Value Focused Insights - Stop and Solve
Annah Godwin
In today’s world of “go, go, go” the idea of stopping is hard to imagine. This same “go, go, go” mentality also applies in the business world. As managers, executives, owners, and employees, we find it difficult to stop, even when it is obvious that we should. This is especially true with defects and the process failures that allow them to occur. In this blog, I will discuss stopping the errors by building processes to prevent defects from getting to the customer.
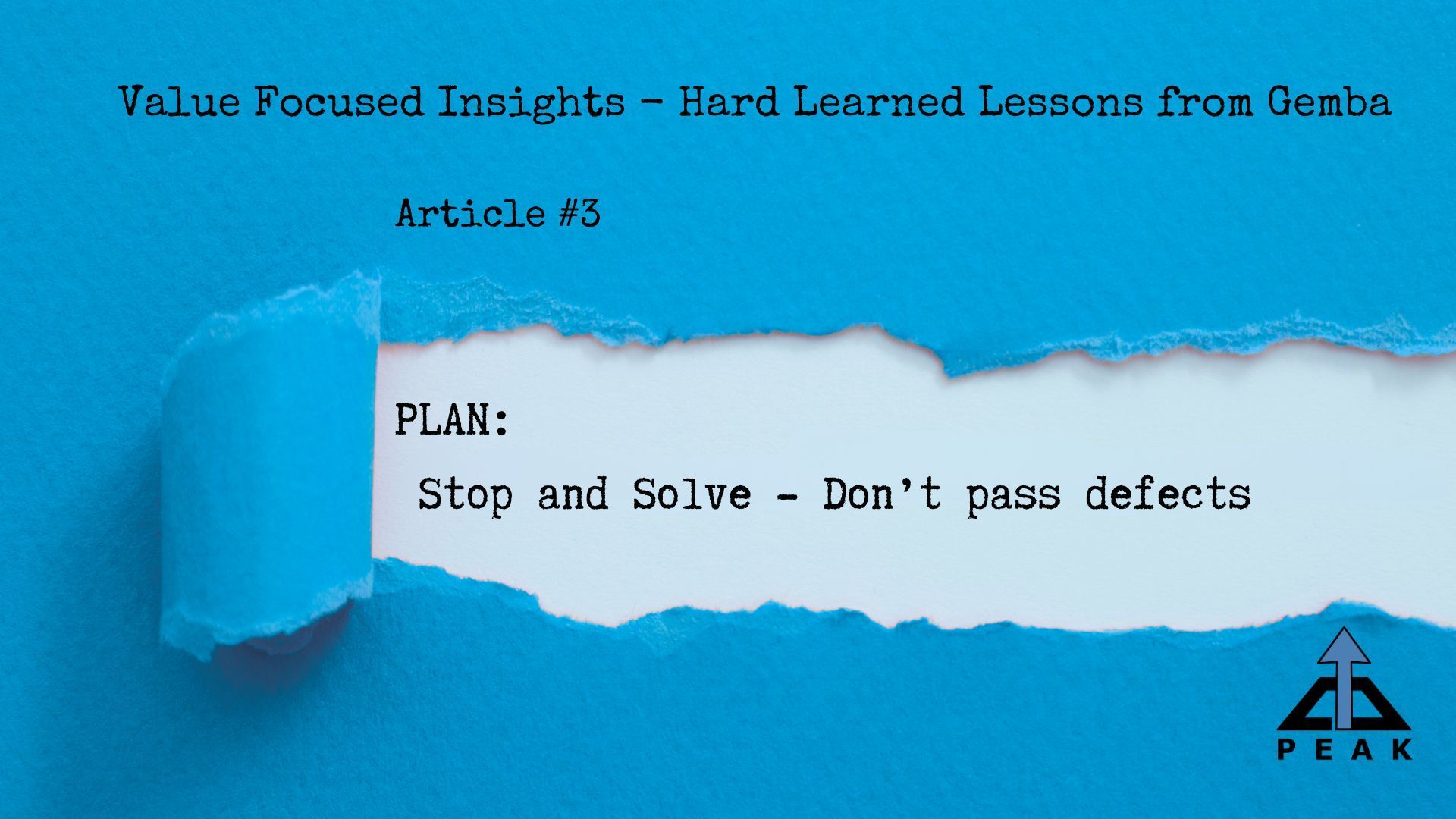
When a defect occurs is it better to focus on fixing the defect or eliminating the error? Most defects happen because of an error, which may be caused by a machine, material, or person, and may be the result of an omission of a step or doing something incorrectly. With time and resources, you try to salvage the part via repairs or reworks, but what prevents it from occurring? I bet the same issue continues to occur until we address the error, which is why it is vital to eliminate the root cause as soon as possible by stopping and solving the problem.
In my experience rarely do we stop and solve the problem. In fact, stopping the processes is usually seen as a last resort, instead of the first step in corrective actions. We are content for lines to continue running materials and parts, as we add extra people to provide costly inspections and quality rechecks, all with the hope the customer doesn’t receive a bad part. Sometimes that works, and sometimes, even with all the extra effort, poor quality makes it to the customer. However, there are proven ways to break this cycle and save us from defects.
Start shifting from the old motto of “Catch the defect” and move to the new motto “Can’t make a defect” by applying these actions.
- When errors and/or defects occur stop the process and investigation. The real-time information gathered helps to determine potential causes that could contribute to the defect. Look at the equipment, raw materials, work instructions, and work orders, along with discussing with the operators, material handlers, inspectors, and others involved to understand the circumstances that led to the error. It takes some time, but the more you follow this pattern of problem-solving, the deeper your knowledge will grow and the quicker you will move to problem resolution and error elimination.
