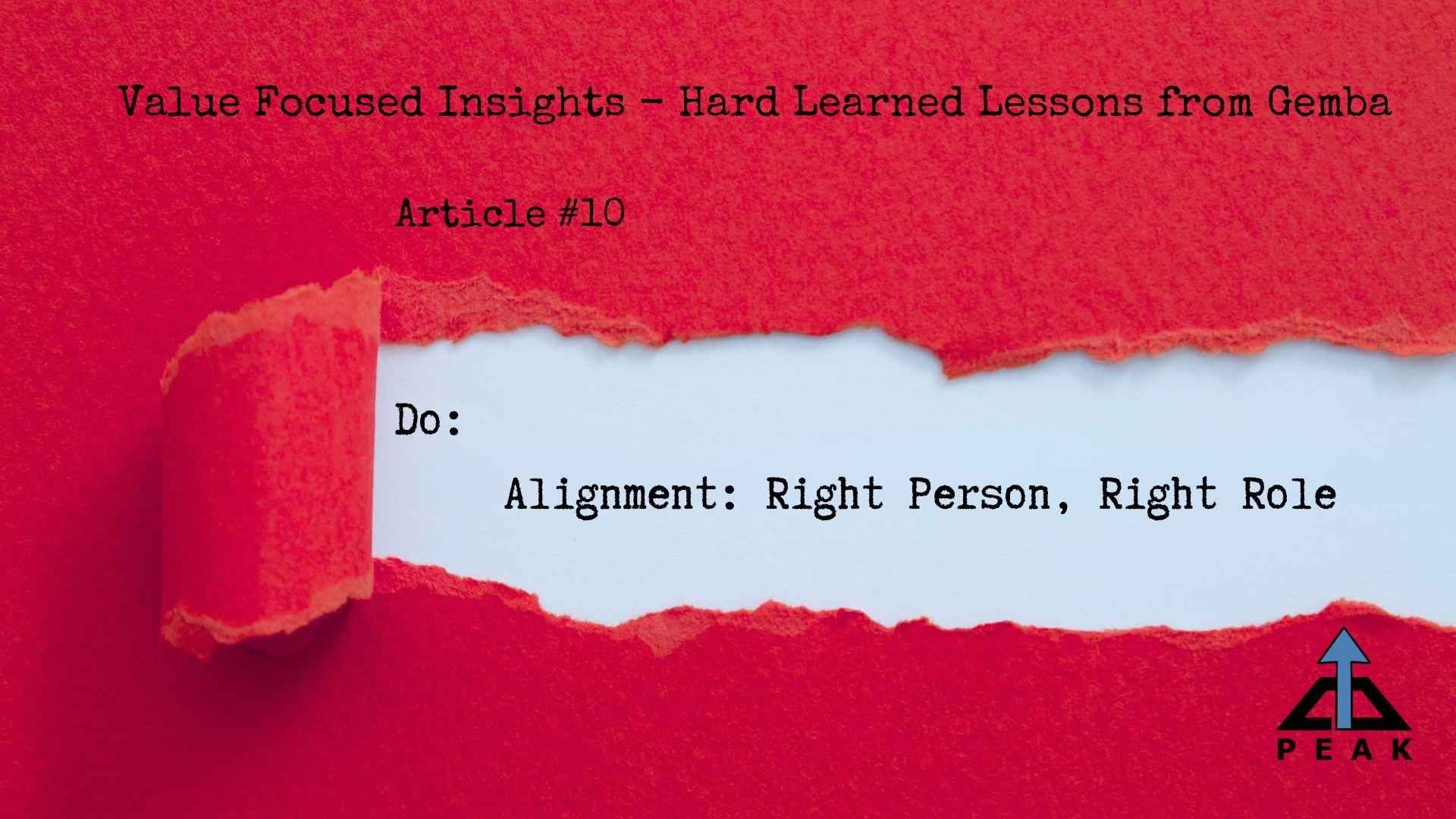
