Embracing Slower Times - Part 11 Building Resiliency with Long-Term Sucess using Visual Controls
Annah Godwin
This is the 11th blog in a 13-part series titled “Embracing Slower Times, Building Resiliency for Long-Term Success using Visual Controls.” In it, I focus on the lean manufacturing tool, Visual Controls, and how they can be used to help build long-term success for your organization. Visual Controls are included in an organization's standardization toolset and are one of my favorites to deploy.
This is the 11th blog in a 13-part series titled “Embracing Slower Times, Building Resiliency for Long-Term Success using Visual Controls.” In it, I focus on the lean manufacturing tool, Visual Controls, and how they can be used to help build long-term success for your organization. Visual Controls are included in an organization's standardization toolset and are one of my favorites to deploy. As the name implies, they contain pictures, drawings, schematics, charts, checklists, etc., that can communicate operational status, instructions, feedback, safety needs, and much more. When deployed correctly they help you identify problems within processes that impact production, cost, lead times, inventory, safety, quality, and other key metrics.
What are Visual Controls? It is a set of lean tools that help team members and management understand the current condition by reviewing key inputs and outputs within a given process. They are highly visible and intuitive. Visual Control uses the standard to measure the status and highlight problem-solving opportunities, along with communicating important information personnel need in the area. They support Visual Management systems, which are key to moving to a more mature lean organization.
Let’s look at a couple of non-work examples. A lot of our day-to-day functions like driving or shopping would be less efficient and more hazardous without Visual Controls. Just think, when you approach an intersection, and the stoplight isn’t working, what happens? How do you approach the intersection? Most people become more cautious and aware of the other vehicles at the intersection. Of course, there are rules on what to do when the light is not working, but not everyone follows them. What about when a store redesigns its layout, moving products from one area to another? How quickly do you find the items you need? Do you have to ask someone for help? Are there signs that point you in the right direction? I am sure finding your way in those scenarios is much easier with visuals in place. A working stoplight or someone directing traffic at the intersection is safer and more efficient. Having a map and signs in the store helps you orient quickly. I think most of the time we are more aware when visuals are not present than when they are in our daily life activities. So why don’t we have that same level of Visual Control in our work environments?
In our work environments, most companies do a good job with safety-type visuals, like Personal Protective Equipment (PPE) signs for hearing or eye protection, or lights and alarms that indicate when something is not working properly on equipment. But don’t we need and want more information than that? Maybe it is time to start looking at Visual Controls as a cohesive system to improve standardization and communication, not just covering the basics. Don’t you want to have people walk into a company and know how things are going without the need to publish reports and attend management meetings? A company that is committed to a Visual Management system and supporting Visual Controls ensures you can understand how things are going without asking someone for the answer.
At a minimum, Visual Controls should provide immediate information on the current condition, highlight a problem, create a basis for improvement, and keep management alert to deviations from the standard.
- Help everyone understand the current condition and highlight problems in the area. The current condition includes output, safety, quality, staffing, inventory, and machine status. I remember one time I was touring a manufacturing plant and during the tour, we went to a small staging area that held inventory for a downstream process. The plant manager gave some basic information about the process and then asked if I thought they were having a good day or not. After looking at the visuals posted on the walls and the floor, I suggested they were behind by 2 hours. He smiled and nodded in agreement. He went on to explain that anytime he needed to know about current conditions, he didn’t ask his managers, he came to this small area and looked. When they were on schedule he would go back to his office, when they were behind, he would go to the upstream and downstream areas to see what the problem was. It became very apparent the efficiency gained for his entire team because of the robust visuals in place. Anyone who understood the visuals could determine the status and even potential root cause.
- Create a basis for improvement. Since Visual Controls are a type of standardization they should be reviewed, modified, and updated like standardized work. There must be an ever-present pull to make processes more efficient, less wasteful, faster, safer, and lower cost. Implementing key Visual Controls can help you achieve this goal.
- Indicate when a process has stopped following the standard. When the process is no longer performing at the standard, problems need to be solved to return back to the standard or to improve it.
There are many types of Visual Controls, and each one has a different purpose for application. How do you know which Visual Control to use within your process? Let’s review some of the more common ones.
Andon provides a signal indicating the status of a process or equipment. The andon can show when the status is or is not meeting the standard. For example, an alarm might sound when the line stops running, or a green light turns on when the line is running. Andons can be visual or auditory.
- Floor marking indicates where materials, supplies, inventory, or WIP are staged and should highlight the direction of material flow and the amount of materials needed. They can also be used to help maintain the flow of people and conveyance equipment (forklifts, AGVs, etc.)
- Color coding uses different colors or combinations of colors to indicate status or communicate vital information. In some cases, there are industry standards for color coding that should be applied.
- Safety signs communicate safety information, status, or standards. Many of the safety signs are standardized and should be applied accordingly. For example, stop signs are octagon-shaped with red and white coloring.
- Kamishbai board incorporates the use of a board that holds tee cards. Each card is associated with an action, task, or audit. The color of the tee card or the position of the card will indicate if the item is completed or still pending.
- Checklists standardize an audit of a process, task, or product. They are usually self-administered and typically highlight when steps or tasks are omitted or incomplete, or when products are not up to standard.