- Ask the right question. The question is not how to stop producing defects but rather how to prevent errors. If we only focus on eliminating the defect, we will be stuck in an endless game of Wack-a-Problem. We will focus on moving resources from problem to problem and while some may be resolved, you will find some of the same issues may reappear in the future. As you transition from catching defects to eliminating errors, you will find the number of defects, errors, and line stops will begin to drop as root problems are fixed. Remember, we stop the line, so we don’t have to stop the line. Take the hit on your metrics today, so tomorrow the processes run more efficiently with higher quality and improved metrics.
- Design the process so that mistakes can’t be made. This is one of the hardest goals to achieve within a process. I don’t think I have seen one that was 100% successful because processes seem to always evolve or devolve. A process is either developed from a lack of planning and standardization with lots of variation and errors or is designed from the ground up. Over time, shortcuts, poor training, and out-of-date standards can introduce process creep to even the best-designed processes, which in turn increases errors and, thus, defects. If you find mistakes, errors, and omissions happening today, it is time to insert inspections throughout the process that are quick, real-time, and cover 100% of the products. Problems will be highlighted that lead to the detection of defects and errors immediately through poke-yokes, built-in tests, feedback loops, and source inspections. These tools protect your customer from poor quality arriving at their doorstep.
Customers want a quality product, part, and service so building a culture that encourages stoppages in the process when poor quality occurs helps save time, energy, and money for the organization while keeping the customer happy. In this environment, your process will continually improve as your team members move toward problem solvers that not only fix the defect but address the error to