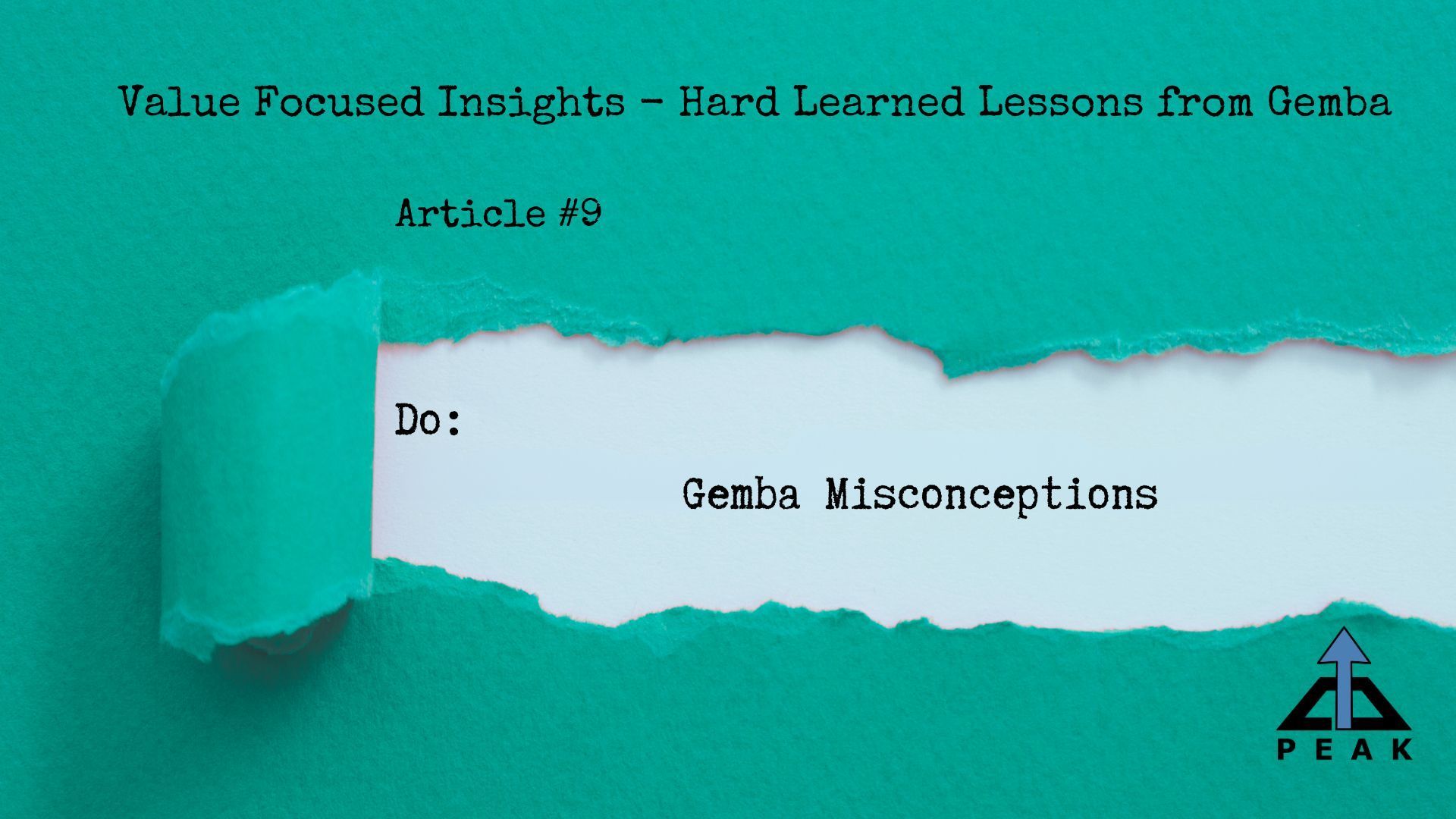