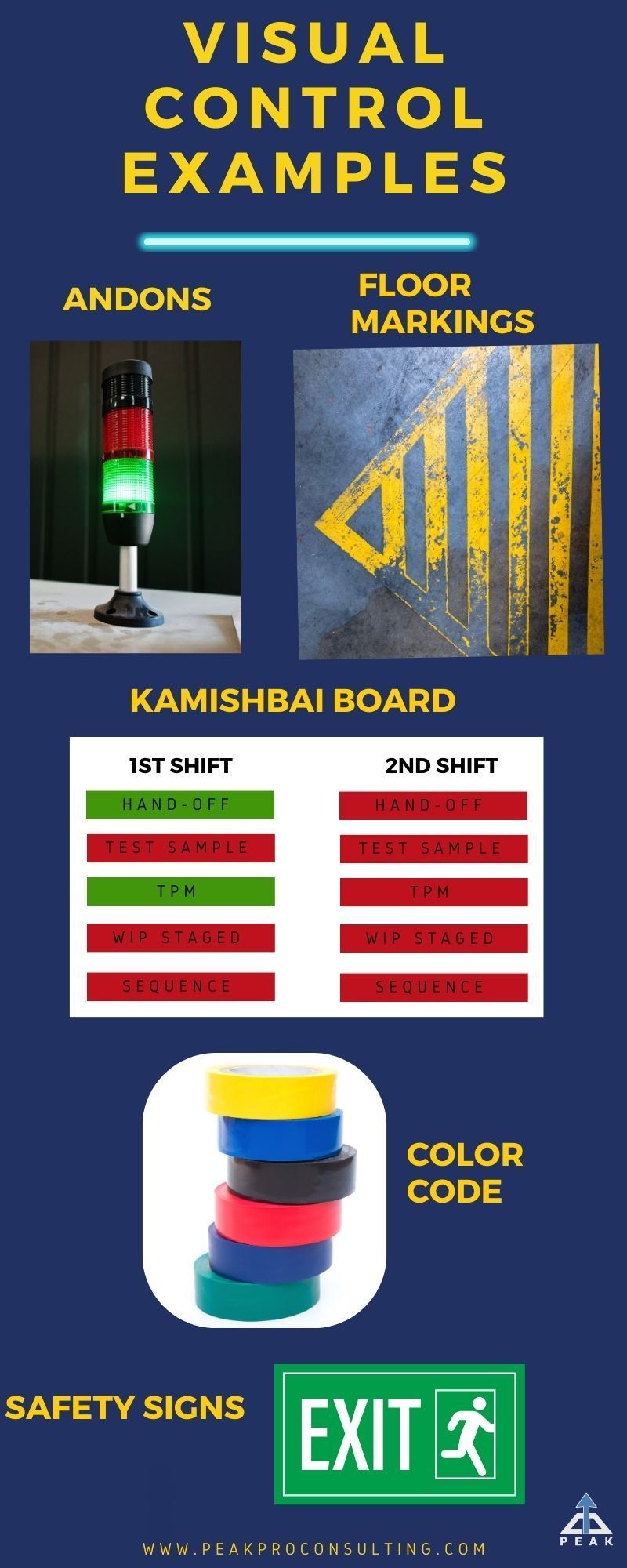
One of the things that I like about Visual Controls is they are usually simple to create and install. Also, they usually don’t require a lot of training for team members; a quick review will usually suffice. Their purpose needs to be clear by answering:
- What are they communicating and to whom?
- What actions are needed to correct issues or problems highlighted by Visual Controls?
They become even more impactful when they are incorporated with other lean tools like inventory management, TPM, standardized work, 5S, etc.
The reason to build your Visual Management System using Visual Controls when things are slow is because you have resources available to work on them. However, one universal challenge is the funding needed to create and install them. To determine how much time and money is needed, head out to the Gemba and review the visuals currently in place.
- Are they up to date?
- Do they meet the standards in size, color, font type, etc.?
- Is the information clear and concise?
- Are they damaged, dirty, or worn?
- Do they provide the desired results?
These questions will determine the scope of work and resources needed. Usually, it is not people-intensive, but it does require knowledge of Visual Controls and how to implement them, computer knowledge and access to design them, and a printer capable of making them. Much of the cost, beyond the allocation of resources, results from the ability or decision to print them in-house or to have them supplied by a vendor. It is important to standardize their look, so consider fonts, colors, sign size, medium, mounting types, etc. My recommendation to reduce costs from rework is to create mock-ups internally, verify their correctness, and then, if necessary, send them to a vendor to be produced.
Because companies often have a basic level of Visual Controls in place, they tend to believe the task of generating Visual Controls is complete. However, because they are part of process controls and standardization they should be looked at as vital and necessary to maintain a smooth and efficient operation. Don’t make the mistake of placing them in the “do it later” category. Instead, get your team involved in building a Visual Management system that is alive and robust. Since slower times mean there is the potential for resources to be reallocated, I feel that's a perfect time to go to Gemba, design, and deploy them. You will find when the demand returns your new Visual Controls will allow you to quickly access your status, identify the problem, troubleshoot it, and get back to the standard. In many cases, all this can be completed at the Gemba without the need for meetings to fit the issue.
Hopefully, this blog provided some insight into the benefits and types of Visual Controls. If you've liked it, let us know in the comments. If you have questions, post those in the comments as well. Also, if you miss any of the other blogs in this series, you can find them on the Peak Productivity website or our linked-in page.
Peaks and Valleys.....
