Embracing Slower Times - Part 12: Rebuilding Quality Tools and Standards
Tim Upchurch
Welcome to the next installment of our series on building resilience during periods of lower demand. In this article I will discuss options to either rebuild or introduce quality tools into your processes. Unfortunately, most quality tools are often introduced and then never seriously reviewed or challenged again. Any slowdown in production is a great time to check up on your quality systems and determine if you need to revise or upgrade them for when volume returns. This can range from a quick check to verify everything is still working as planned or may even require a total rebuild of the systems. Regardless of your current condition, you need solid quality systems in place to support stable processes. They constitute the foundation for continuous improvement in all organizations.
I will explore both traditional and innovative strategies such as quality circles, visual tools, real-time feedback loops, preventative measures, and visual controls. I hope to challenge some of your established assumptions, encouraging you to rethink and rebuild your approach to quality in ways that promote lasting resilience and success. If you're ready to strengthen your quality systems, join me in this latest edition.
For previous articles in the series, please visit our company website or LinkedIn page. As always, we’d love to hear your feedback.
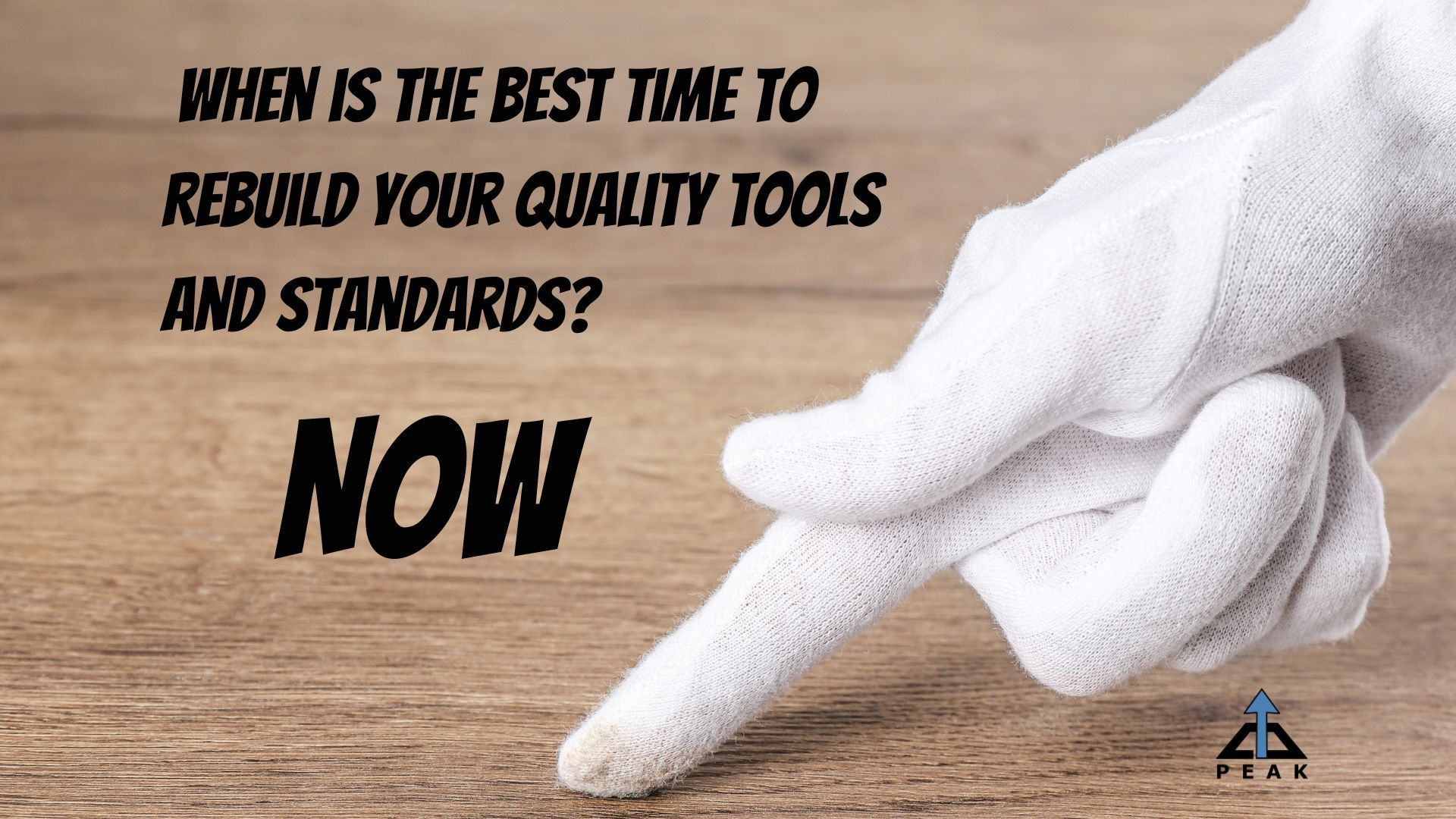
Introduction: In today's rapidly evolving business landscape, taking advantage of any slowdown in production to rebuild or upgrade your quality tools and standards is an effort well spent. This article explores how organizations can harness this period to enhance their quality practices to ensure for long-term success.
1. Implementing Quality Circles
During slower times, it's crucial to foster collaboration and idea generation among your teams. Quality circles are small groups of employees who meet regularly to identify and solve work-related problems. This can be a powerful tool for engaging the team during uncertain times.
Quality circles are a concept that has been around for decades, and the principles remain as relevant as ever. They provide a structured platform for employees to discuss quality-related issues, share insights, and collectively devise solutions. These circles promote a culture of continuous improvement, where every team member has a voice.
The implementation process involves several key steps:
- Formation: Identify interested employees from various departments. Seek to get representation from all job classifications and experience levels when developing the teams. The best examples I’ve seen are when they include people who have the ability and authority to get changes implemented, such as engineers.
- Training: Provide training on problem-solving techniques and quality improvement methodologies. Make sure to emphasize customer-supplier relationships, so the team members don’t only focus on what makes their jobs easier.
- Meetings: Organize regular meetings where members can discuss challenges and suggest improvements. Make sure you take advantage of going to gemba to see the problem firsthand. It’s also crucial to make a good set of team rules at the start so everyone understands the expectations and norms. Don’t allow individuals to hijack the meetings. If someone is not participating, use techniques to pull them in or replace them.
- Action Plans: Develop action plans based on the best ideas generated during meetings. Use the team members to communicate any proposed changes to the shop floor and management. It’s important they both take responsibility and show engagement.
- Tracking Progress: Monitor the implementation of these plans and measure their impact on quality. If an idea doesn’t work, explain that it was a good effort, but stop it. Treat their improvement efforts like you would any other and hold them to the same standard. They want to be respected on merit.