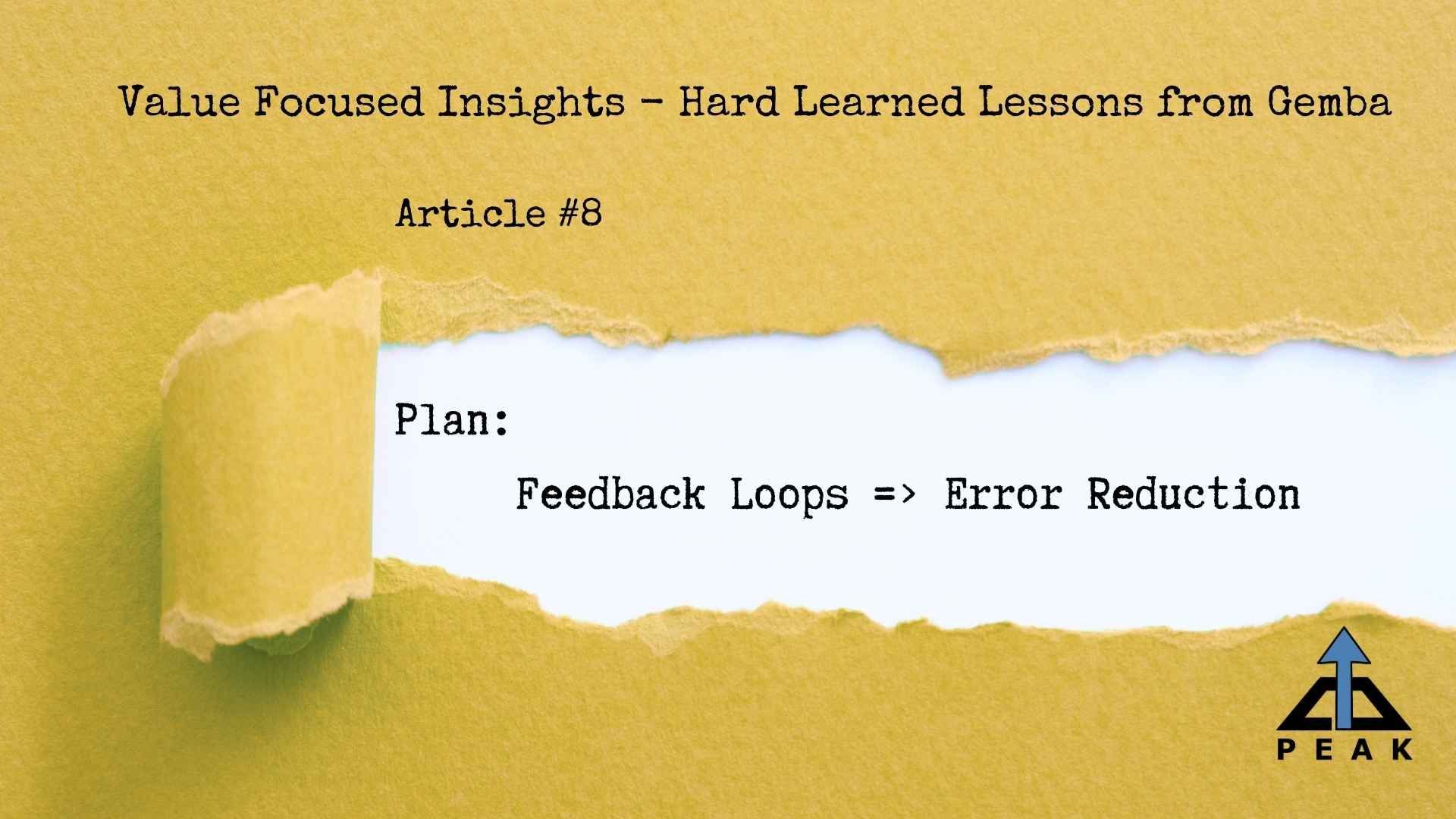
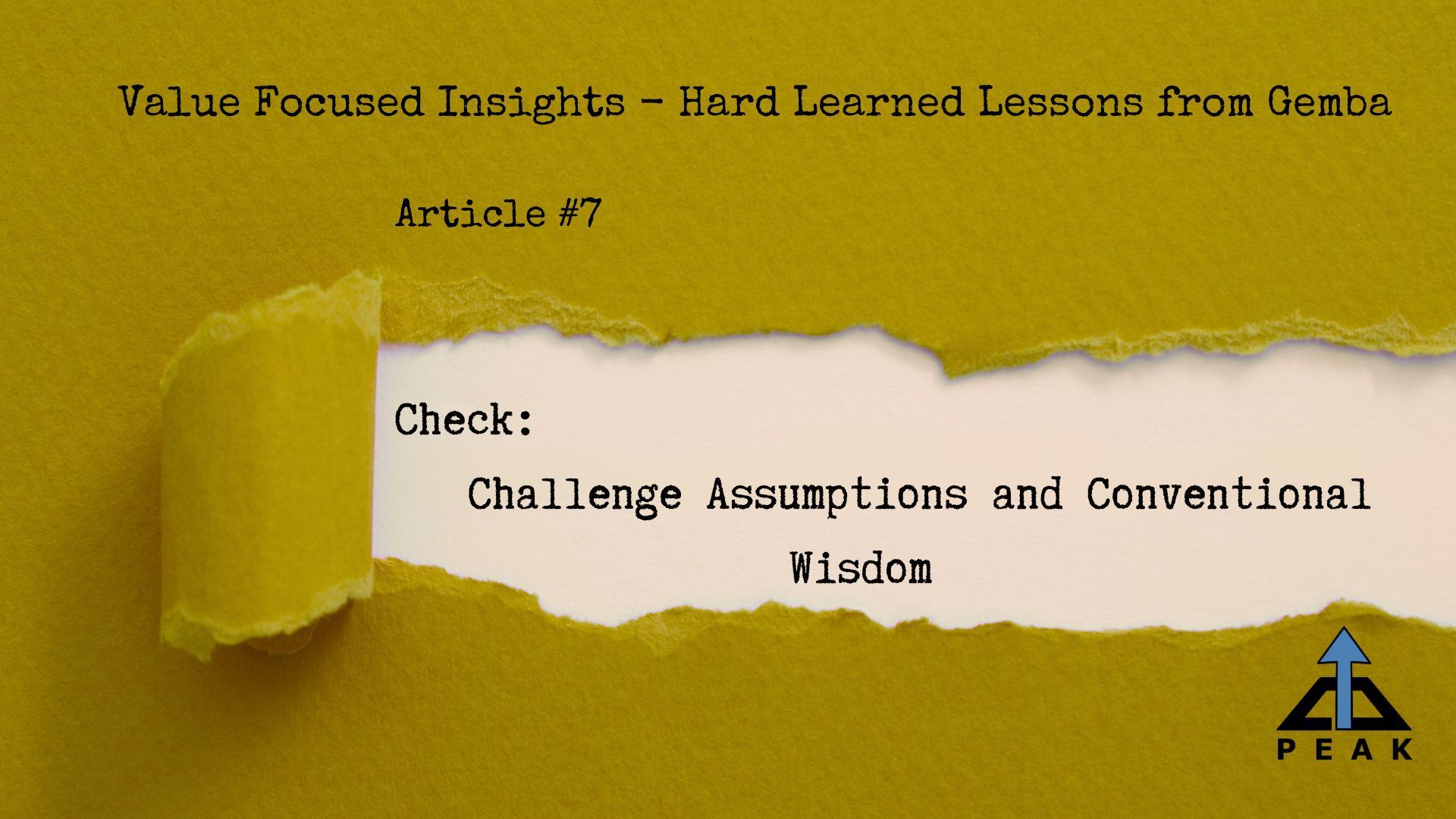
