Embracing Slower Times - Part 9: Building Resiliency for Long-Term Success with SMED
Annah Godwin
In this week's blog, I continue the 13-part series "Embracing Slower Times: Building Resiliency for Long-Term Success" by applying SMED, Single Minute Exchange of Die. In this blog, I discuss what is SMED, how to apply it, and its' benefits. As always, I love hearing your thoughts and ideas on SMED, so post them in the comments section.
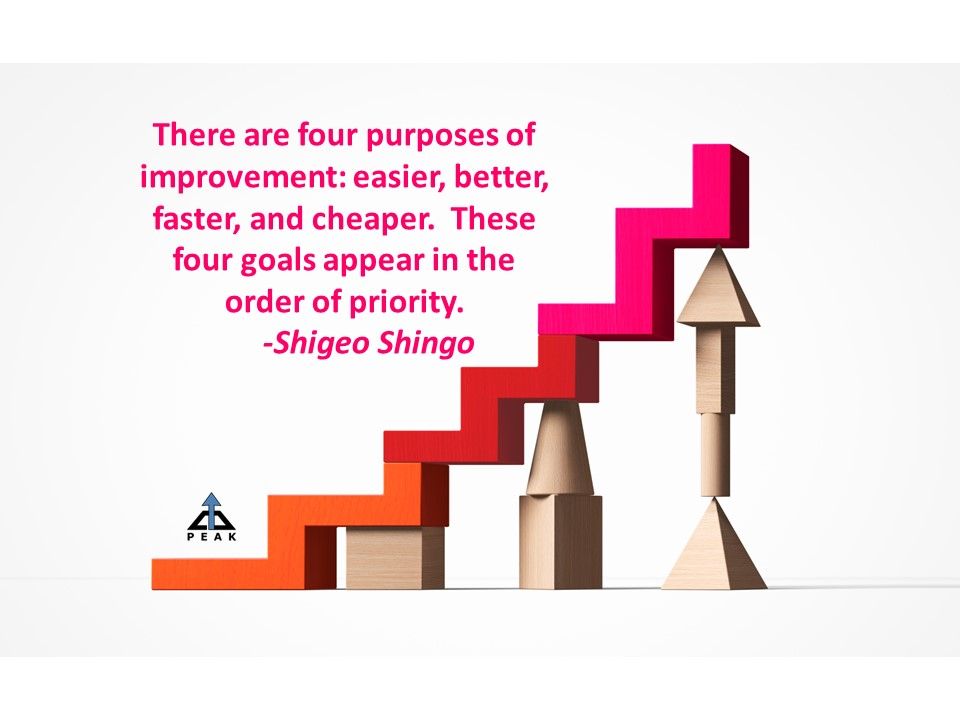
In blog 9 of the 13-part series “Embracing Slow Times: Building Resiliency for Long-Term Success,” I discuss SMED, Single Minute Exchange of Die. It is a set of tools deployed to reduce the changeover times and reduce the quality issues at start-up after a changeover. Just like most lean tools, SMED requires people, machine time, parts, and supplies to be successful. Usually, SMED teams include technical team members from operations, maintenance, engineering, tool room, purchasing, and quality. The team may focus on tasks like ordering correct tooling and parts, redesigning or modifying equipment, reducing quality issues, and 5S application, along with creating visual controls and standard work for the changeover process. Because of the skill set required for a SMED activity, slower times are the perfect opportunity for redeploying personnel to review the Value Stream Map, select process changeovers to improve, and implement successful solutions.
Let’s start by defining the term changeover. It is the time required to go from the last good part, through the equipment set-up, and ends when the first good quality part is produced. Some companies only include the time the equipment is not running but that misses quality issues and small tweaks required to obtain a quality product. Let’s say it takes 15 minutes to change the machine to the new set-up and an additional 20 minutes to get the quality right, your changeover time would be 35 minutes, not 15. Including both numbers is beneficial to highlight the dual focus on quality improvements and downtime. Quality improvements should provide pinpoint accuracy and minimize the amount of tweaking while downtime moves internal tasks to external, improves internal tasks, and runs tasks in parallel with each other.