prevent future occurrences. The next time you have a quality issue or defects take a different approach by stopping the line and addressing the real issue, the system that allows the error to happen. You will find that stopping is the best way forward.
I hope you enjoyed this blog post and found the information helpful and informative. I would love to hear your feedback, thoughts, and opinions on it.
Peaks and Valleys.....
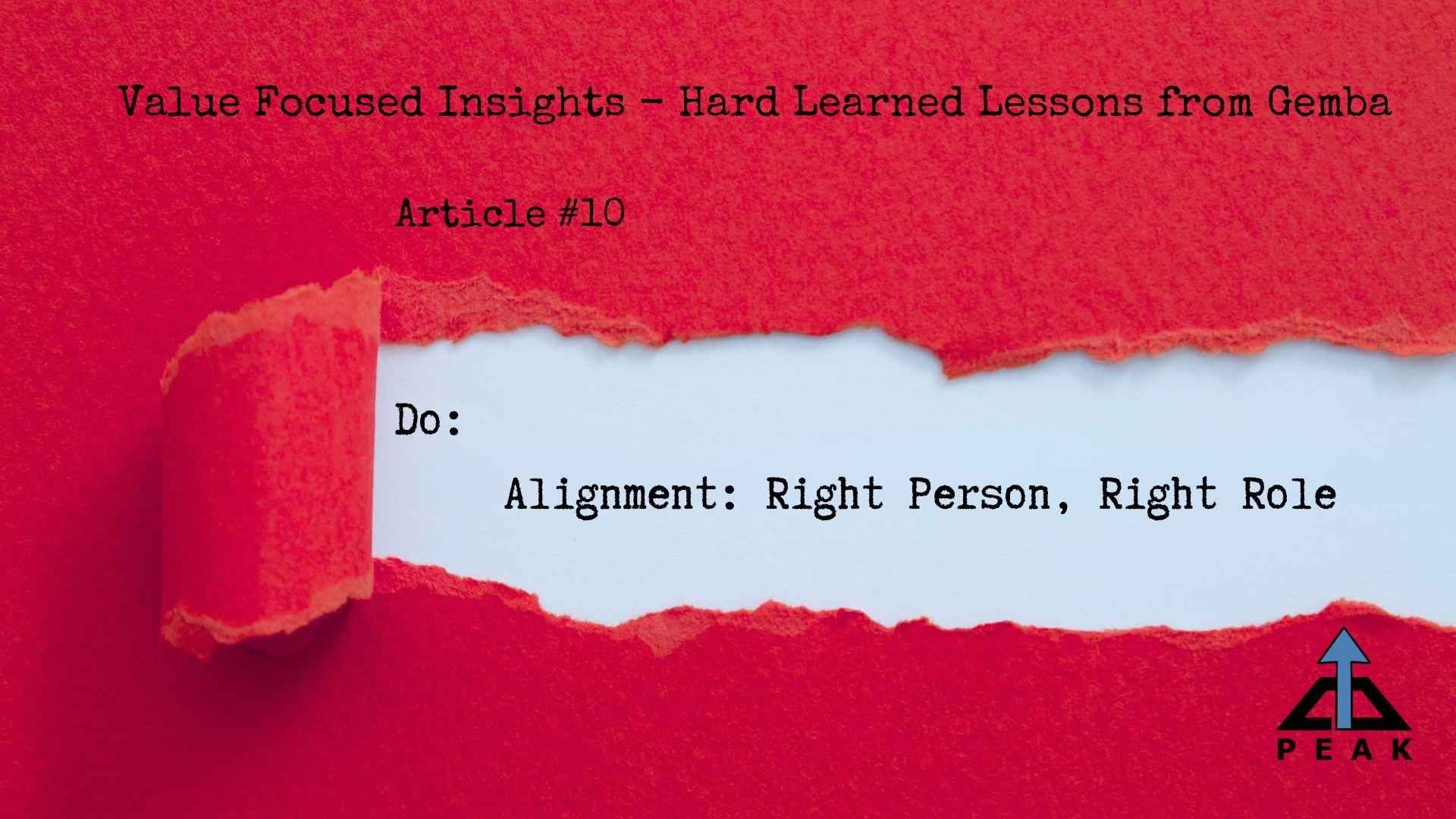
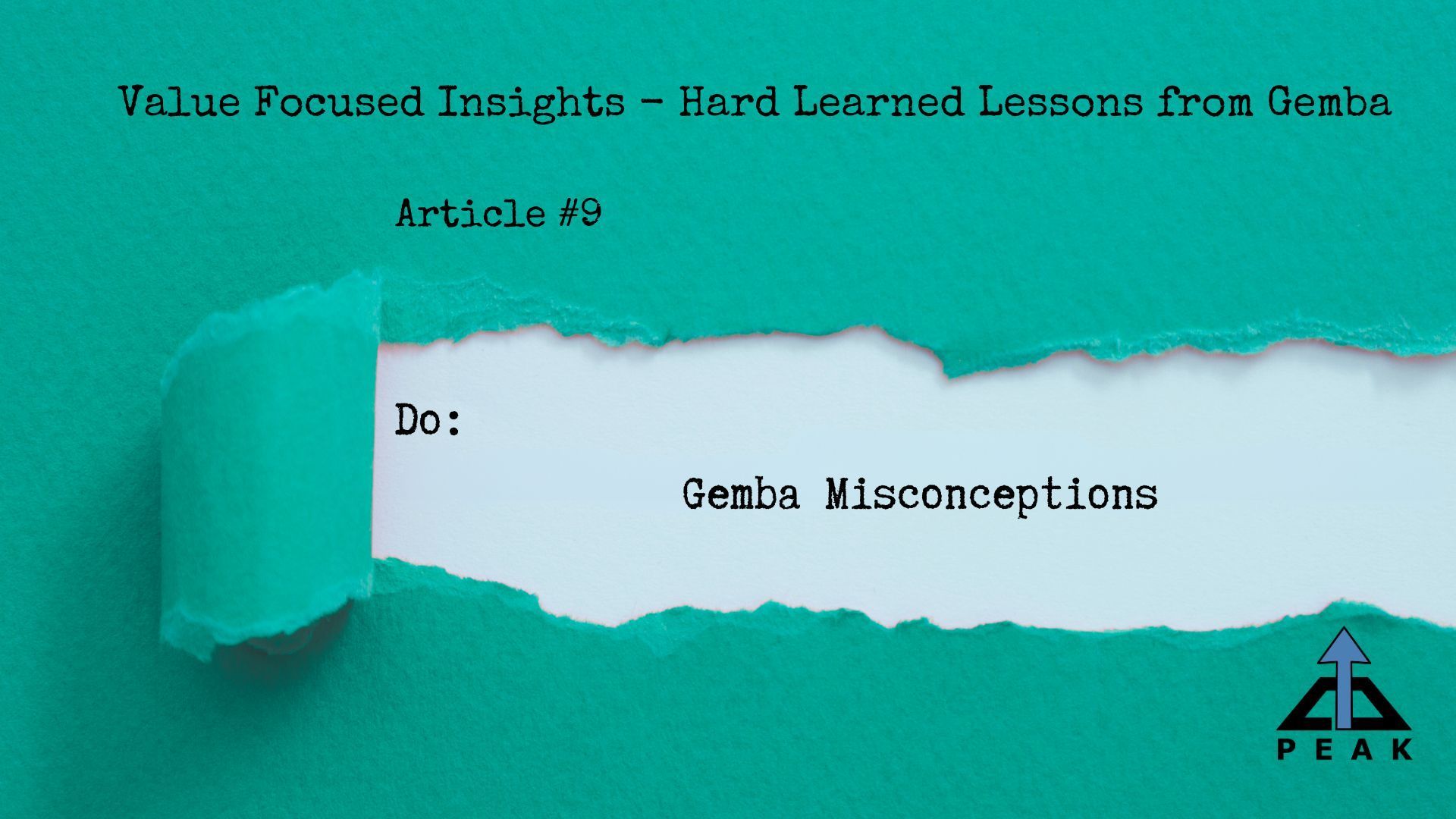
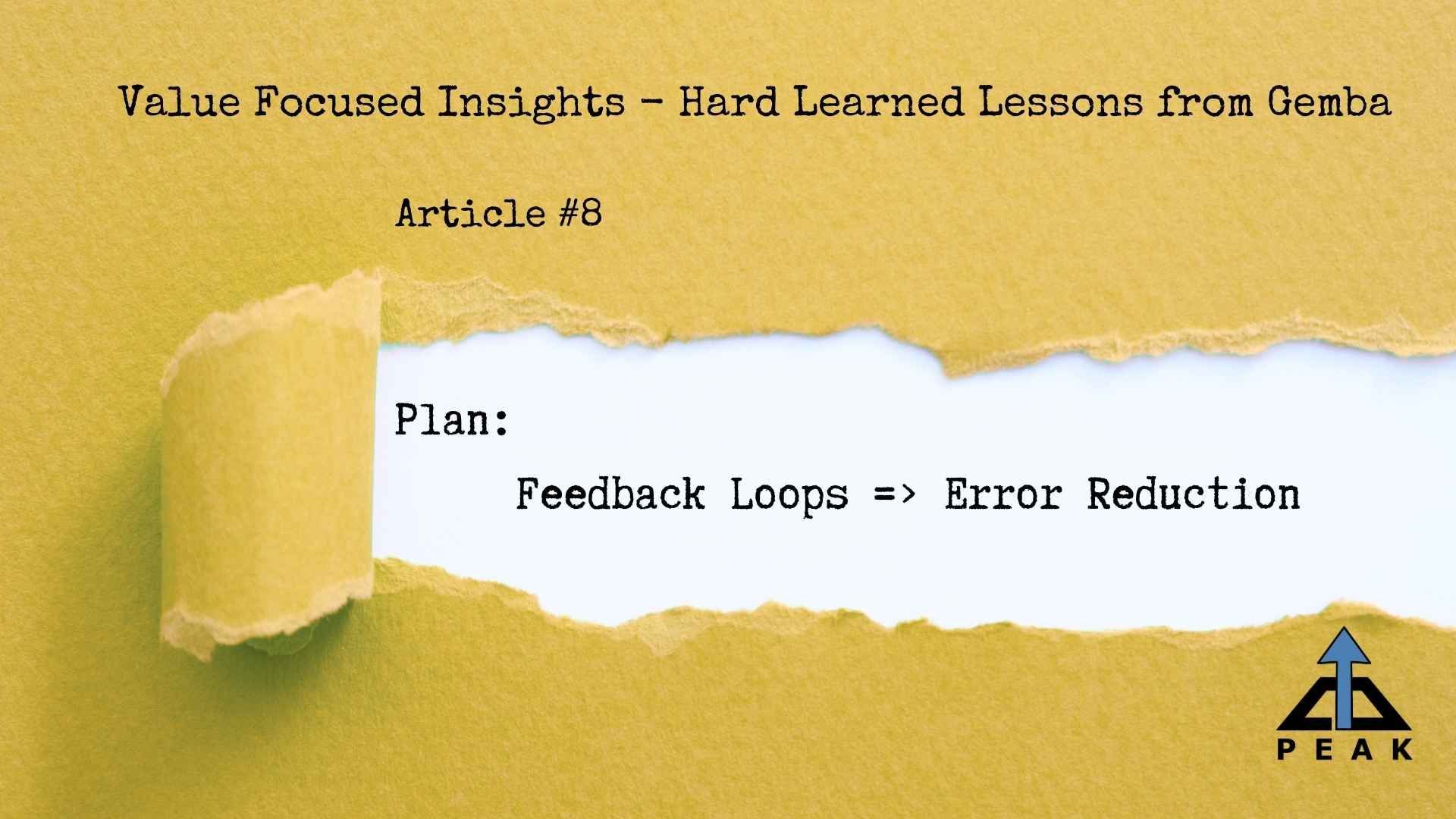
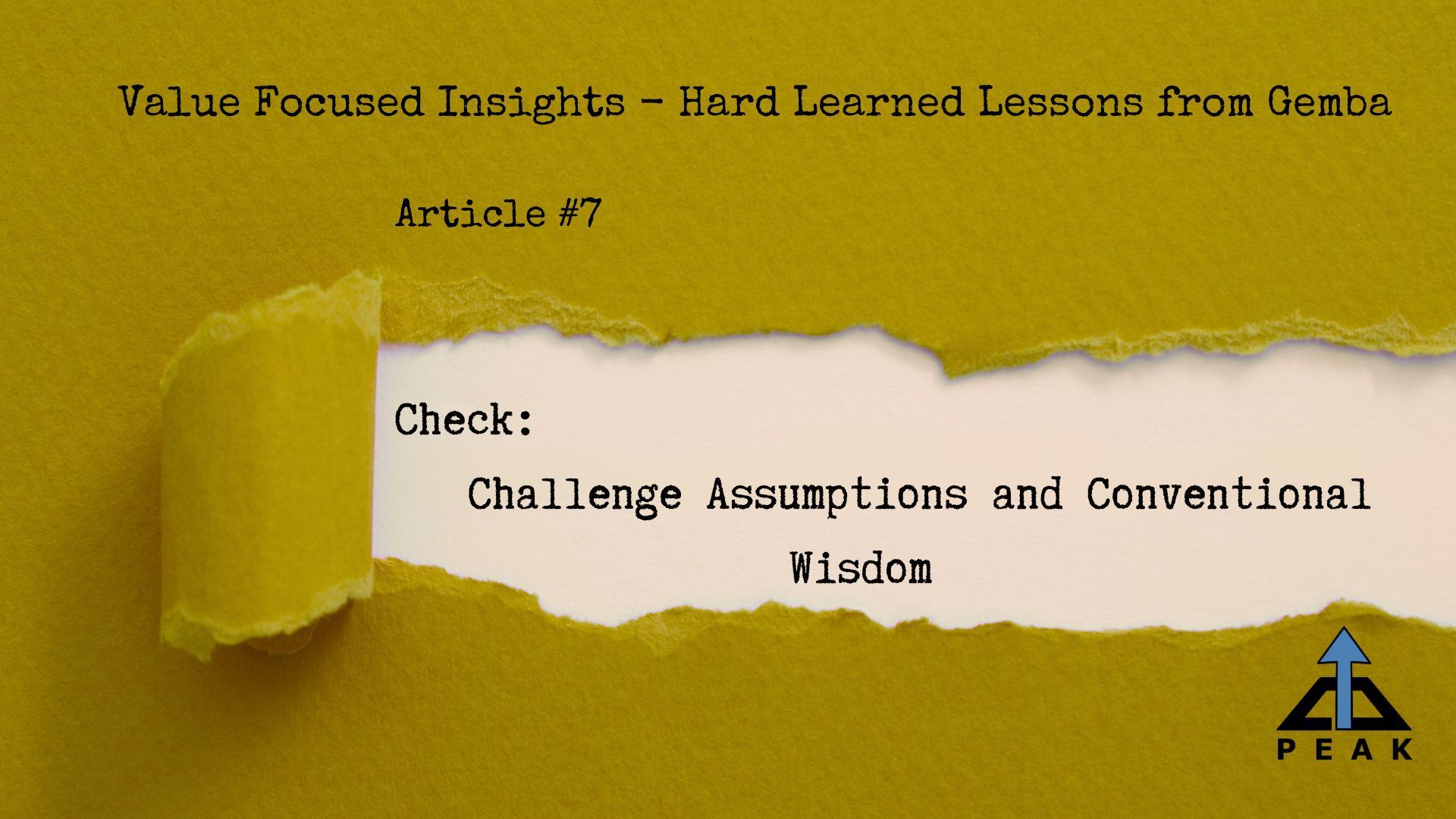
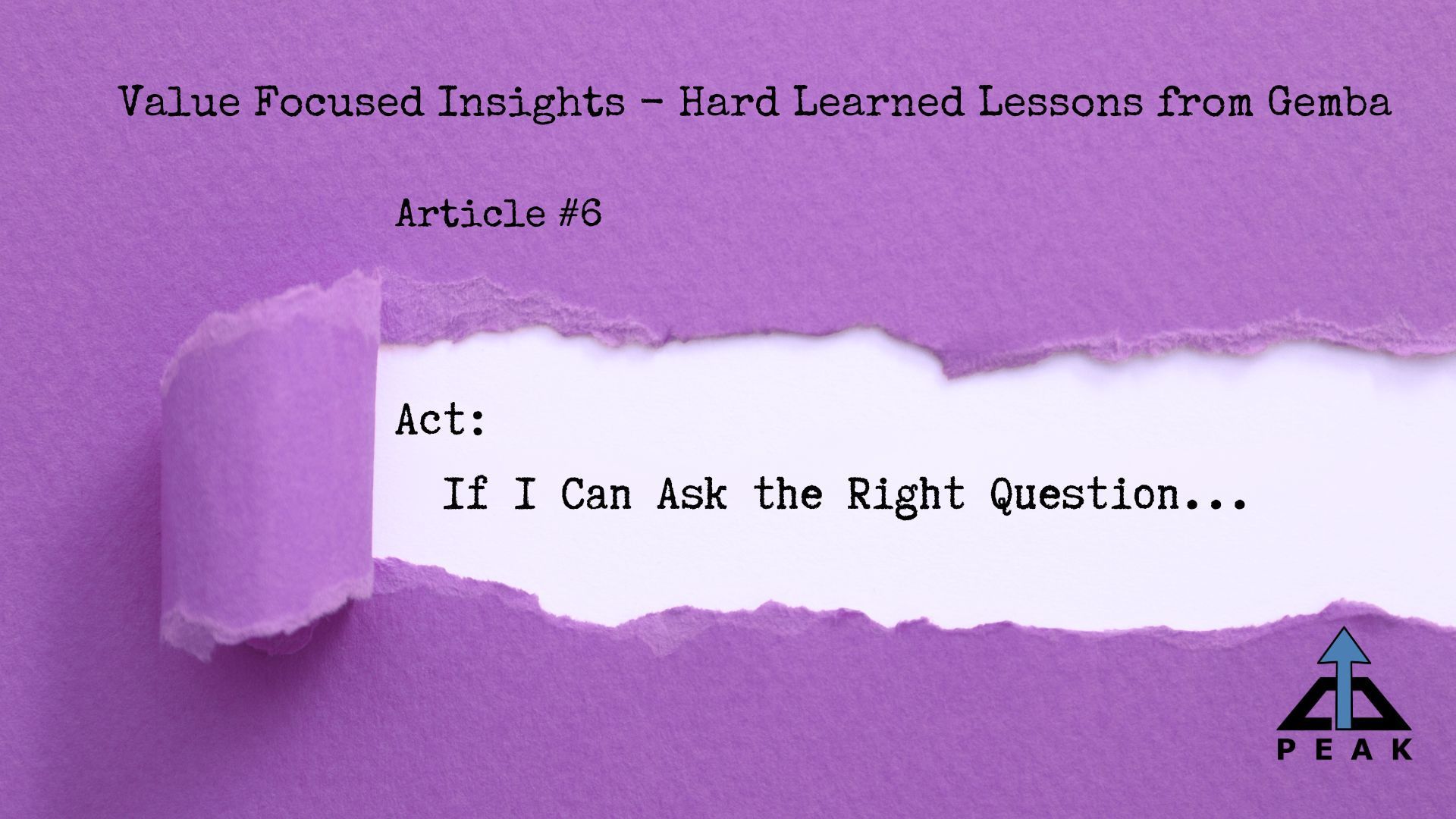
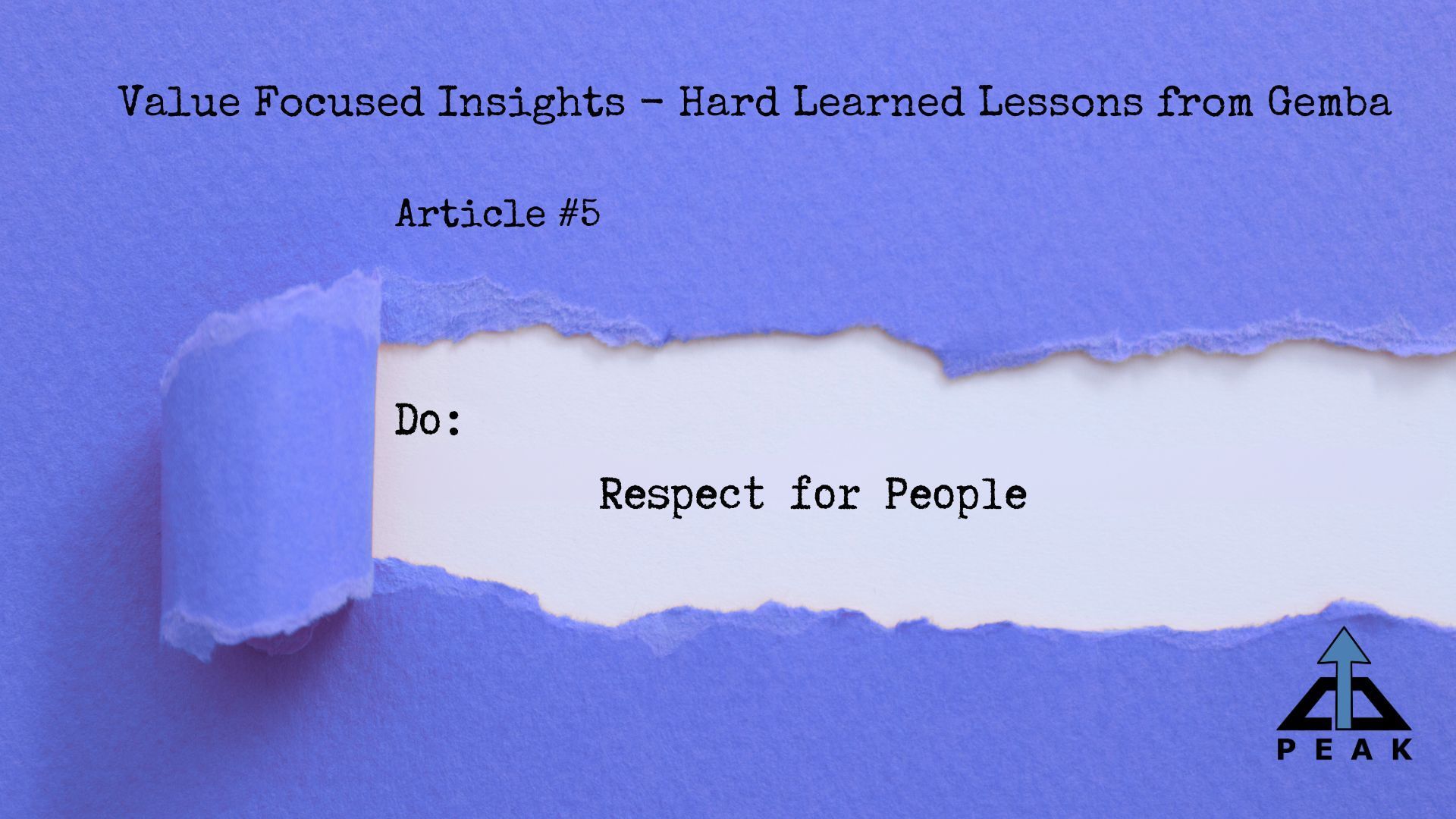
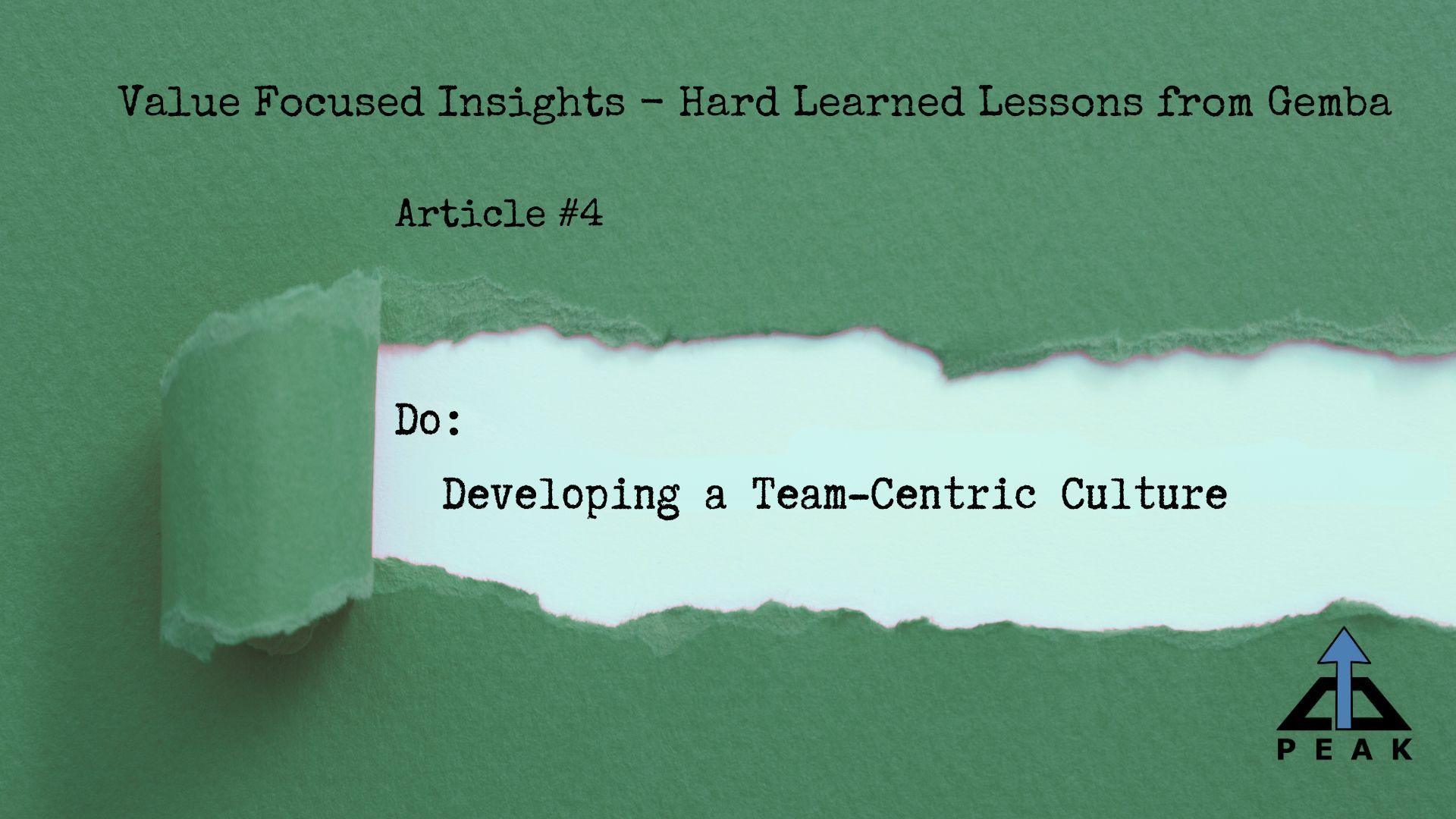
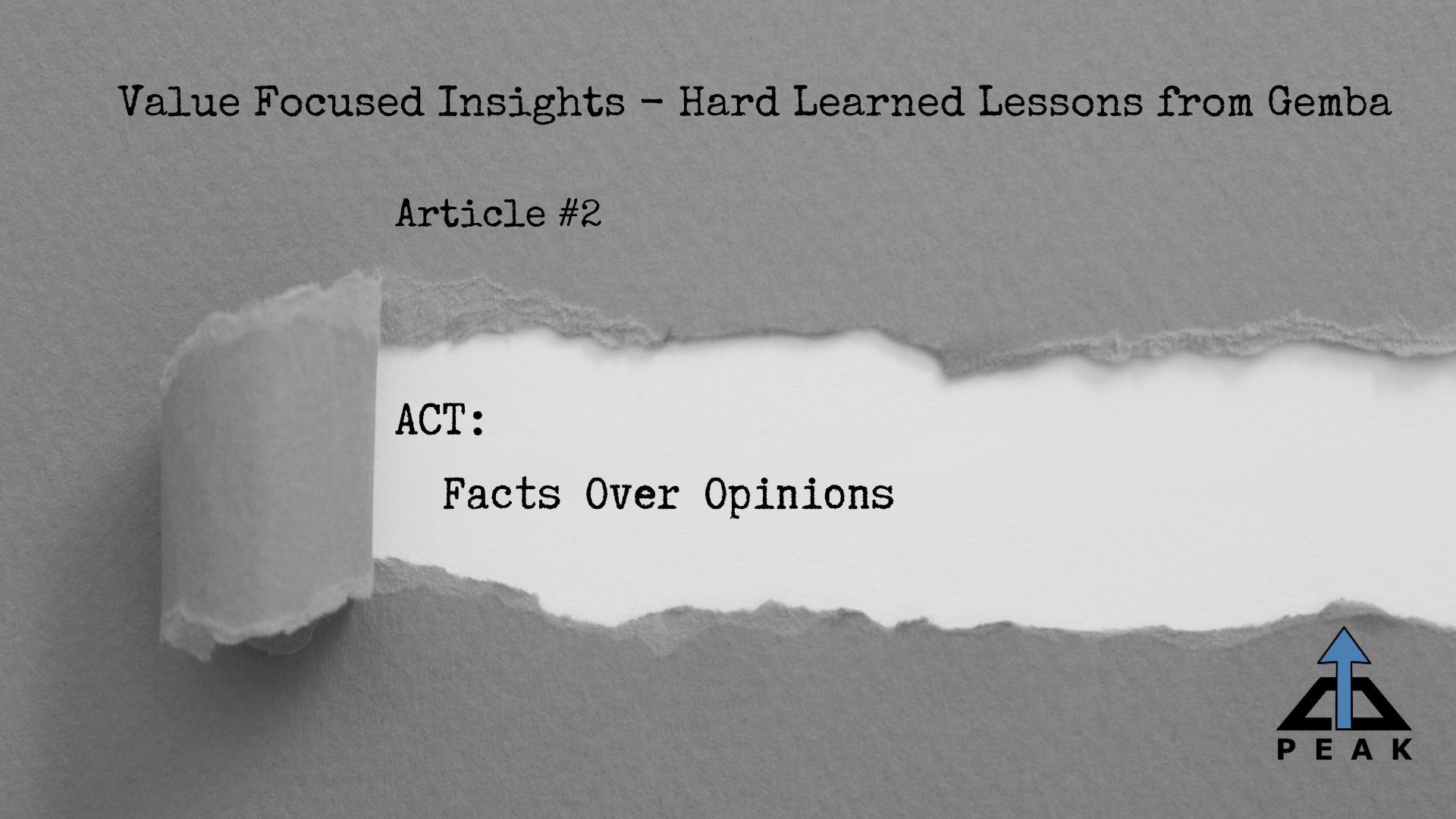
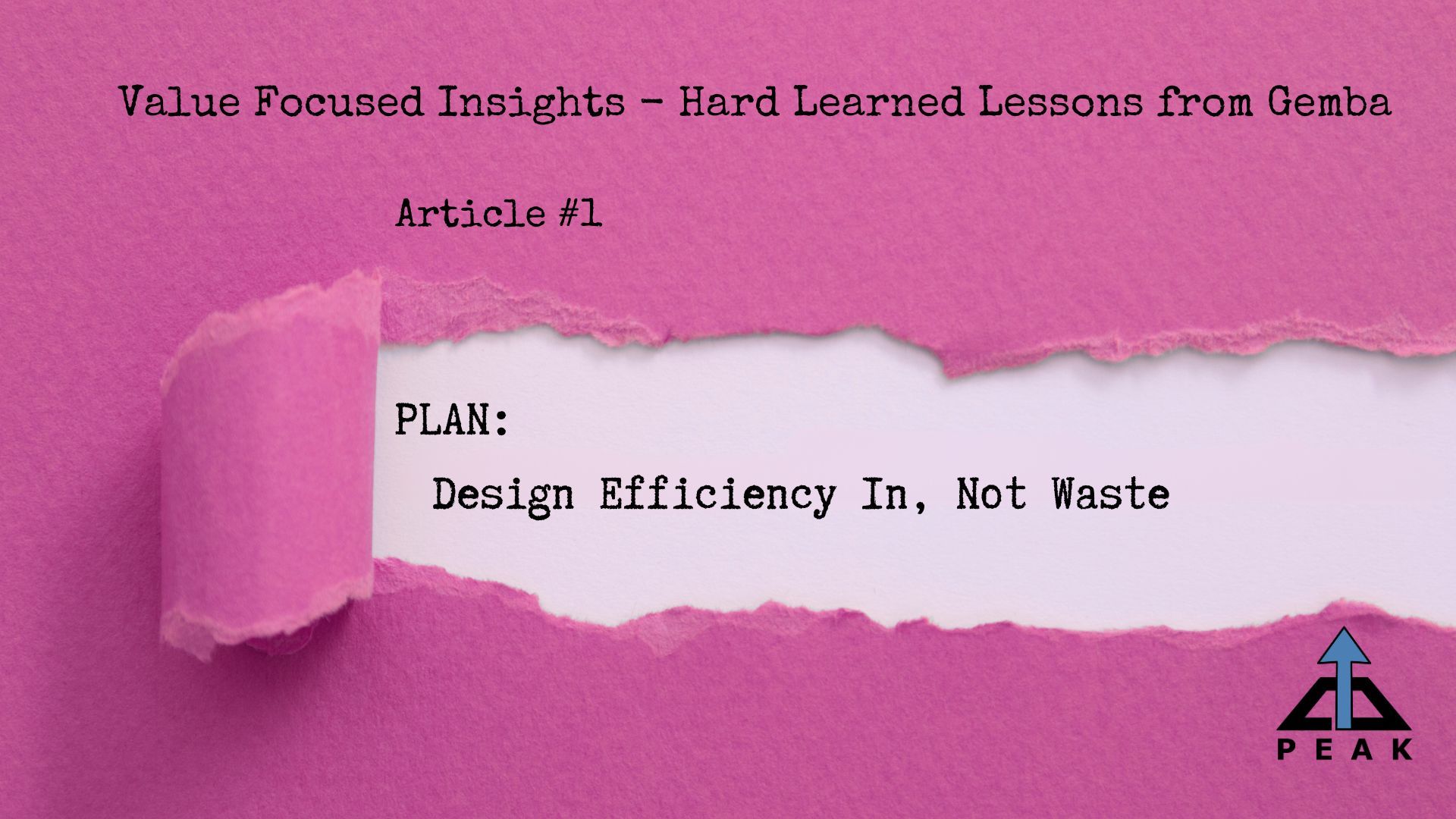
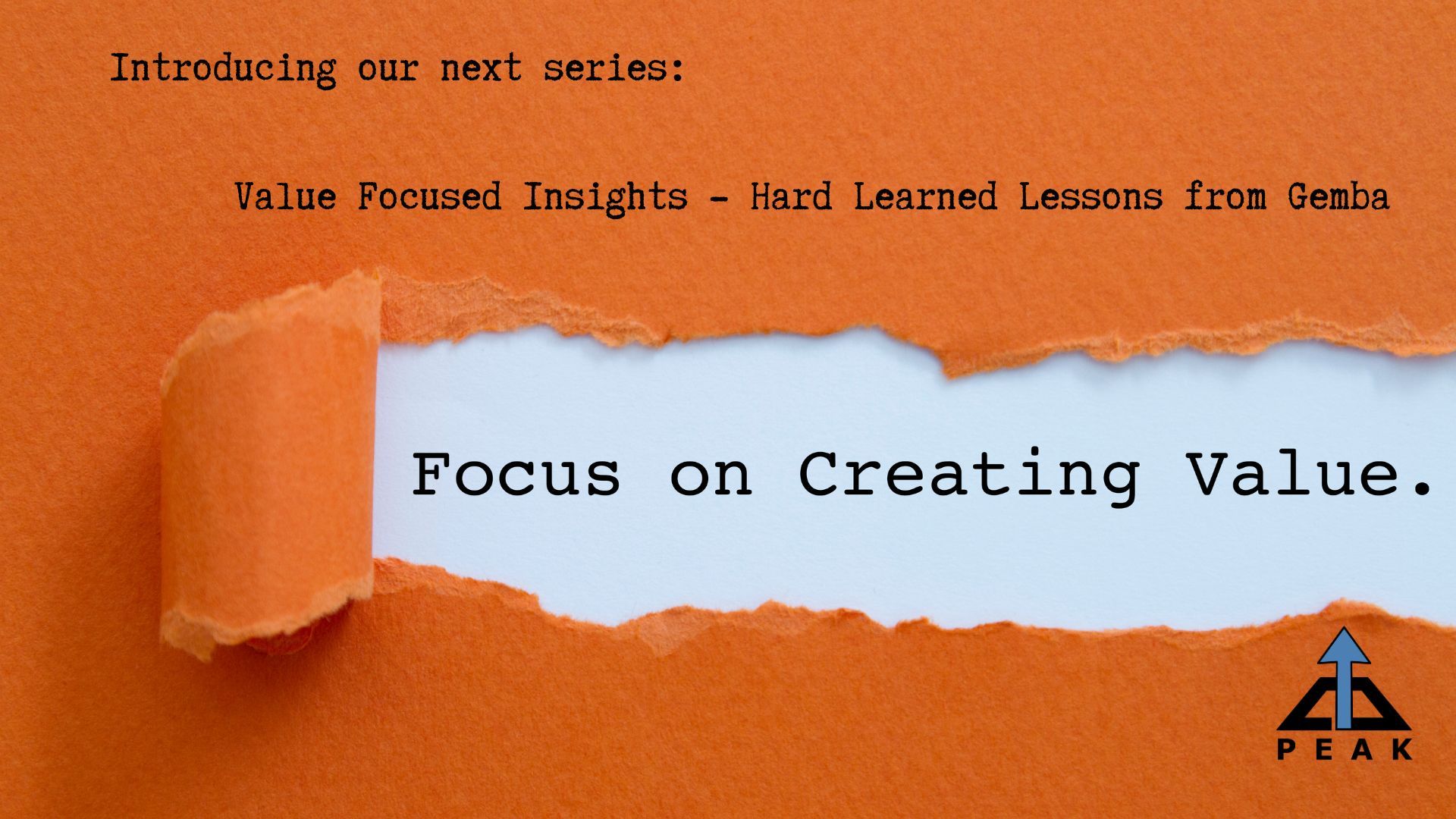