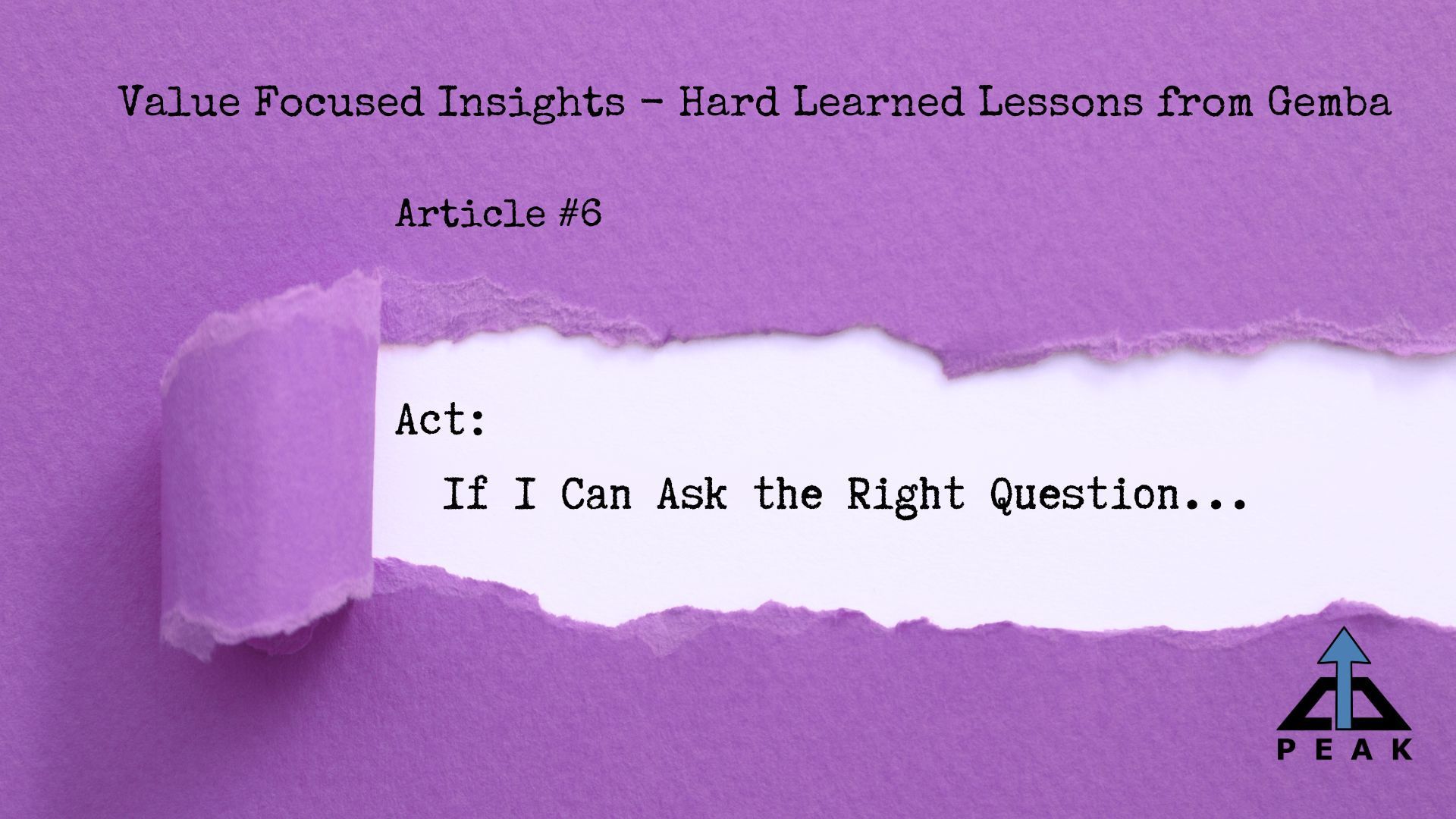