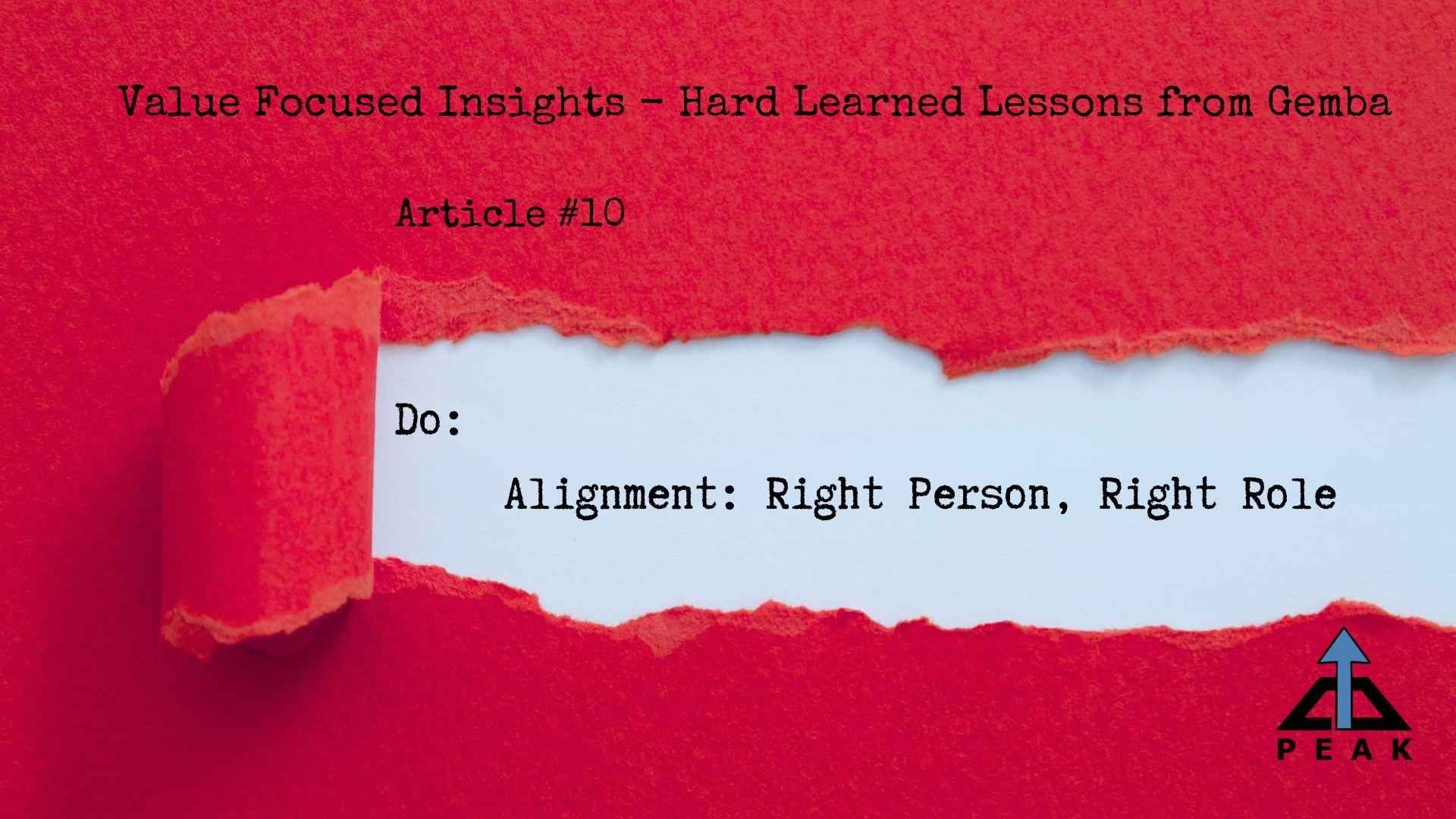
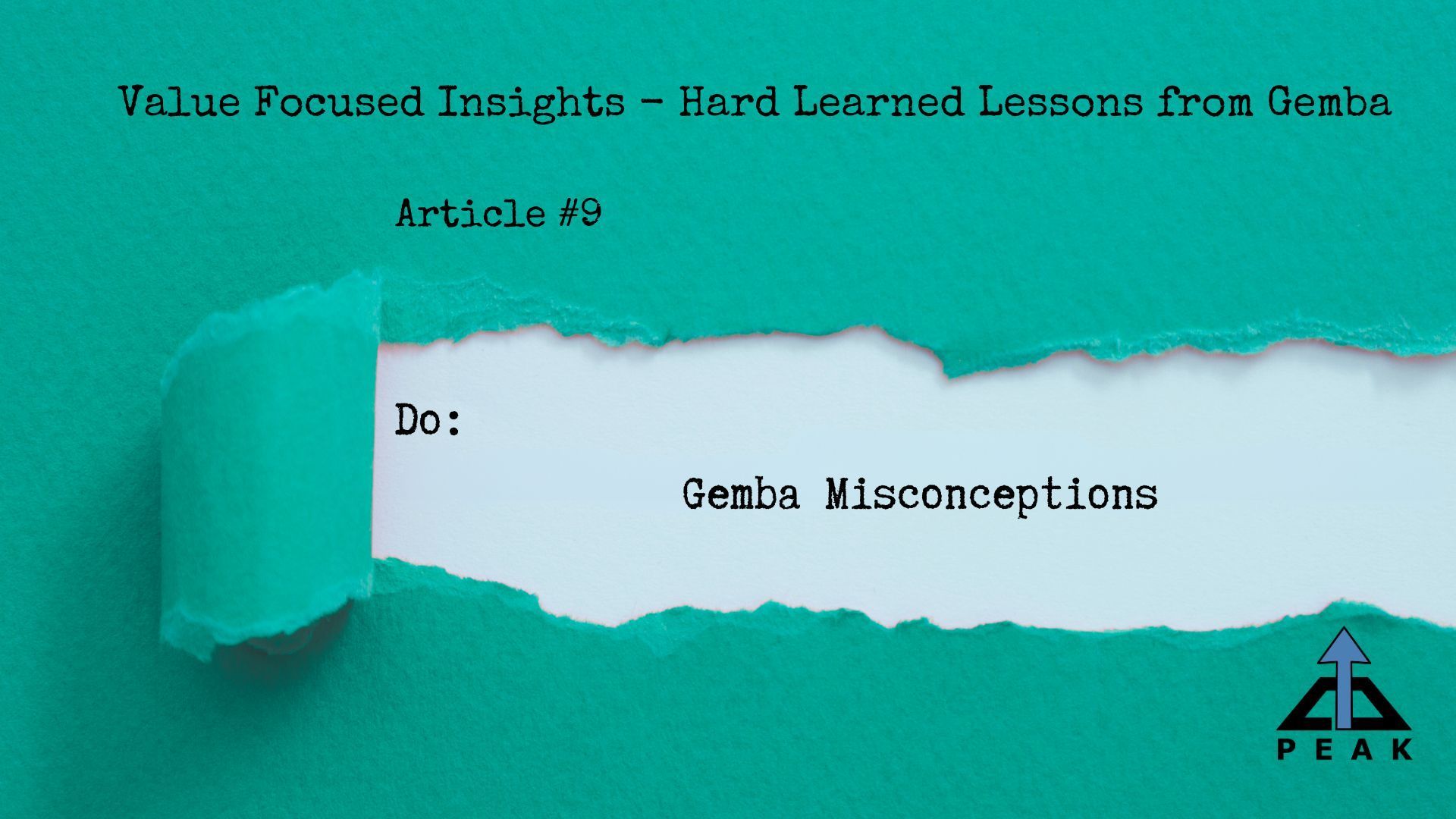