Since most companies don't have enough product demand to create dedicated lines for only one product, the same equipment must produce multiple products, thus creating the need for changeovers. Most companies don't like changeovers because of the impact on production and output, while people don’t like them because of the time and work required. As a result, we try to avoid them. Typically, the longer the changeover, the less frequently the changeover occurs. This practice drives high inventory levels of some parts while creating outages of other parts. In extreme cases, it may be several days or weeks before the customer’s parts are produced. However, in that situation, the schedule is usually interrupted, and an additional changeover is added to produce the needed parts. This in turn forces another changeover to get back on schedule. These changes bring chaos throughout the process and the supporting, upstream, and downstream processes.
The reason to focus on SMED activities is that changeovers occur more often, which should produce a mix of products that aligns with customer's needs. SMED creates an environment for smaller batches of production and flexible and agile schedules that respond to day-to-day needs. It is a misconception to think the only reason to improve the changeover time is to reduce the downtime. It is not uncommon for SMED activities to provide reductions in cost by reducing inventory levels, creating less scrap and rework while increasing output.
What are the benefits of SMED activities?
1. Reduction in downtime of your machine. Every minute a machine is not running quality product; is a missed production opportunity. By reducing downtime, you can improve your output without increasing cost.
2. Quality focus and improvement. I have watched many processes that require a lot of time to get the quality right after the changeover. In some cases, it takes more time to get the quality right than it does to get the equipment ready to run. So, during a SMED event, the team should focus on how to get a quality part the first time. We all have seen machines and processes that run well, then you complete a changeover, and now the line just won’t run good product. This is where a quality focus during the SMED activities drives better yields.
3. Improved visual management. Using 5S, visual controls, and standardized work should improve quality outputs and help set clear expectations during the preparation and execution of the changeover.
4. Not just about machinery and equipment. I think there is a misnomer that SMED is all about equipment and machinery. I believe the methodology behind SMED can be applied to any process that requires a transition from task A to task B. A few examples of non-traditional changeovers:
a. A hospital procedure room being cleaned and prepared for the next patient.
b. A doctor's office exam room being cleaned and prepared for the next patient.
c. A landscape crew completing work at one client’s property and starting work at another property.
d. A customer service representative completing one call and starting the next.
e. An office team member completing one report and starting another report.
f. A hotel housekeeper finishing tidying one room and starting the next.
None of these examples included changing over equipment, but they do have a common thread of finishing job A and moving to job B. So, you could apply the same methodology deployed for a traditional SMED activity. Start by observing the process to see if the person had the tools and supplies, they needed. Did the person know what task to complete next? Was the quality acceptable from the start, or were corrections needed? The answers indicate if non-traditional SMED activities could benefit your processes.
How do you perform a SMED event? In an ideal state, a changeover is completed in 10 minutes or less. In my experience, that is usually not achievable with the first SMED event, so you may start by setting a target of 50%-75% reduction. A SMED event typically is formatted as a kaizen activity so before beginning the activity create a team charter, select the cross-functional team, and spend time at the Gemba collecting data on the current changeovers. If the changeover time is short and occurs frequently, then the team should observe several iterations of the process. If the changeover is long or occurs infrequently, you may want to video a changeover and then use the video for the team to observe. If you video the process, include all the operators and steps.
Once you've completed the observations, you're then ready to create and prioritize the list of improvements. Possible improvements may include:
· 5S toolboxes and tools.
· Visual display board and tool work boards. Along with color coding the tooling.
· Standardized work of the process for changeover.
· Equipment modification and testing.
· Equipment and tooling repair.
· Tooling replacement.
· Quality tooling and gauges replaced or repaired.
· Quality standards posted.
· General cleaning and repairs.
· Prepping for a changeover to reduce internal tasks (tasks that can only be completed when the equipment or line is stopped)
At the end of an SMED event, complete a new time study and verify other deliverables like inventory levels and scrap rates.
Can your company benefit from SMED? Look at the questions below and see if any of them seem familiar.
· Do your changeovers take more than 10 minutes?
· How much time does it take to get the quality correct after a process has a changeover?
· How many people are involved in a changeover?
· Do you find your customers are waiting on parts that are scheduled to be run later?
· Do you find you have outages of some parts and products and a surplus of others?
· Does your WIP between processes have large swings of high and low levels?
· When you observe a changeover do they run smoothly and seem well planned? Does everyone have the parts, the products, and the materials and tools they need?