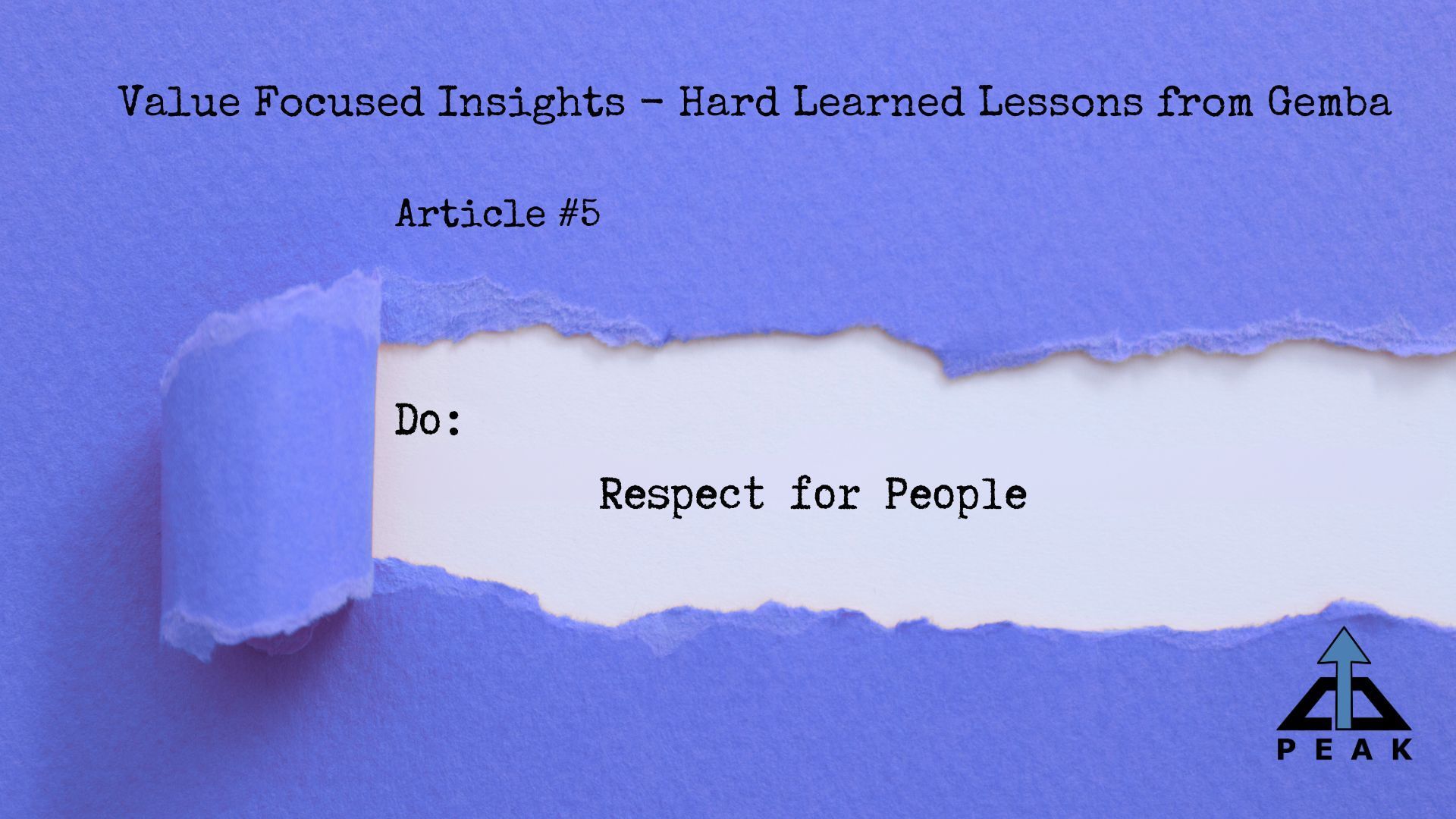