Quality circles empower your workforce to take ownership of quality improvement, fostering a sense of responsibility and engagement. If for any reason you are struggling with gaining traction in the beginning of the initiative – talk about safety or procedures that are difficult to perform. These normally include a quality aspect that needs to be improved. A few early wins usually get the team moving forward.
2. Developing Visual Tools and Samples for Inspection
Visual aids can significantly enhance your quality and production processes. This section discusses the creation and utilization of visual tools, such as checklists, flowcharts, and sample products to streamline inspections and maintain high-quality standards.
Visual tools serve several purposes:
- Clarity: They should provide a clear and easily understandable representation of process outputs, making it easier for employees to follow and adhere to quality standards. Unfortunately, most documentation is copied from engineering prints or quality standards that are often complex or require specialized training to understand. In some cases, these are 2D representations with shaded areas of 3D products to differentiate requirements by location on the product. Painted samples can offer a quick method for operators to compare for better understanding. Always test your instructions or samples to ensure broad compliance.
- Consistency: Clear visual tools ensure that everyone involved in a process performs it consistently, reducing variations and the risk of errors. Many visual inspection processes can’t pass an R&R inspection. In fact, many locations will avoid any test of their visual systems for that fact. You must find out what isn’t working and keep improving your visual tools/processes until they can pass it. Sorry, but there is no shortcut here. This is the only method I’ve seen work. Any expenditure upfront will generate huge payback compared to the costs of poor quality over time.
- Training: Visual tools aid in the training of new employees, allowing them to grasp processes quickly. Make sure you have enough tools available for operators, good tracking for quality inspections and a quick method to recreate them if damaged or lost (it happens). Make sure they are clearly labeled if you have similar looking products with different zones.
- Problem Identification: Standard Work processes can be improved to provide more clarity on instruction or better tests to alert workers of common quality issues. Many quality gaps are a result of a poorly designed work environment – make sure your processes don’t contribute to errors or mask them due to ergonomic or lighting conditions. Short term countermeasures should be SHORT TERM. Take the time to implement root cause solutions or the accumulation of short-term countermeasure costs will quickly turn into financial problems.
3. Source Inspections: Implementing Close and Timely Feedback Loops for Learning/Improvement
Embedded source inspection loops are a great way to ensure defects don’t get passed along to your customer. To achieve this, you must change your focus from searching for defects to searching for errors. All errors must be quickly communicated back to the source, so that action can be taken to eliminate the possibility of a defect being produced.
The sooner the better. If you can create solid built-in tests at the operator level, then they can self-correct for most variation. This may still require assistance from technical or management to bring processes back under control, but it will help them stop passing defects.
However, this is not always possible in many production processes. Often quality requirements are hidden from the view of the operator until much later. In these cases, you must provide excellent feedback to the source. I don’t know how many times I’ve spoken to operators who have no idea what their quality performance is, and/or only receive feedback on rare occasions like annual reviews.
- How can they improve if they receive NO FEEDBACK?
- What do you think the default condition is for an operator who receives no feedback?
- "NOTHING IS WRONG!"
- "I’m doing great!"
- "Rework and defects must be caused by others!"
- YOU MUST create systems to provide 100% feedback to everyone, and this must be done as soon as possible for every step in your process.
In my experience, over 95% of rework can be quickly and easily eliminated by solving the problem of effective feedback to operators. People want to do a good job – it is our responsibility to create systems that allow them to add value.
4. Preventative: Poka-Yoke Your Processes
Preventing defects is more efficient and cost-effective than fixing them after they occur. This section deals with the concept of poka-yoke, or mistake-proofing, and how it can be applied to your processes to ensure quality from the start.
Poka-yoke strategies aim to make it impossible for errors to happen. No errors = no defects. There are many excellent books and training courses available that provide details on how to implement prevention systems into your organization. Major strategies include:
- Design Improvements: Modify product or process designs to eliminate potential sources of error. For example, using unique / biased shapes or connectors to prevent incorrect assembly.
- Checklists and Guides: Provide workers with checklists, guides, or digital tools that assist them through each step of a process, reducing the chance of missing crucial tasks. For very critical or safety related work, having two groups read and check off tasks can be helpful to ensure compliance. A lot of early work on human systems and checklists were developed in the nuclear industry and have been incorporated into healthcare in recent years.
- Automated Inspections: Integrate automated inspection systems into your processes to detect variation in real-time. These can be very helpful in dangerous environments. Vigilance is required to validate periodically and ensure null-values default to error conditions in case of failure.
- Error-Proofing Devices: Implement error-proofing devices that prevent incorrect actions. An example is a car's automatic transmission, which doesn't allow you to start the car unless it is in neutral or park.
By applying preventative principles, you're not just catching defects; you're actively preventing them, which is a proactive approach to quality management. Effectively combining 100% source inspection, immediate feedback loops with reaction and poka-yoke can virtually eliminate defects in most production environments.
5. Focus on Visual Signals and Controls - Control Charts, Andon Signals, Tin Soldier Inspections
Visual signals and controls are essential for monitoring and reacting to quality in real-time. As I’ve discussed in prior articles, part of your standard work development should include building visual signals, showing performance to standard for both for input and output metrics. When you combine these with triggers and pre-determined reaction plans, they become visual controls.
One of the more common types of visual controls is control charts. They are a valuable tool for achieving process stability by identifying trends or variations. By regularly plotting data points on these charts, you can quickly detect when processes are deviating from the norm. Using some simple statistics, it is easy to determine if the variation is normal for your established processes or requires intervention on your part.
You can also combine control charts with pre-determined reaction plans to keep your process in check. For example, instead of adding many gallons of an acid solution to a mixture when the pH rises above acceptable levels, you can add smaller levels, checked more frequently to prevent the process from going out of control and shutting down. Control charts are often used when automated control systems are not in place, or to verify that automated systems are meeting requirements.
Andon signals, visual or auditory alarms can alert support personnel to quality or process issues as they arise, enabling immediate action. This not only minimizes defects but also promotes accountability and quick problem-solving. These can be triggered automatically or by production personnel in response to process shifts.
Most processes will have some type of quality check done at the start and finish of the run. This is important to show that quality is maintained between runs. However, this is only two points in time – and does not show variation from part to part or part to whole. If you ship in batches of products, it may be useful to conduct “tin soldier” inspections. Entire blocks or shipments are laid out as a group – lined up to help identify part to part variation. This can make it very easy to determine “what is different” and help establish where variation occurs in your process. When product runs on different machines or with different batches of materials, tin soldier inspections may be very helpful to proactively achieve consistent quality throughout your entire process. It's also a powerful way to instill a culture of quality consciousness by visibly seeing changes and then searching for the causes.