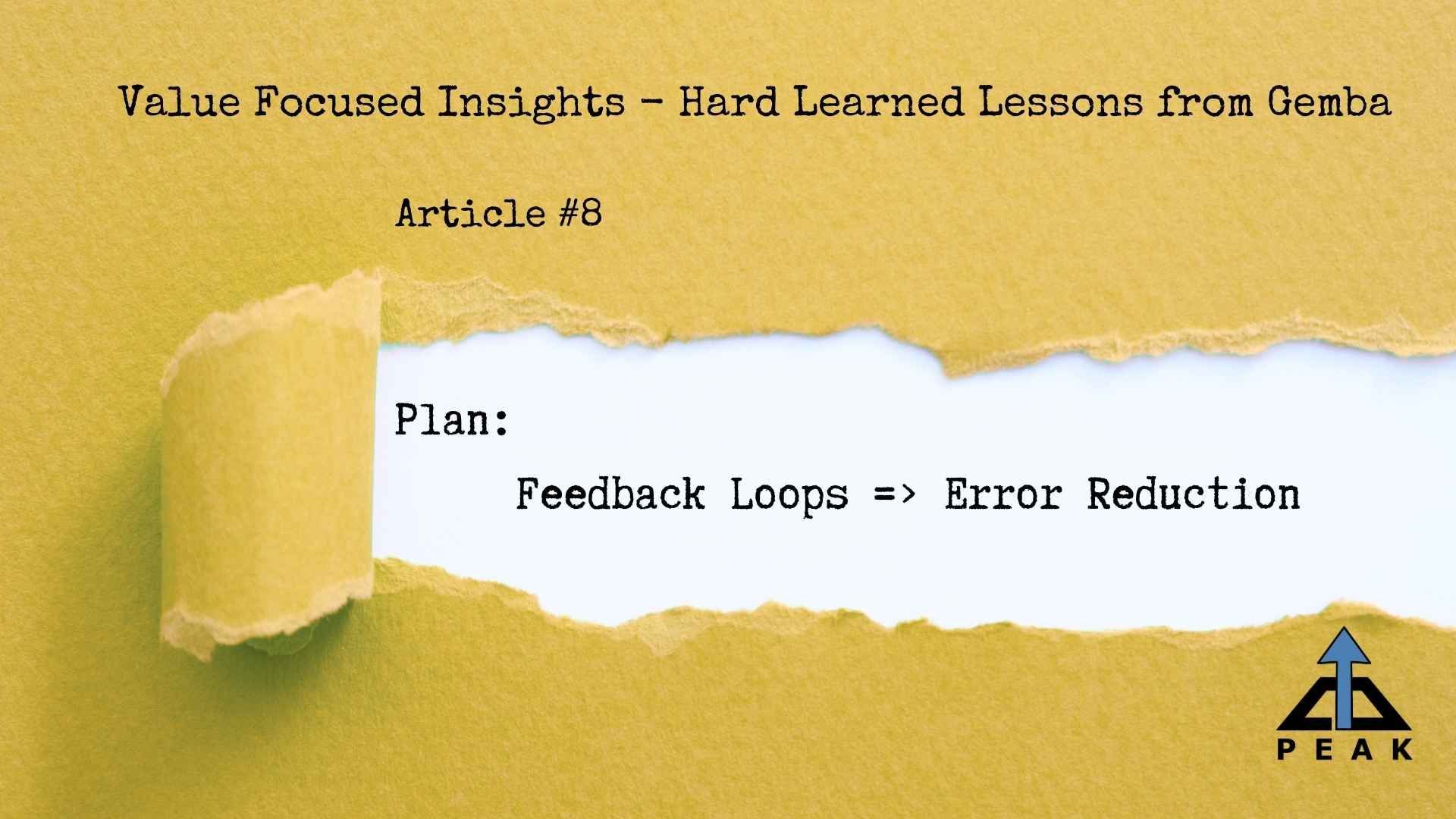