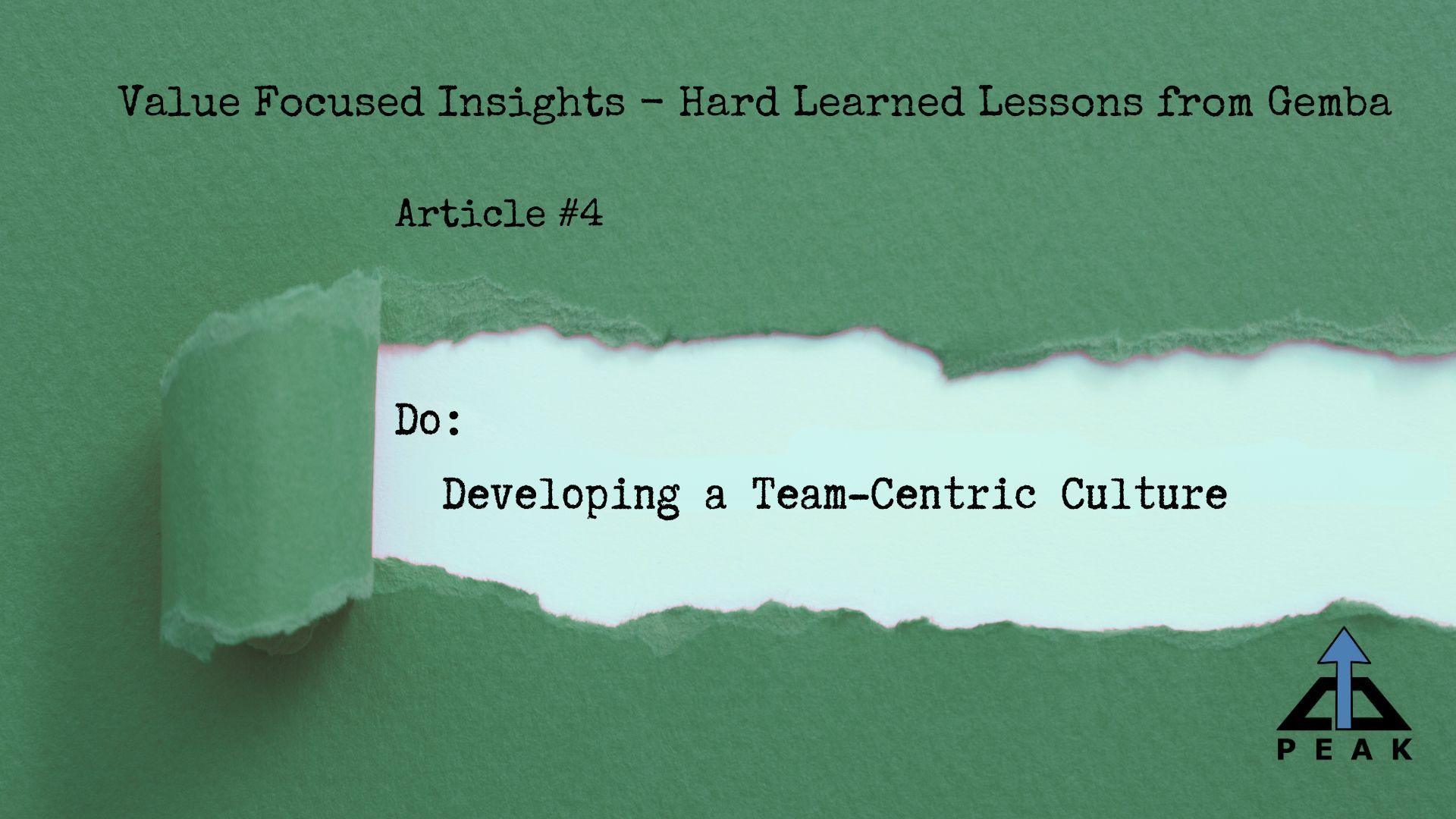