6. Challenge Your Conventional Wisdom and Assumptions
Much of the conventional wisdom and assumptions that your team uses are based on hard learned lessons from the past. However, it is not uncommon for them to be false and in fact responsible for much of the waste in your current design. I’ve encountered numerous issues where this is the case for many reasons:
- Variables shifted that gave the illusion the problem was solved.
- It was true for previous conditions, but now is wrong because those conditions have changed (larger, faster, etc.).
- Management said it was so.
It's easy to fall into the trap of "this is how we've always done it." However, change and improvement require a willingness to constantly question the status quo. Encourage your teams to challenge conventional wisdom and to test all your common assumptions. Do this regularly. Ask yourself – “How do I know this?”.
Conduct detailed root cause analyses to uncover the underlying reasons behind all issues. Seek to achieve “first principle” thinking about the basic assumptions and science behind your processes.
Most importantly, foster a culture where experimentation is encouraged, and failures are seen as opportunities for learning and growth. Don't be afraid to try new approaches, technologies, or methodologies that could lead to breakthrough improvements in quality.
Conclusion:
In times of reduced demand or slower business activity, the focus should shift from mere survival to strategic improvement. By implementing quality circles, leveraging visual tools, establishing feedback loops, adopting preventative measures such as poka-yoke, using visual controls, and challenging conventional wisdom, organizations can rebuild and fortify their