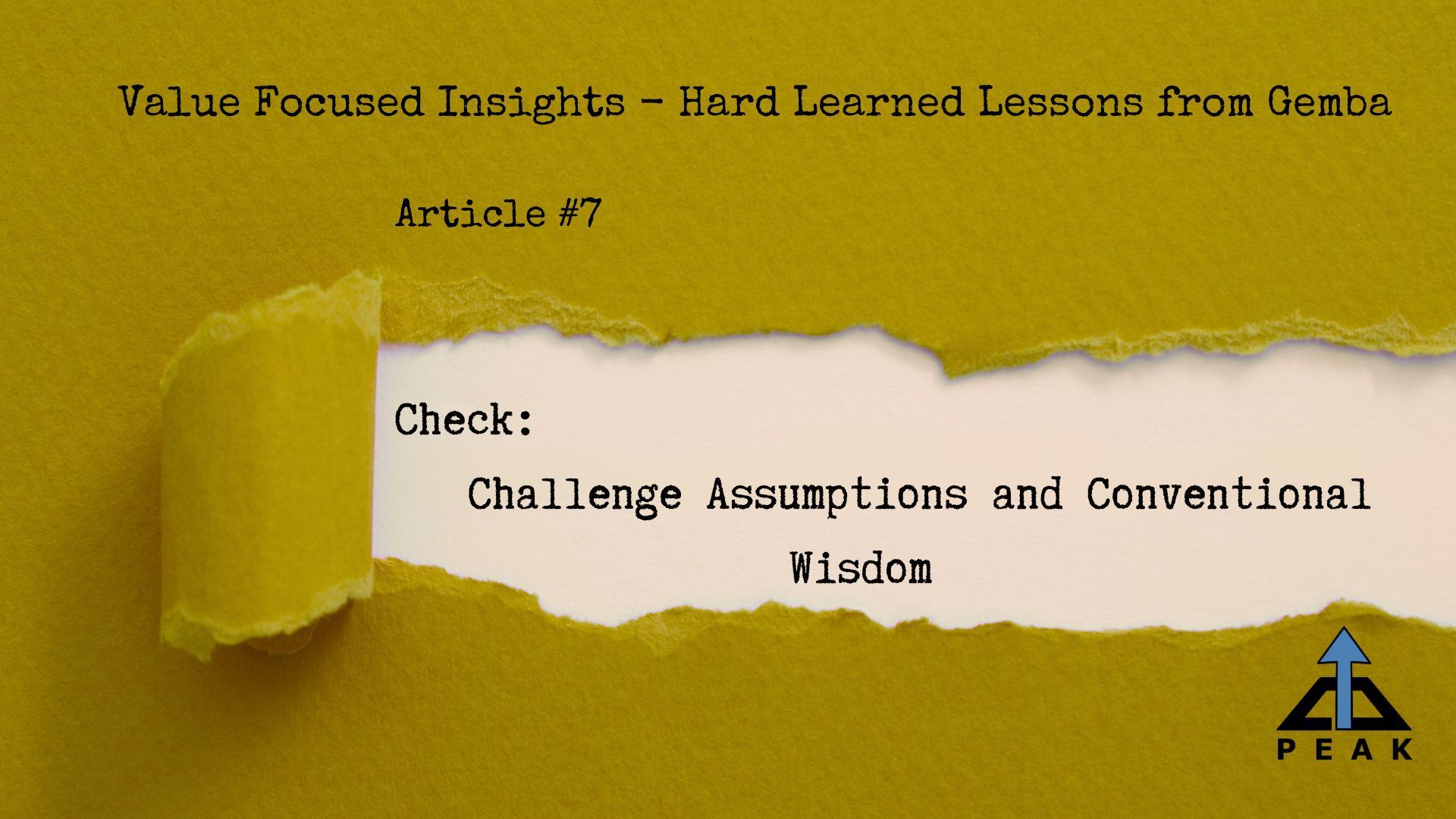
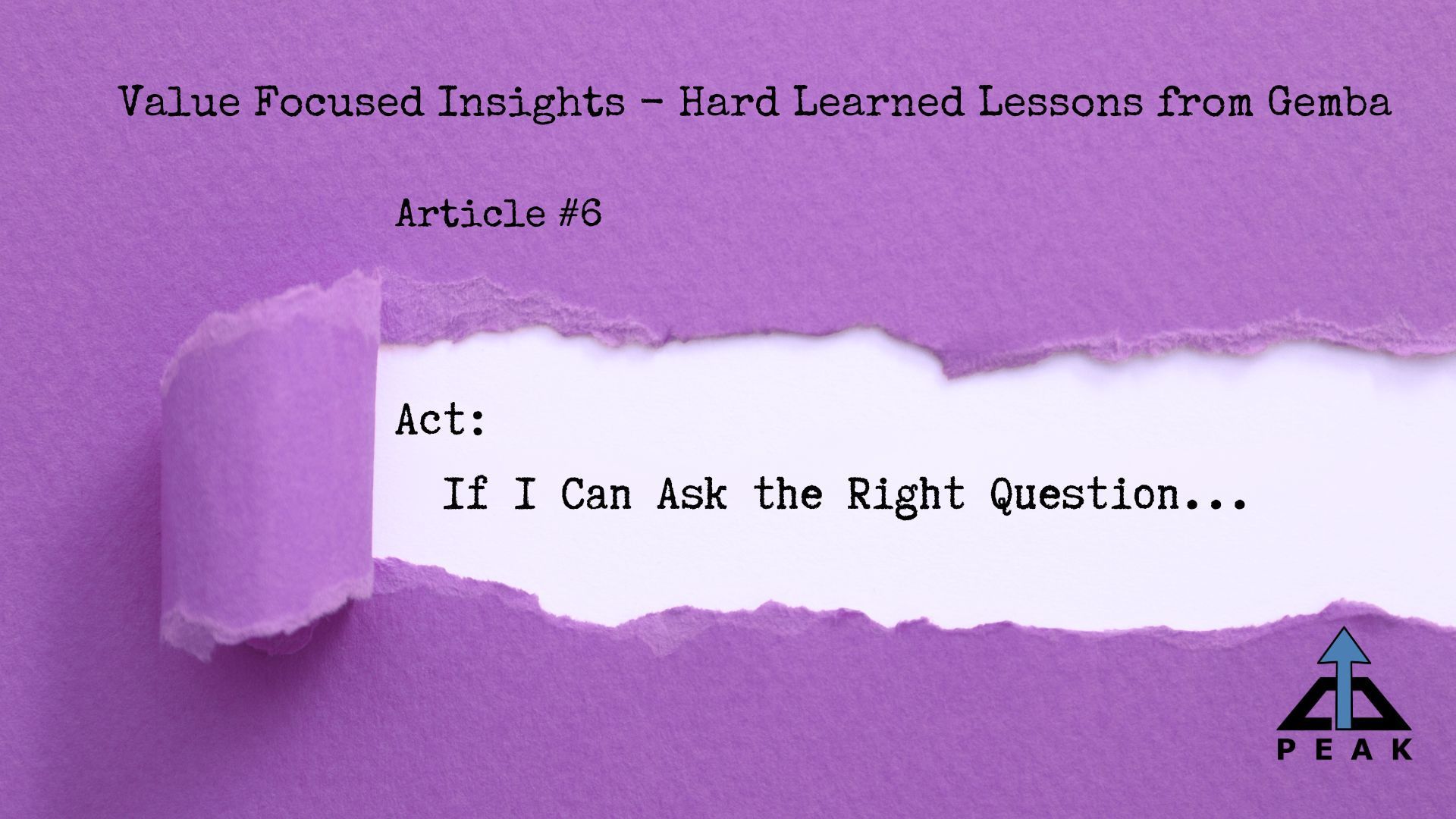