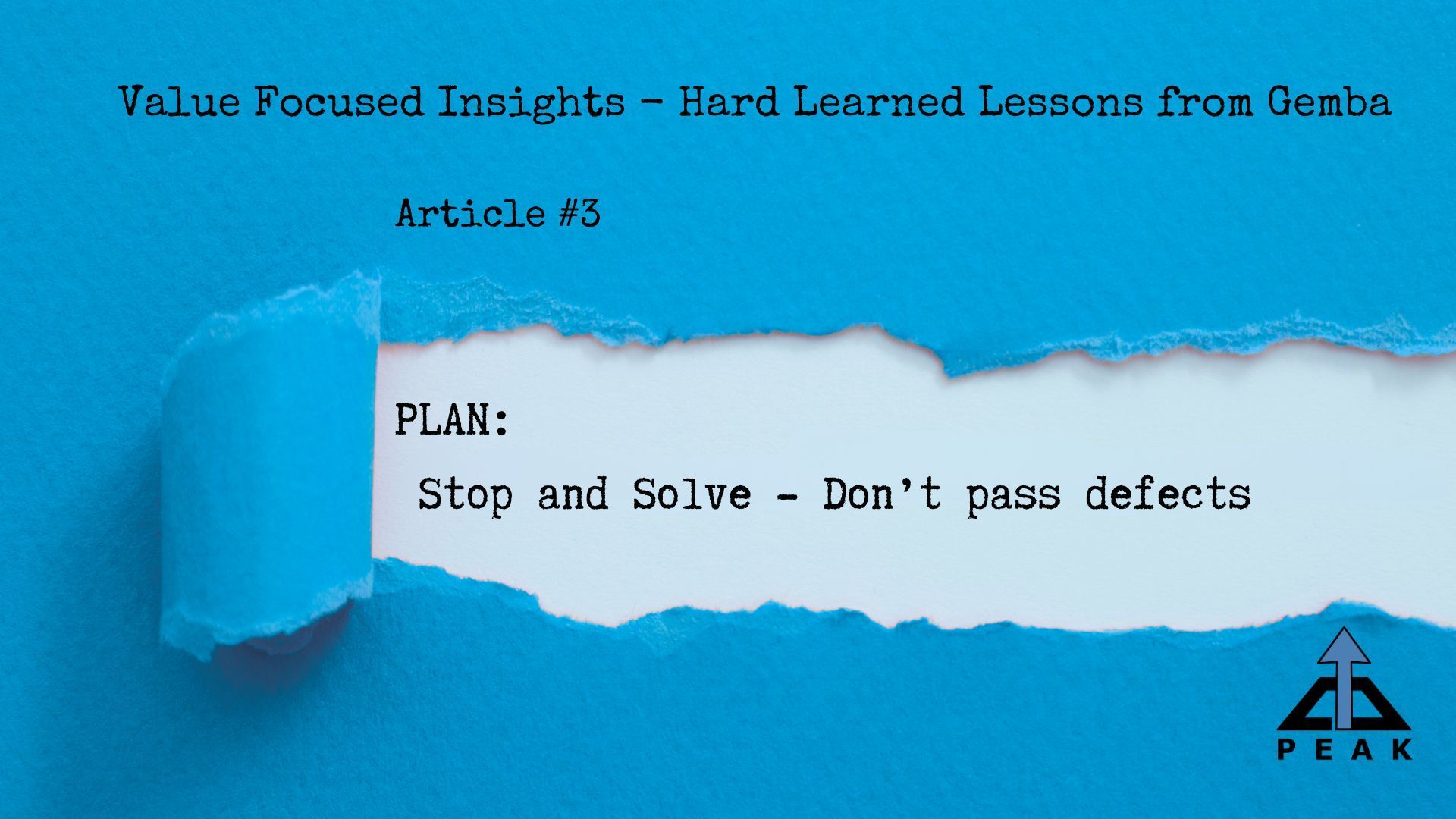
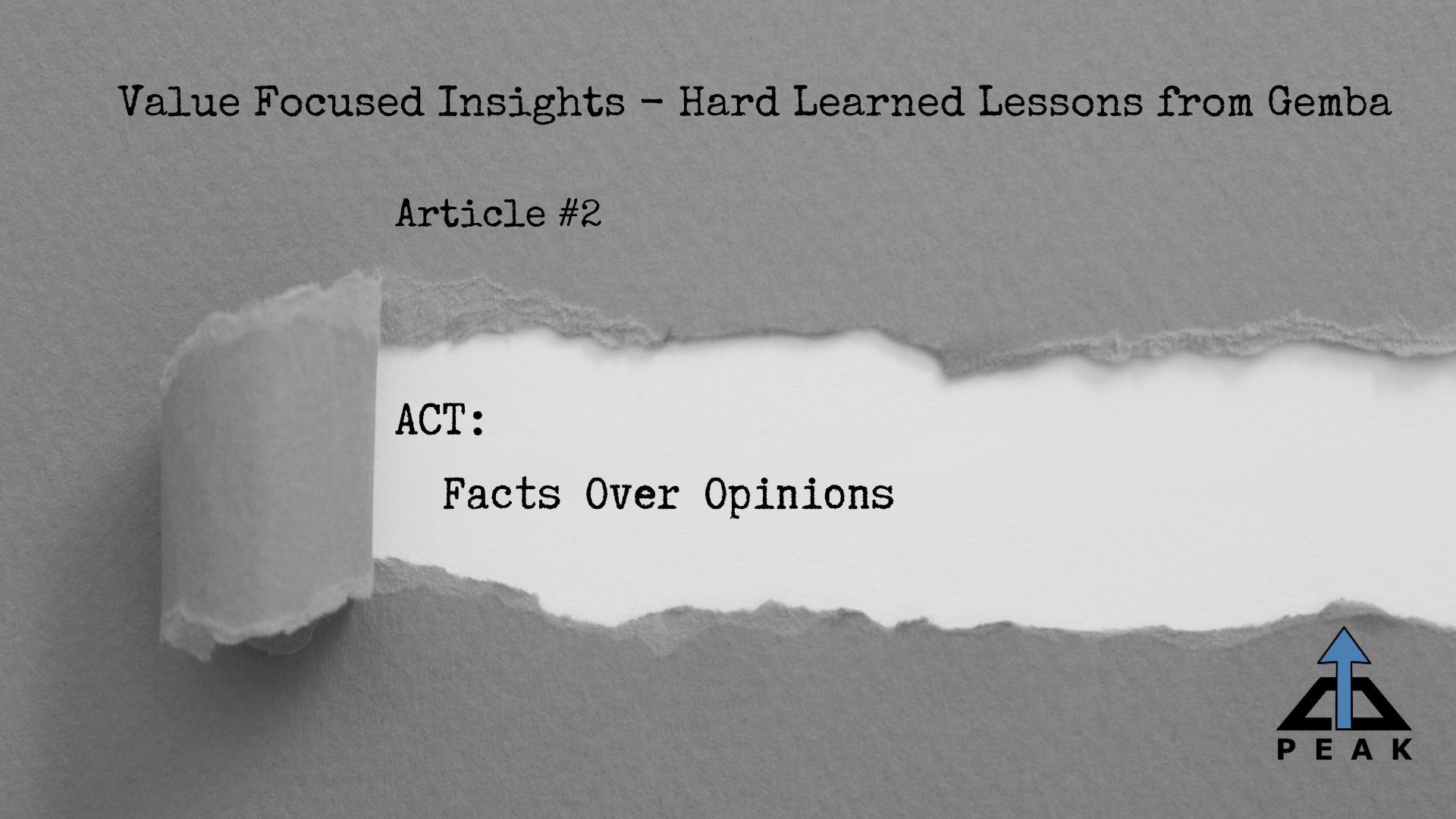