quality tools and standards. This proactive approach will not only ensure resilience but also set the stage for long-term success in an ever-changing market.
If your organization needs guidance in revitalizing its quality tools and standards, Peak Productivity is here to help. Reach out to us to discuss how we can assist you in your journey toward improved quality and creating more stable processes to ensure sustainable growth.
Peaks and Valleys.....
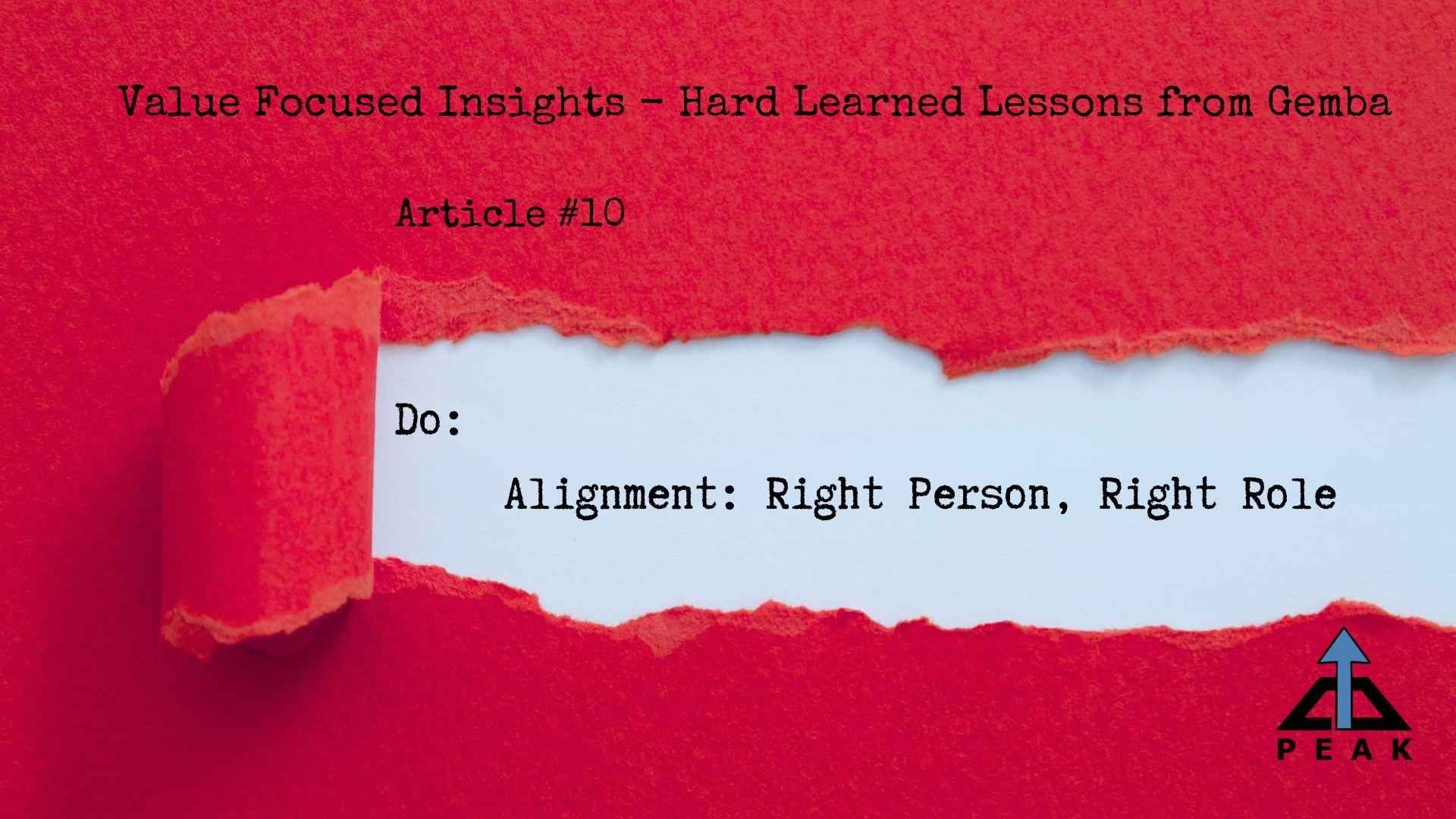
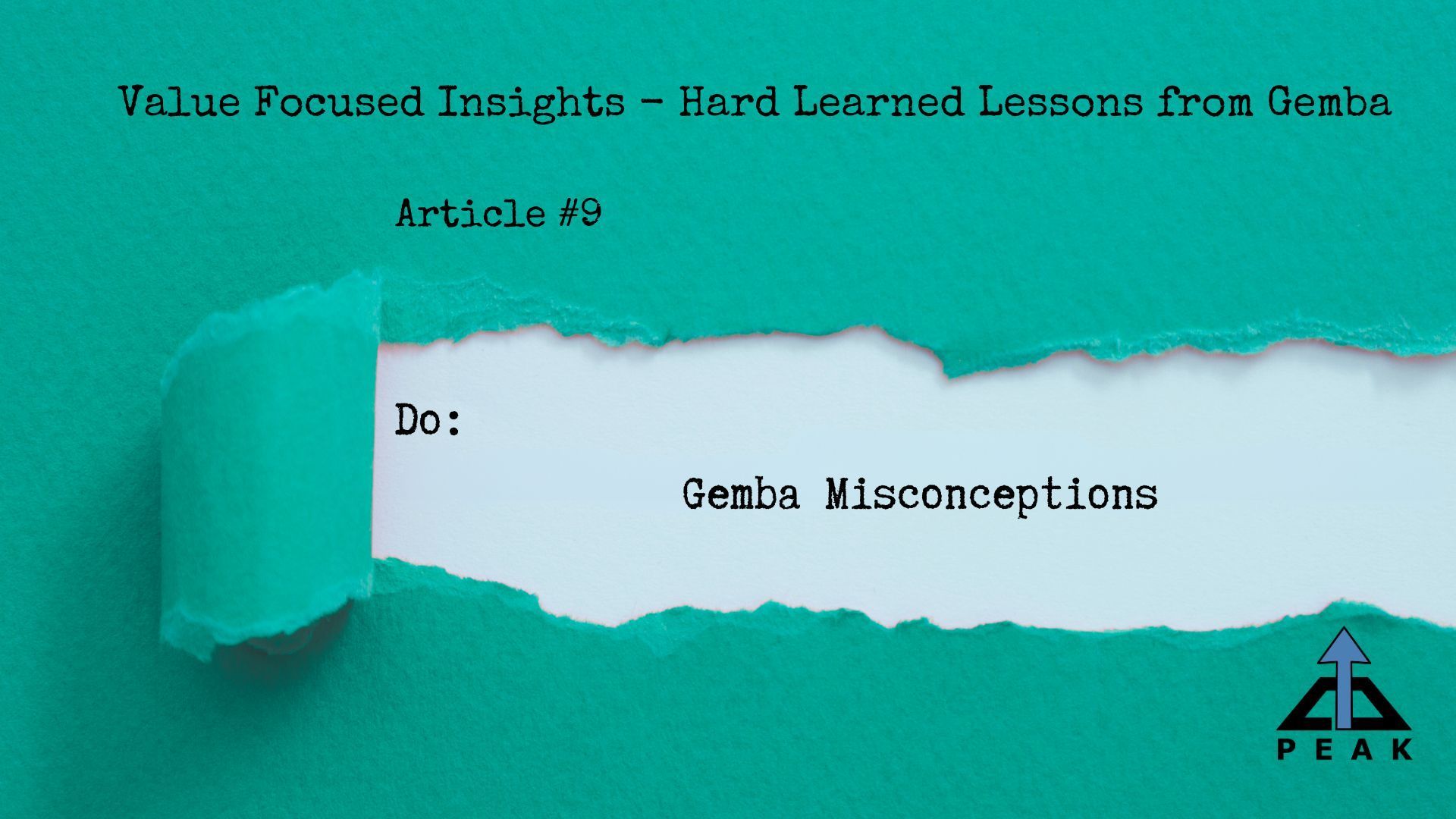
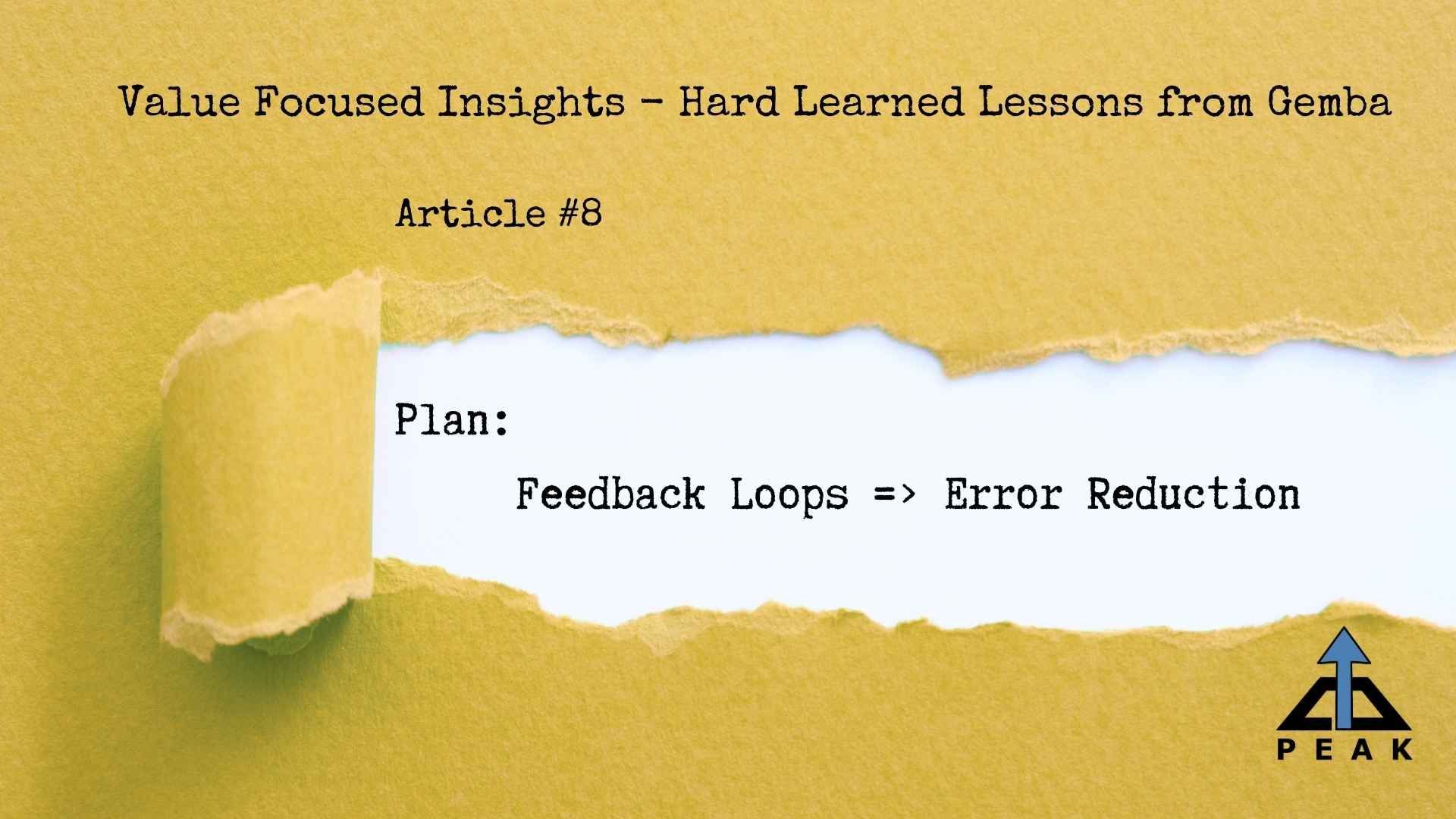
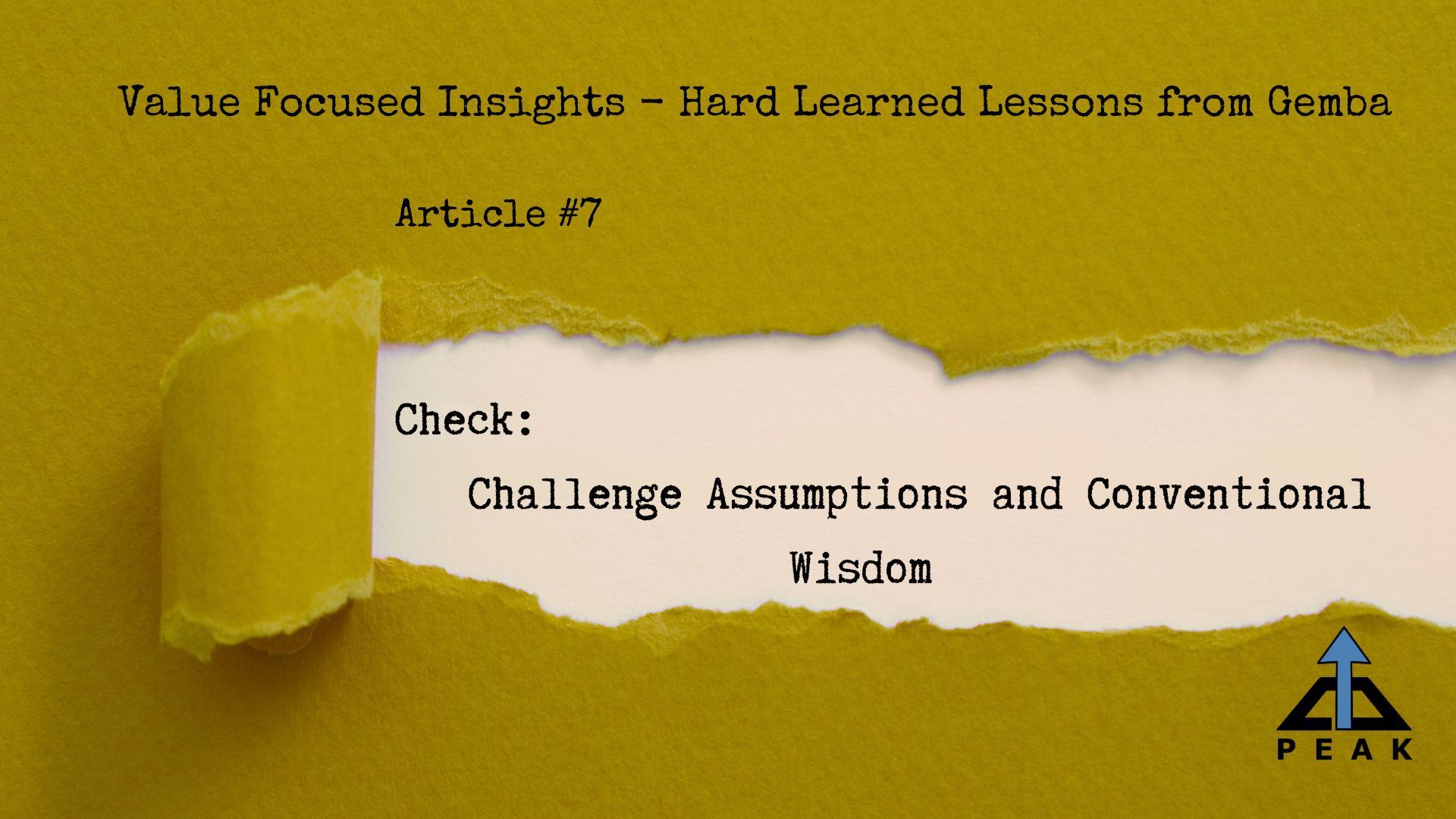
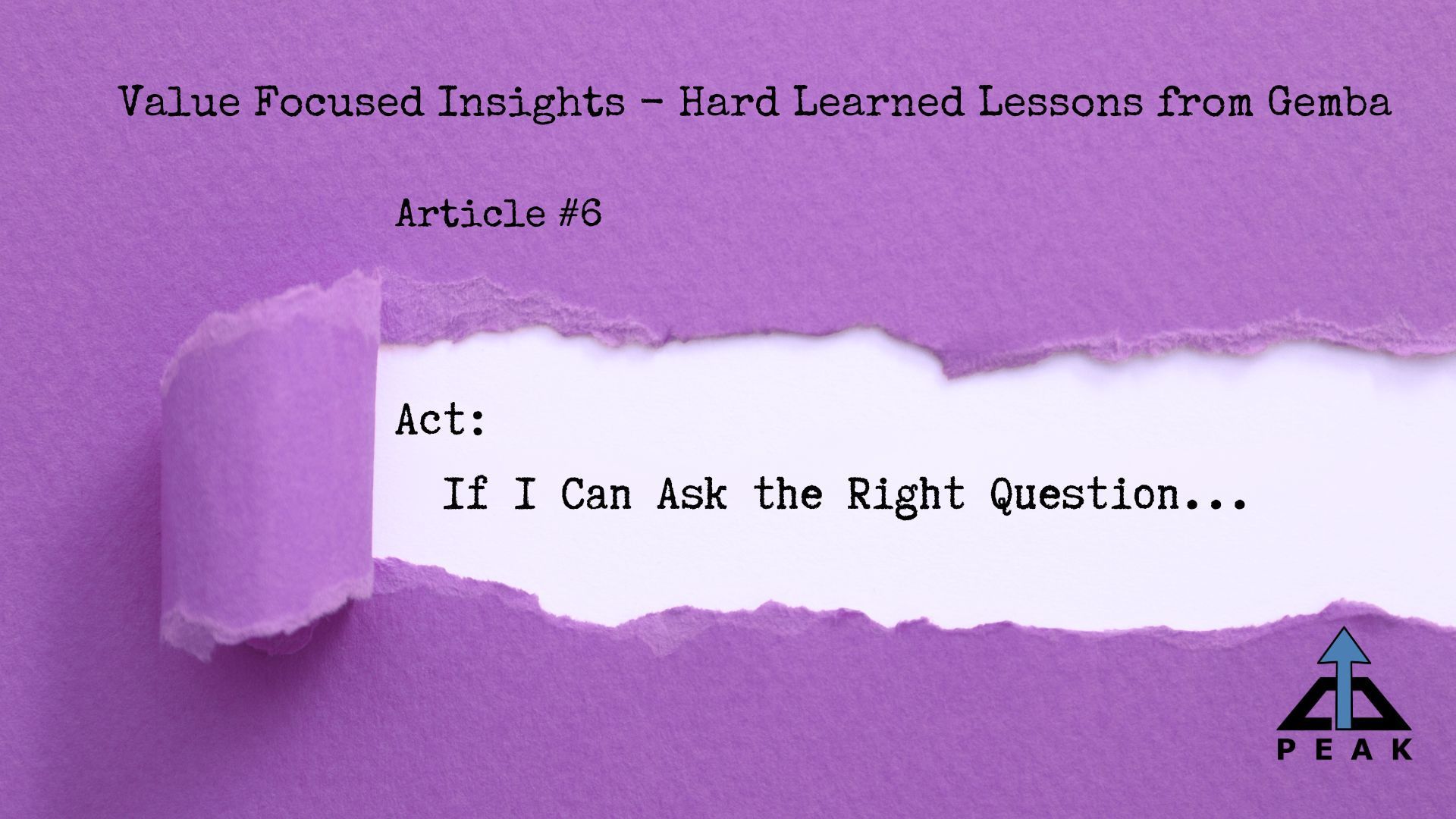
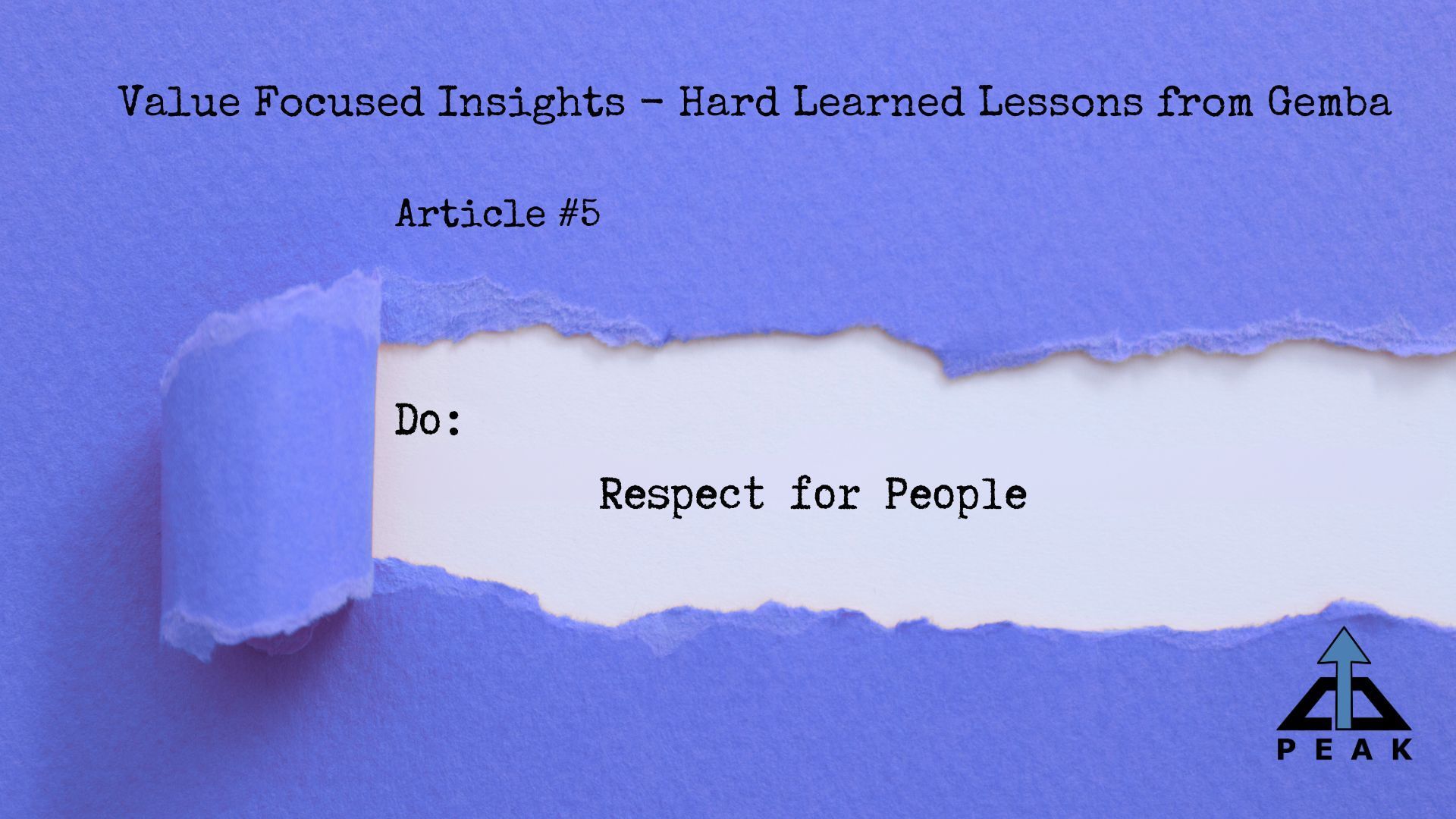
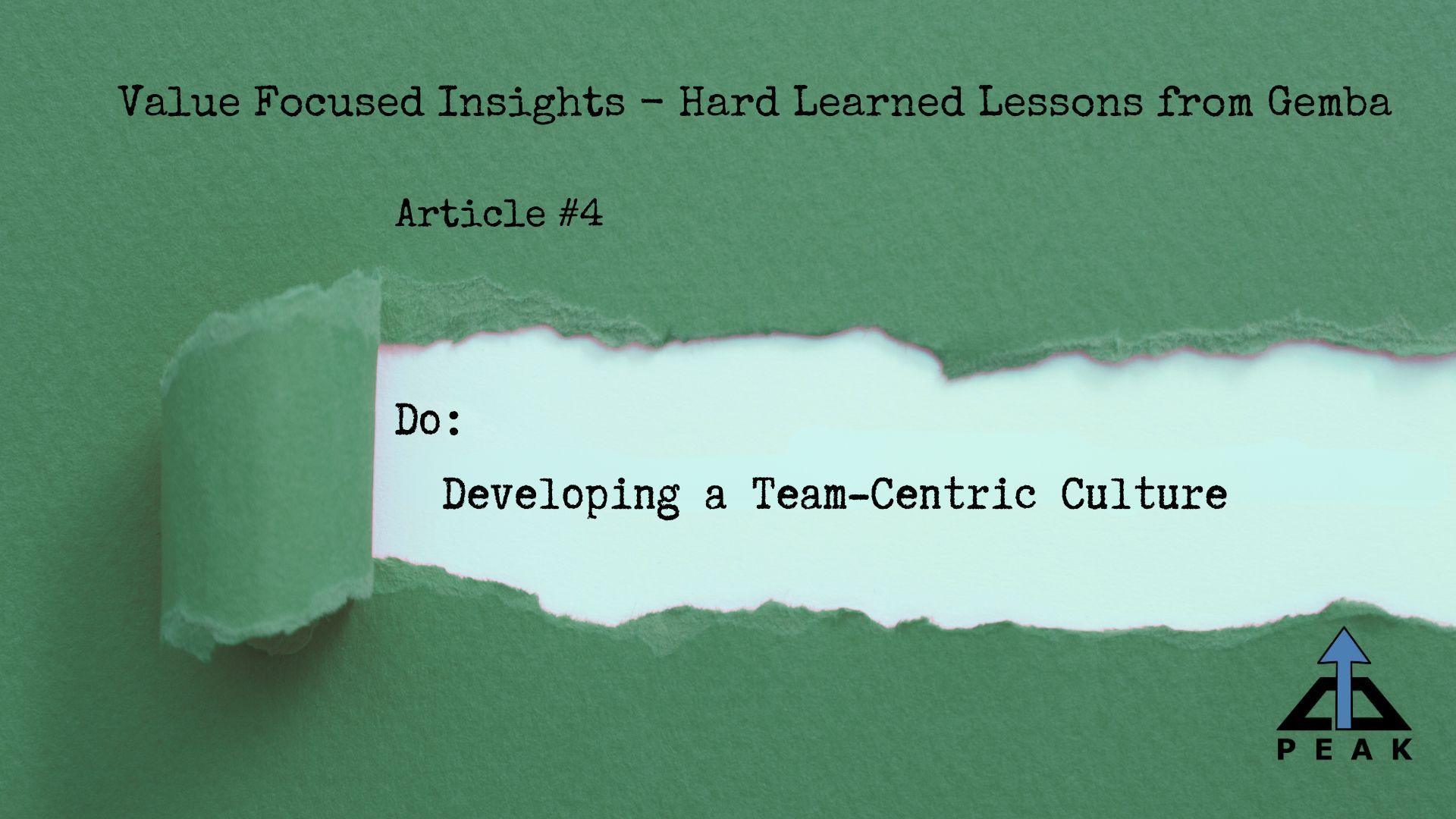
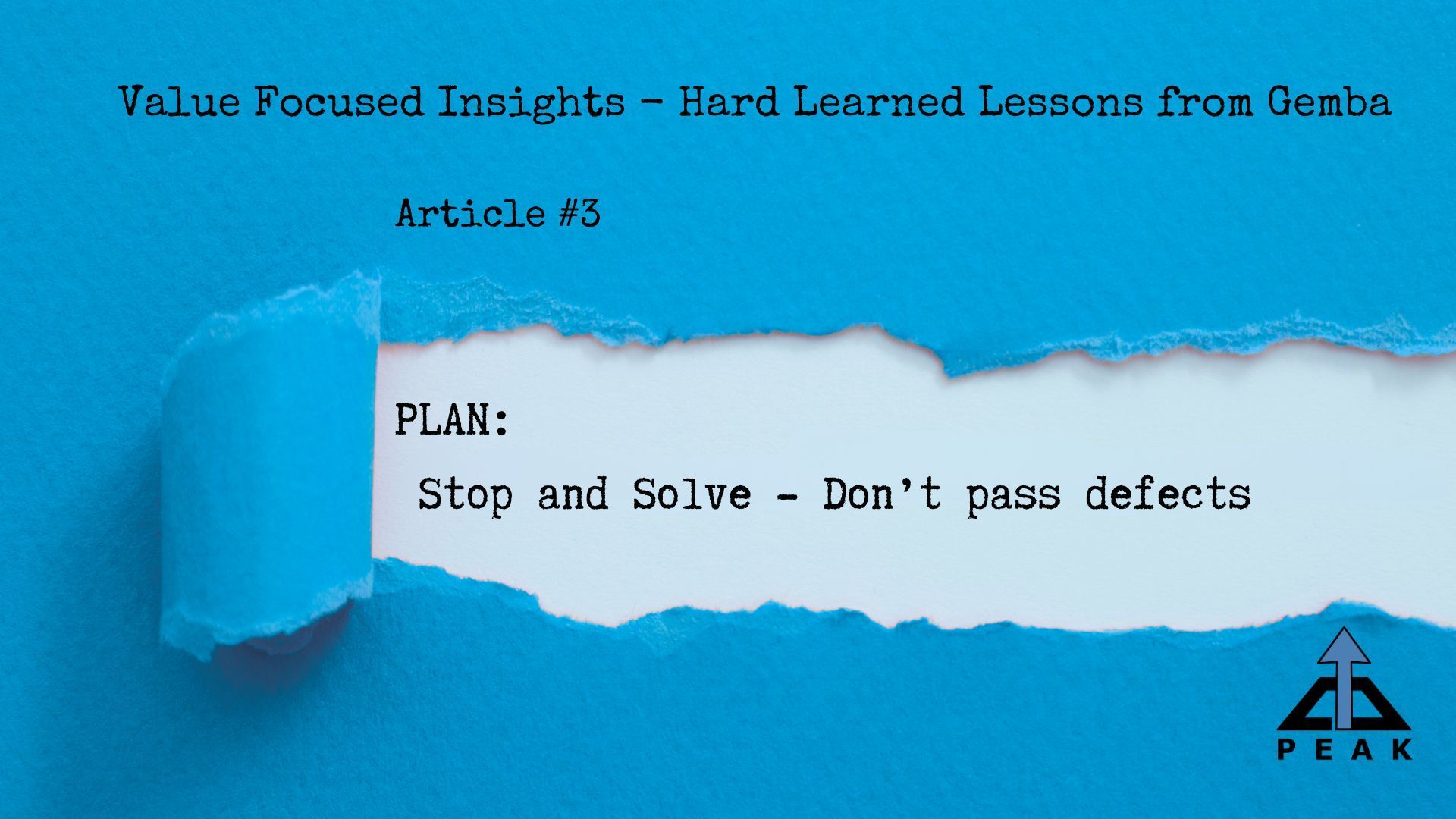
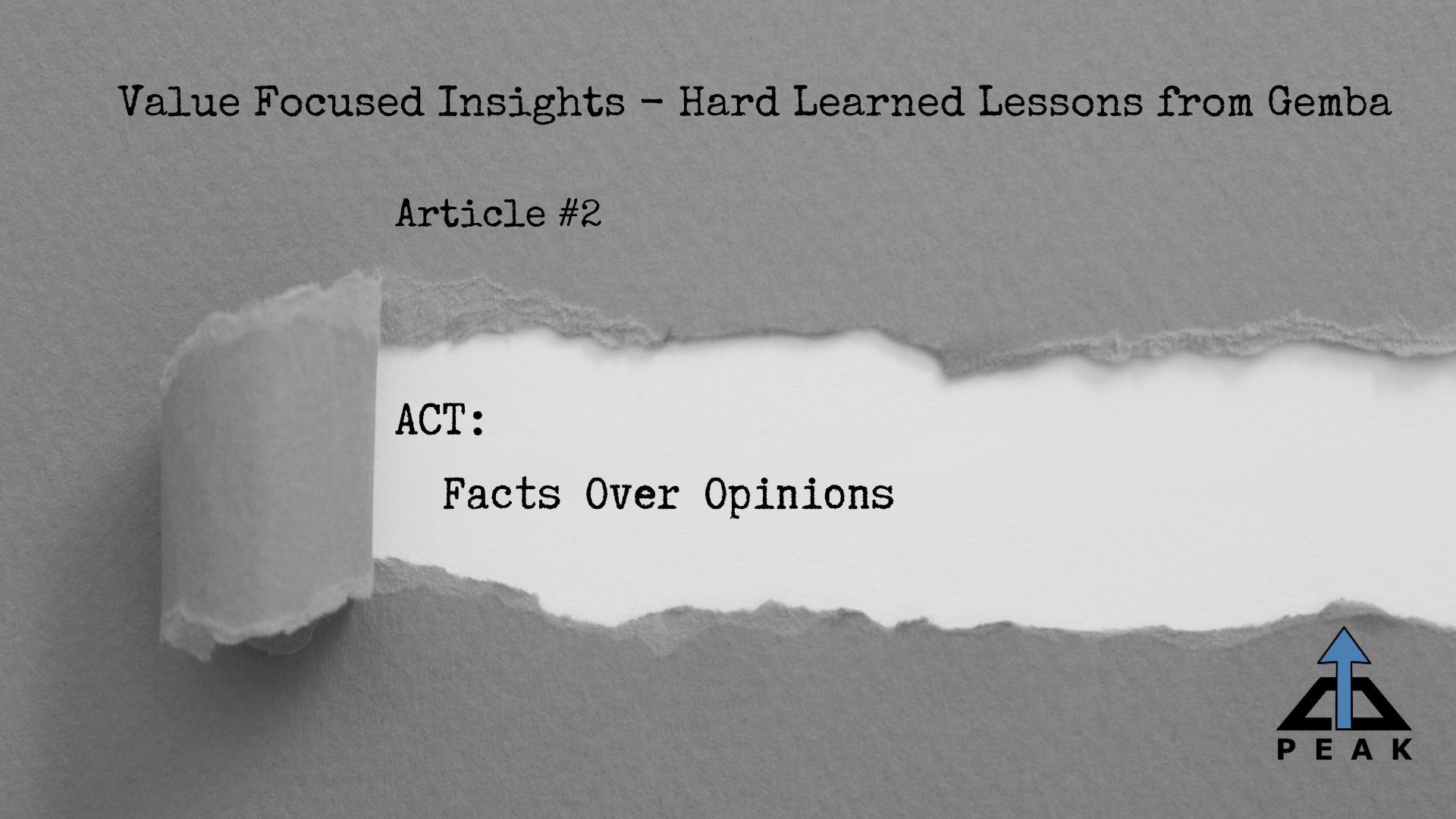
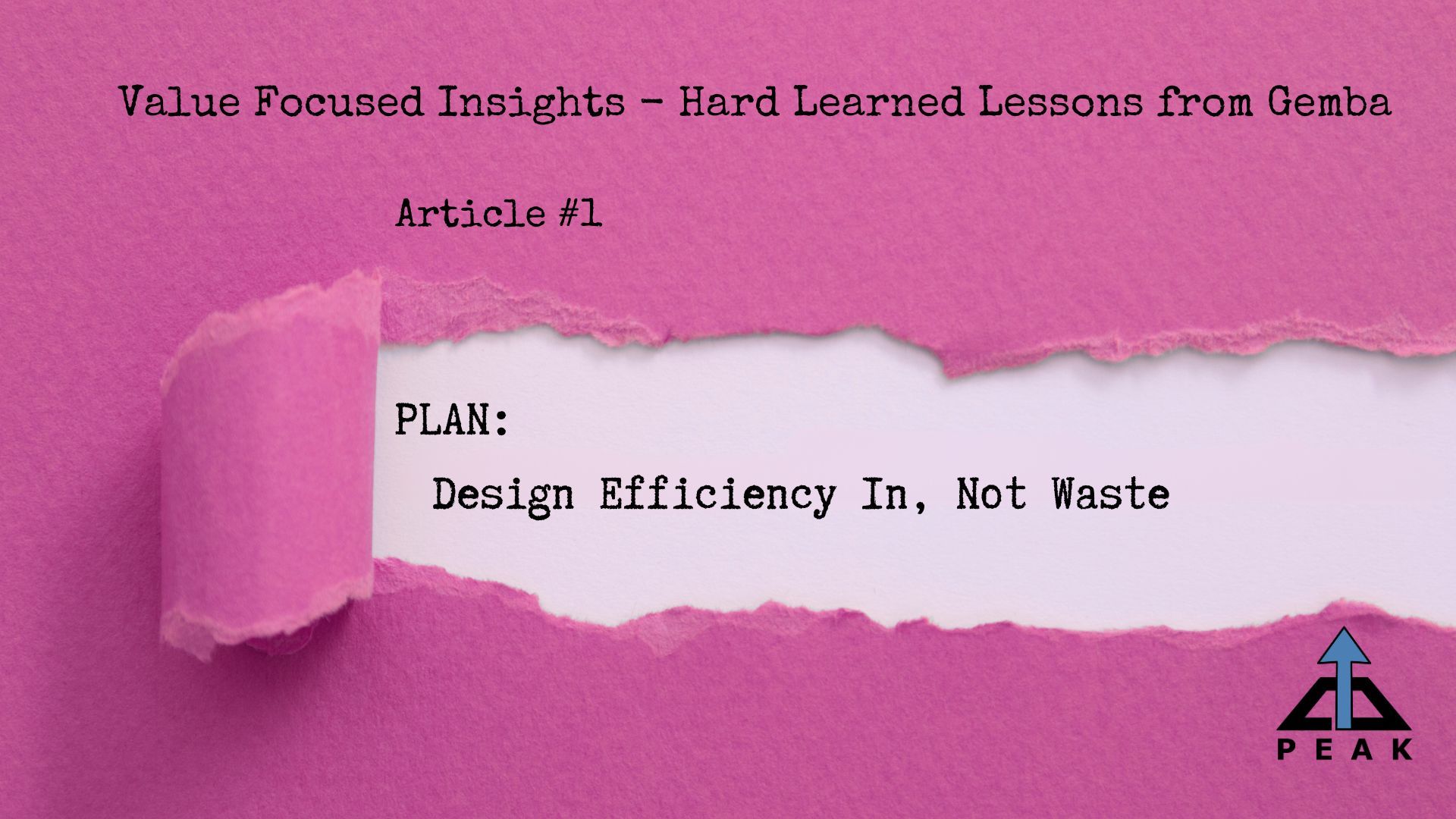