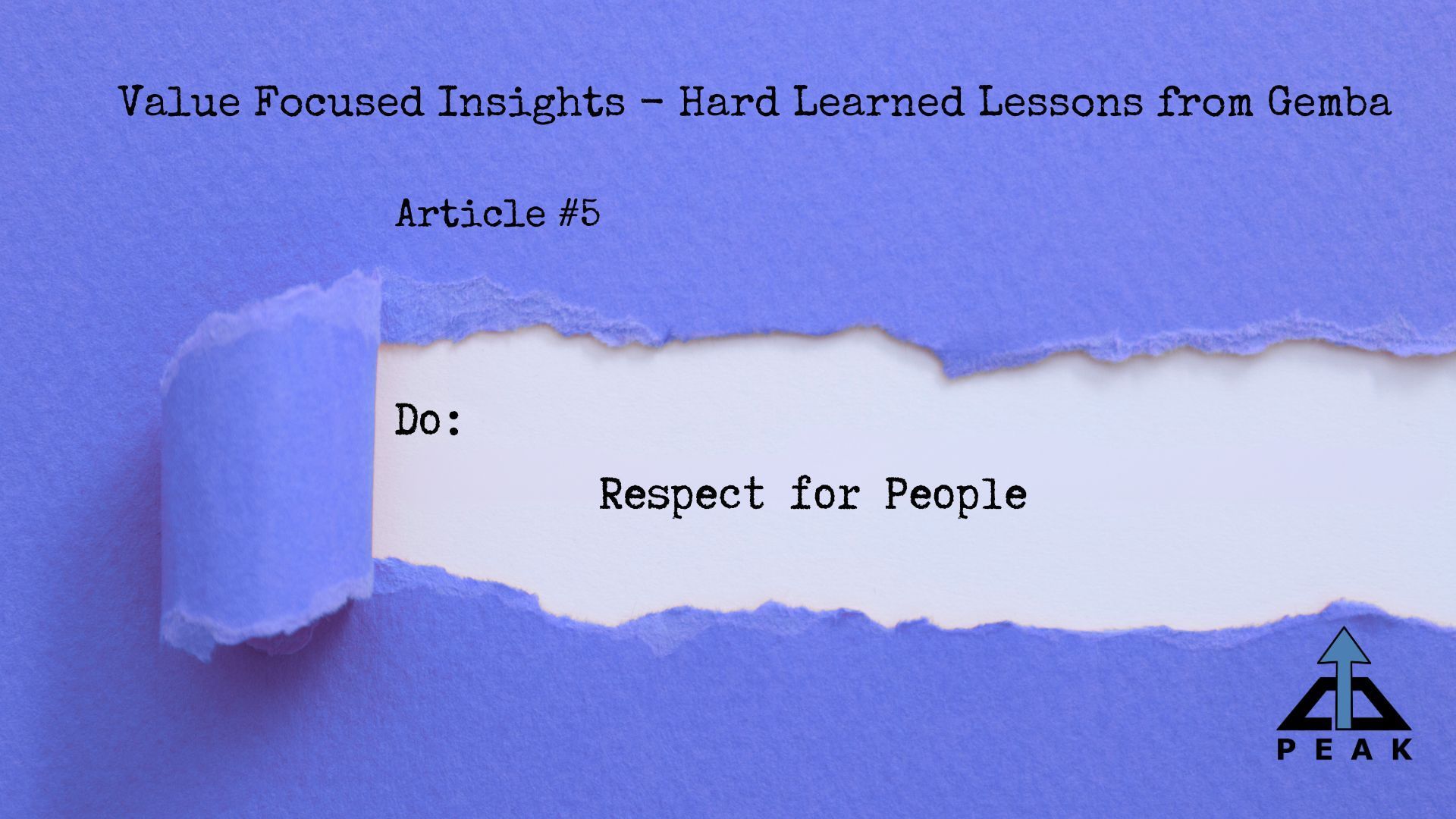
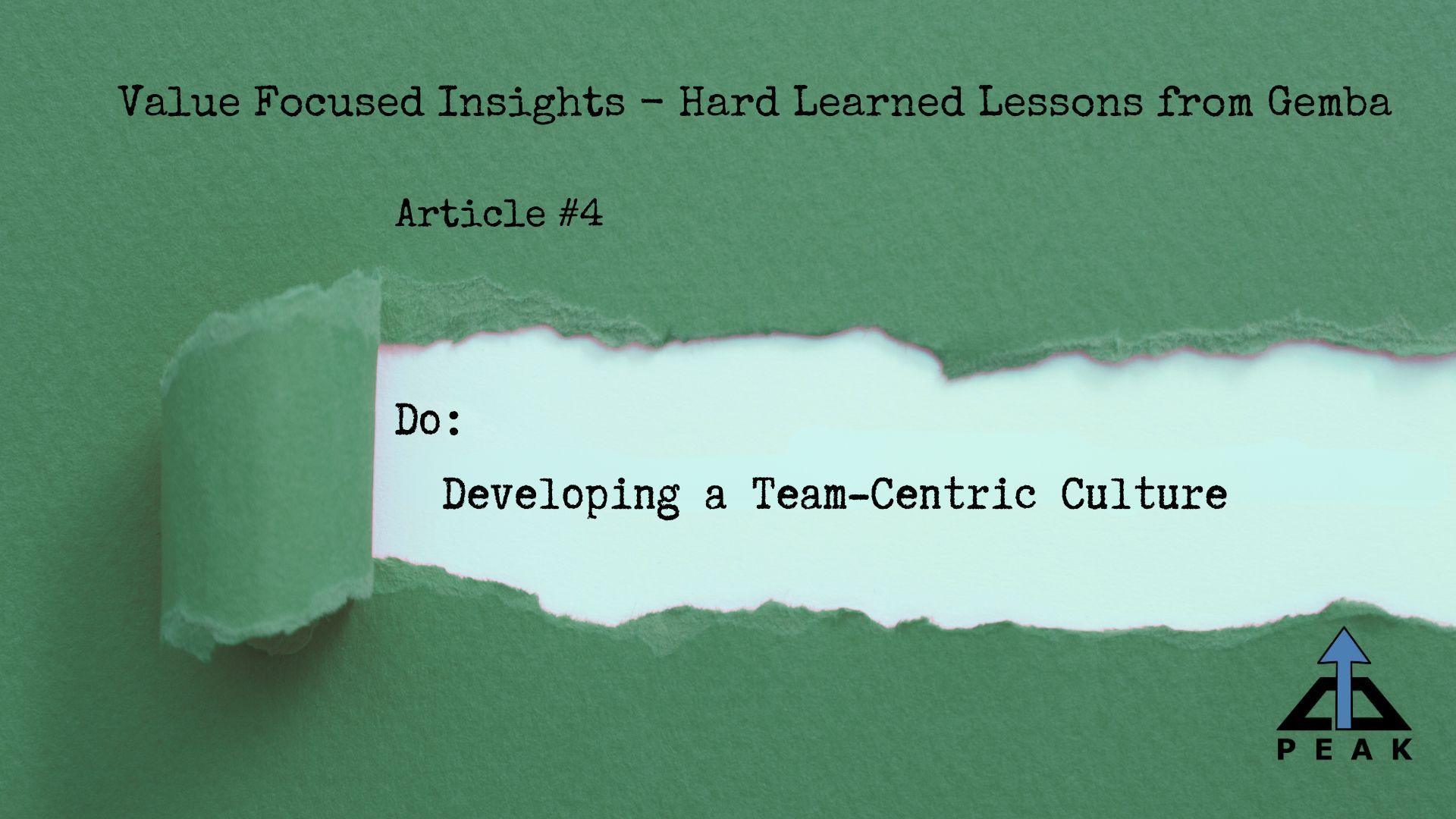