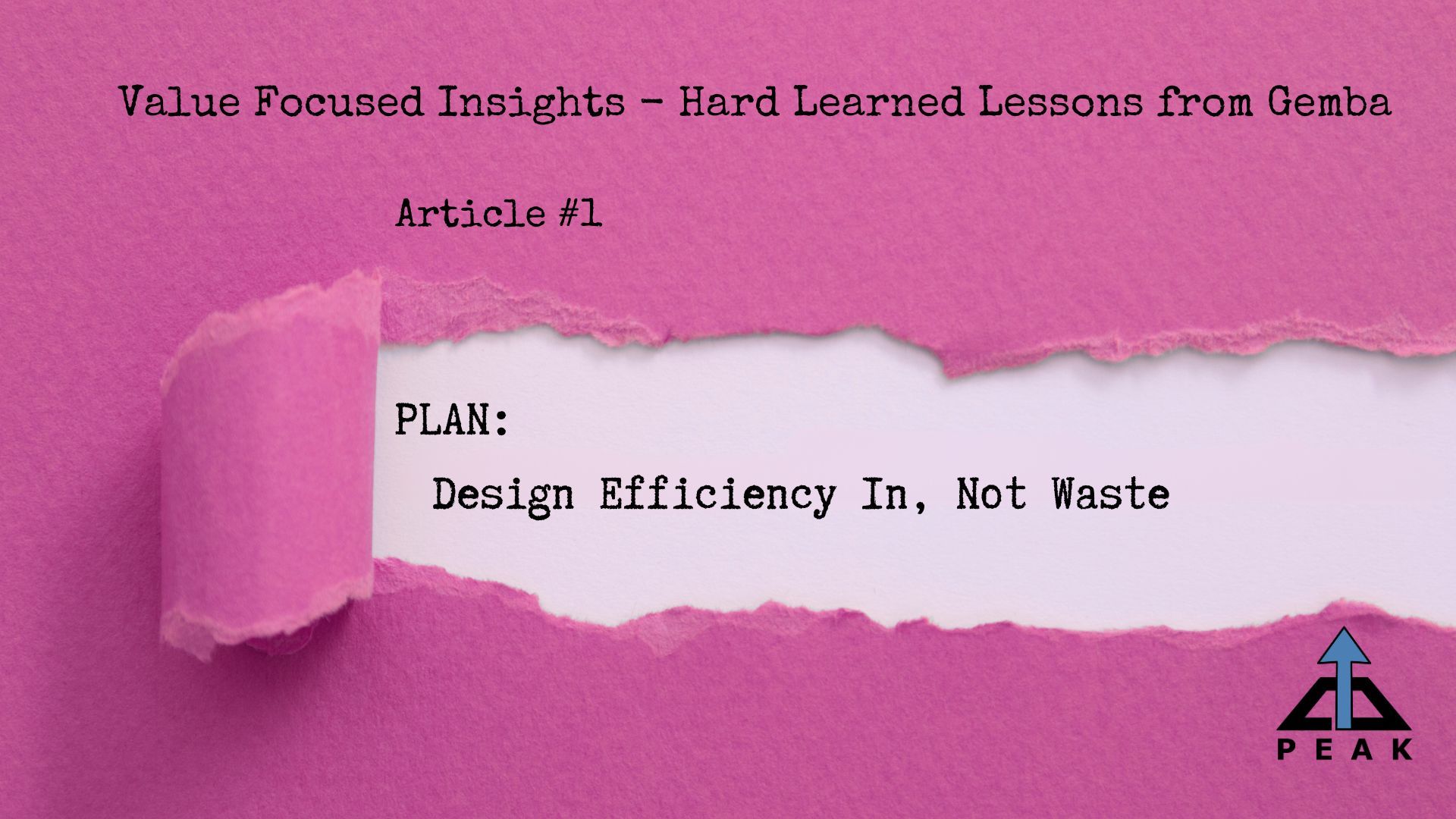