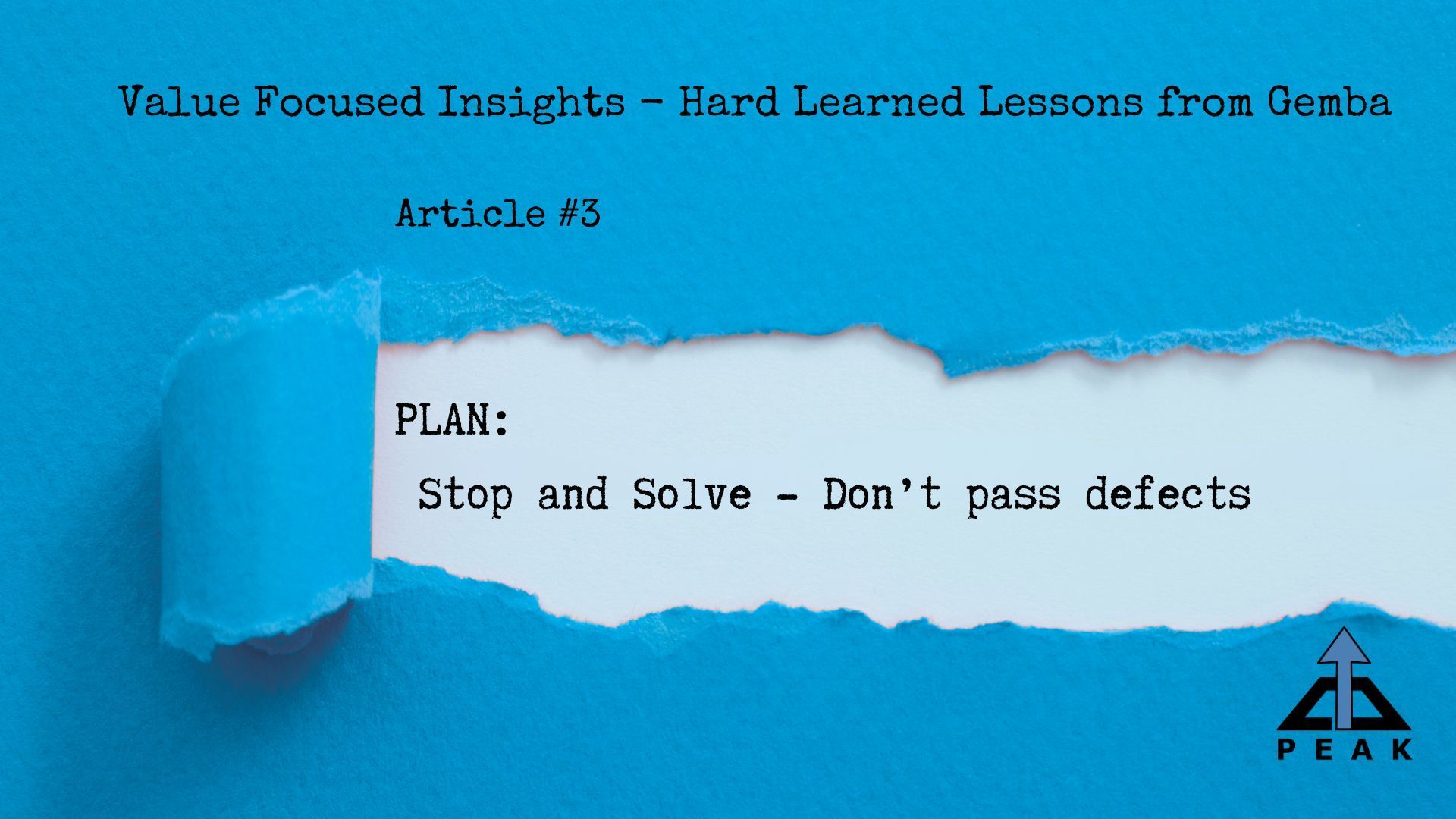
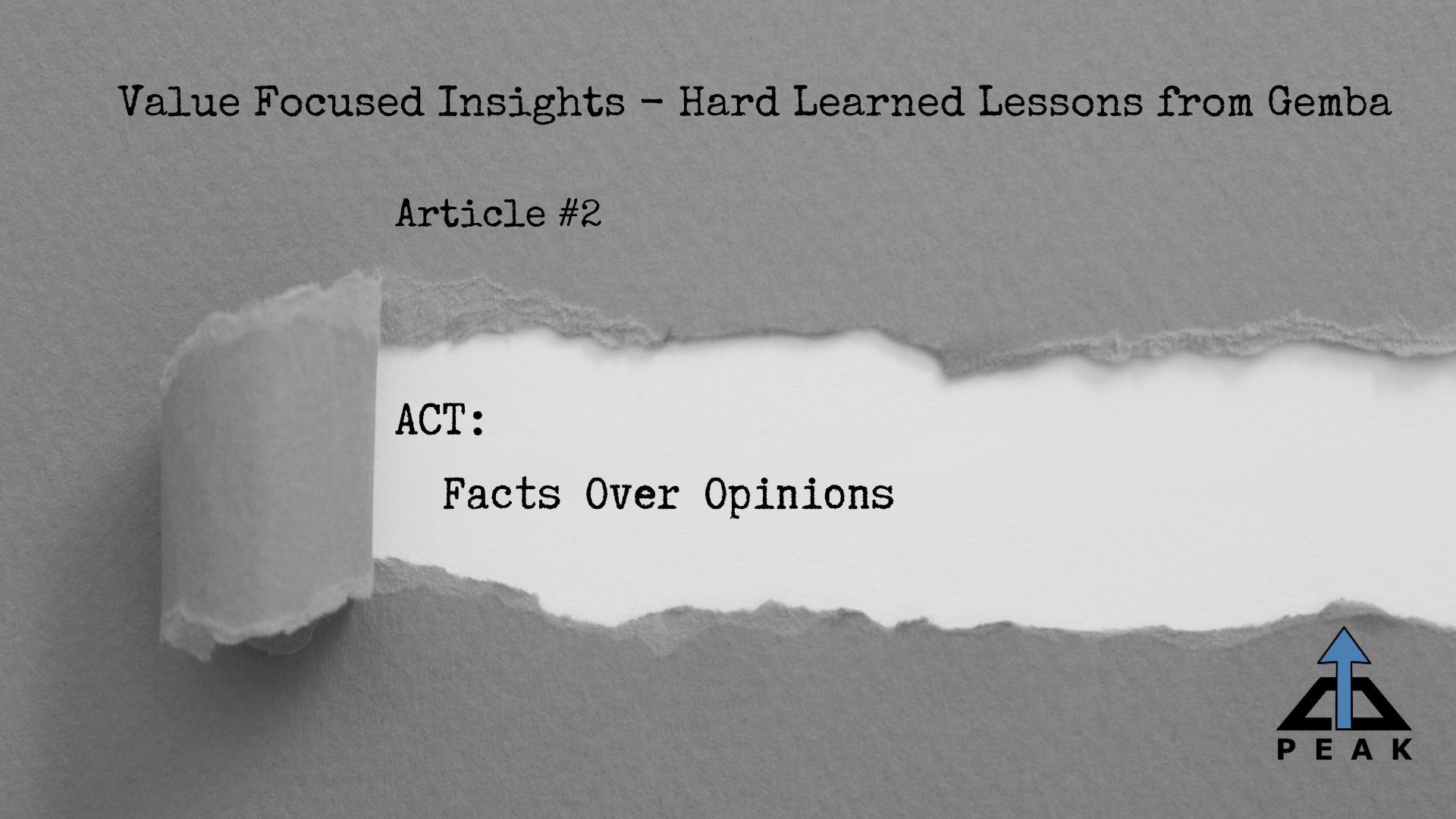
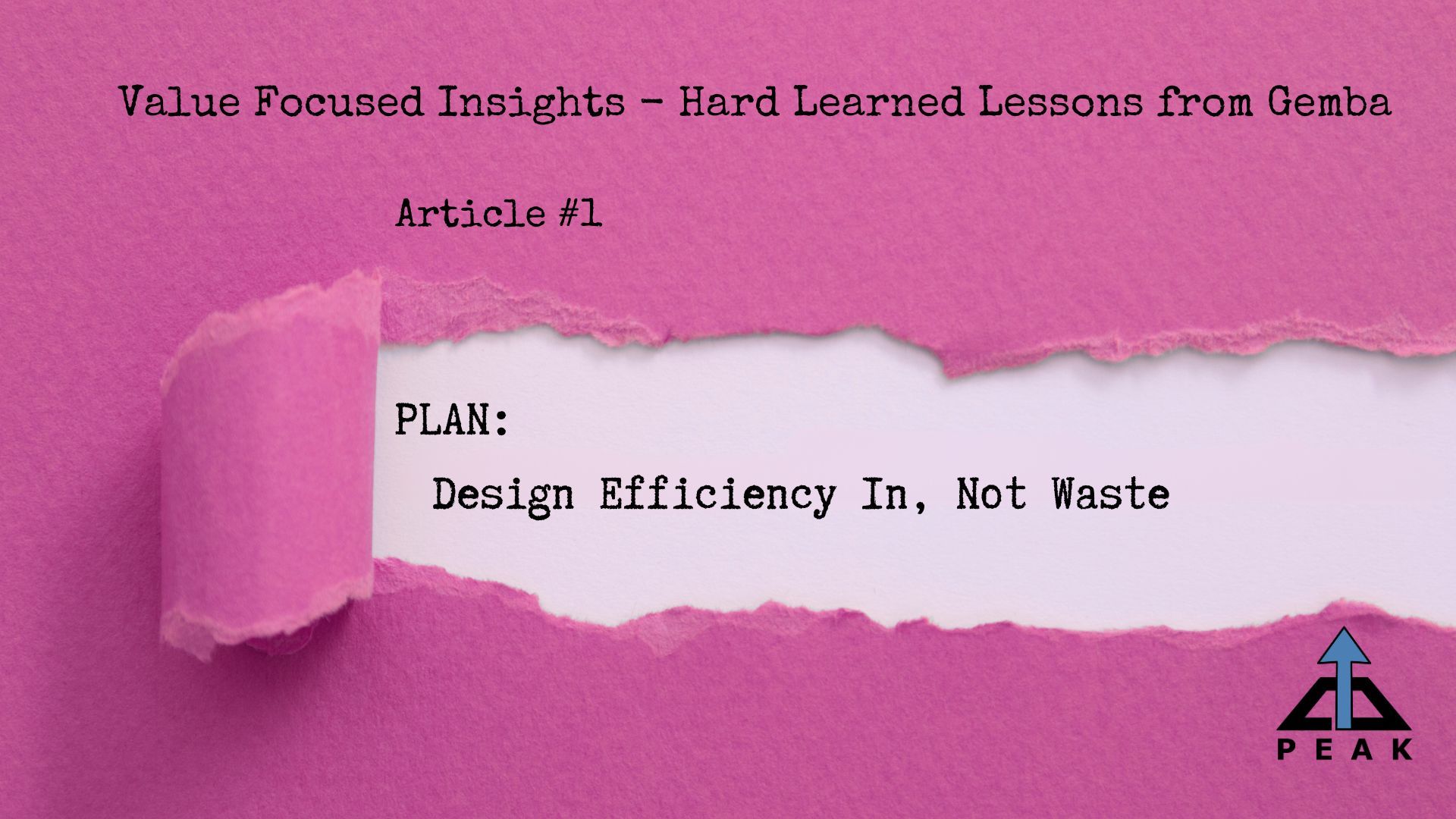