· Does the line know what product is running next?
· Do you see team members assisting one another during a changeover?
The answer to these questions will help you see it’s time to build long-term success by applying SMED tools to your changeovers.
Hopefully, this article has provided insight into SMED, why perform SMED activities, and how it can help build resilience for future success when things are slow. At Peak Productivity, we are always interested in hearing your thoughts and your comments, so feel free to post in the comments section. Also, post your questions or your experiences with SMED work. And as always, if you've missed any of the series of these blogs, feel free to check them out at our Peak Productivity website.
Peaks and Valleys.....
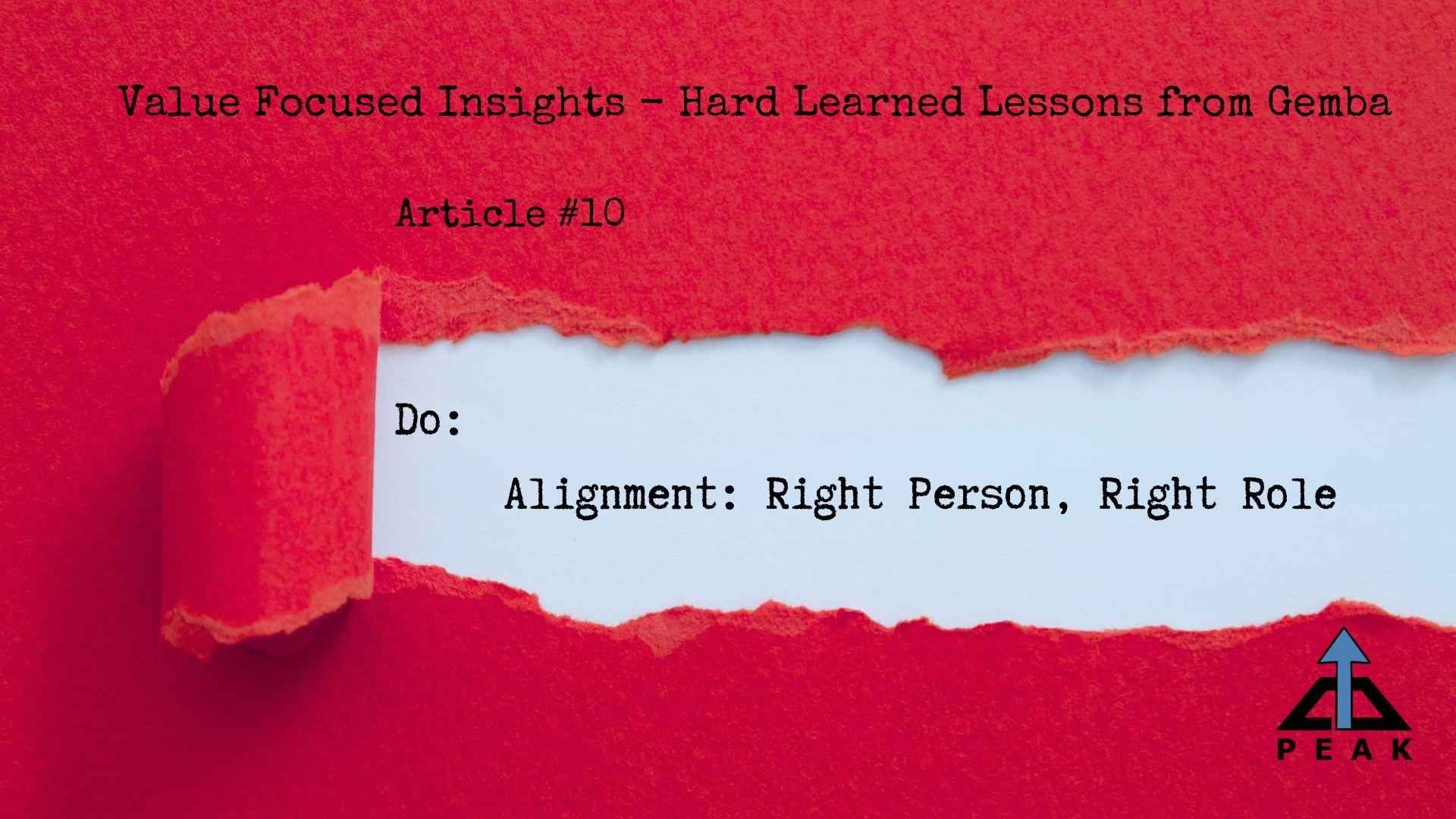
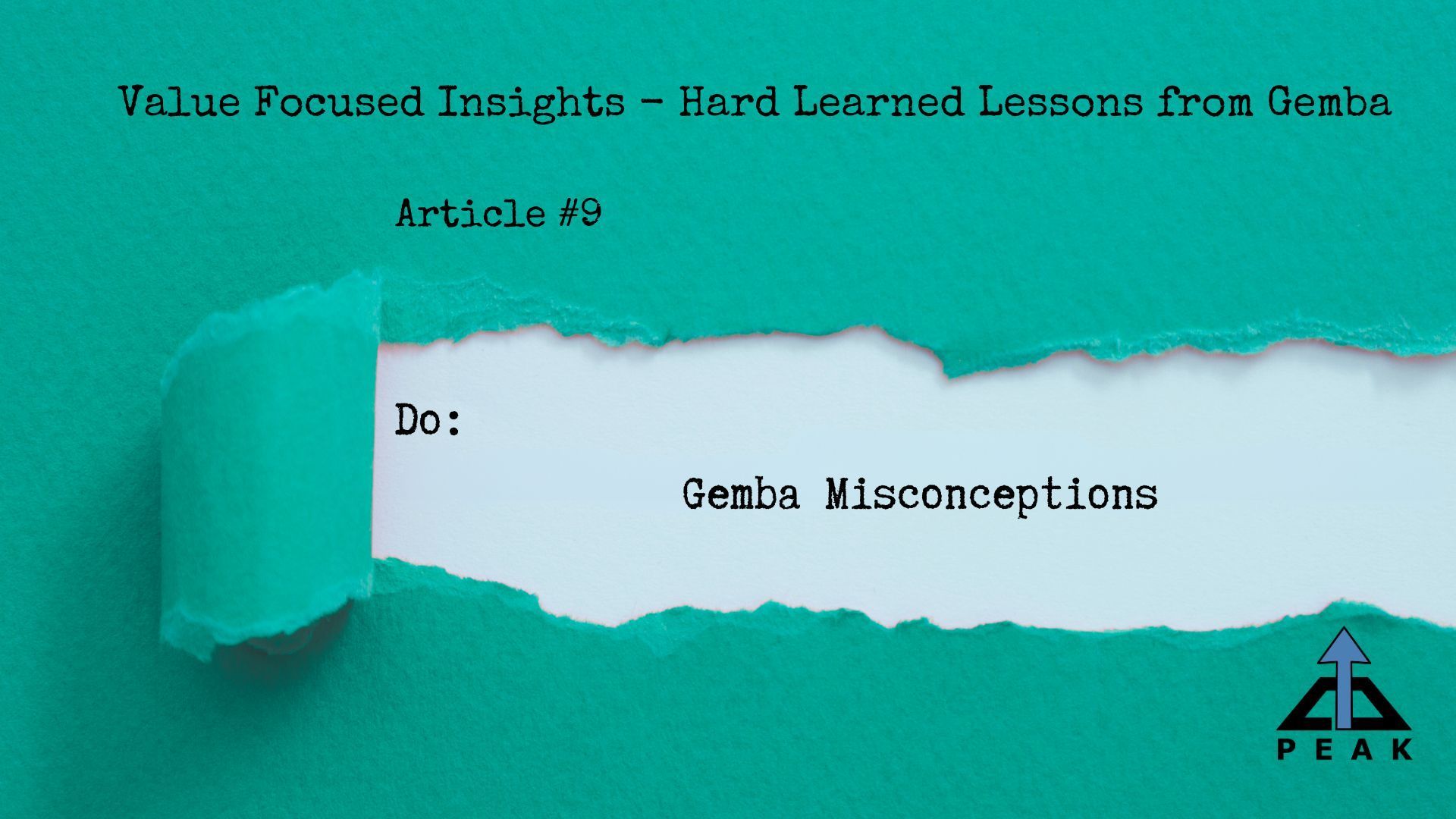
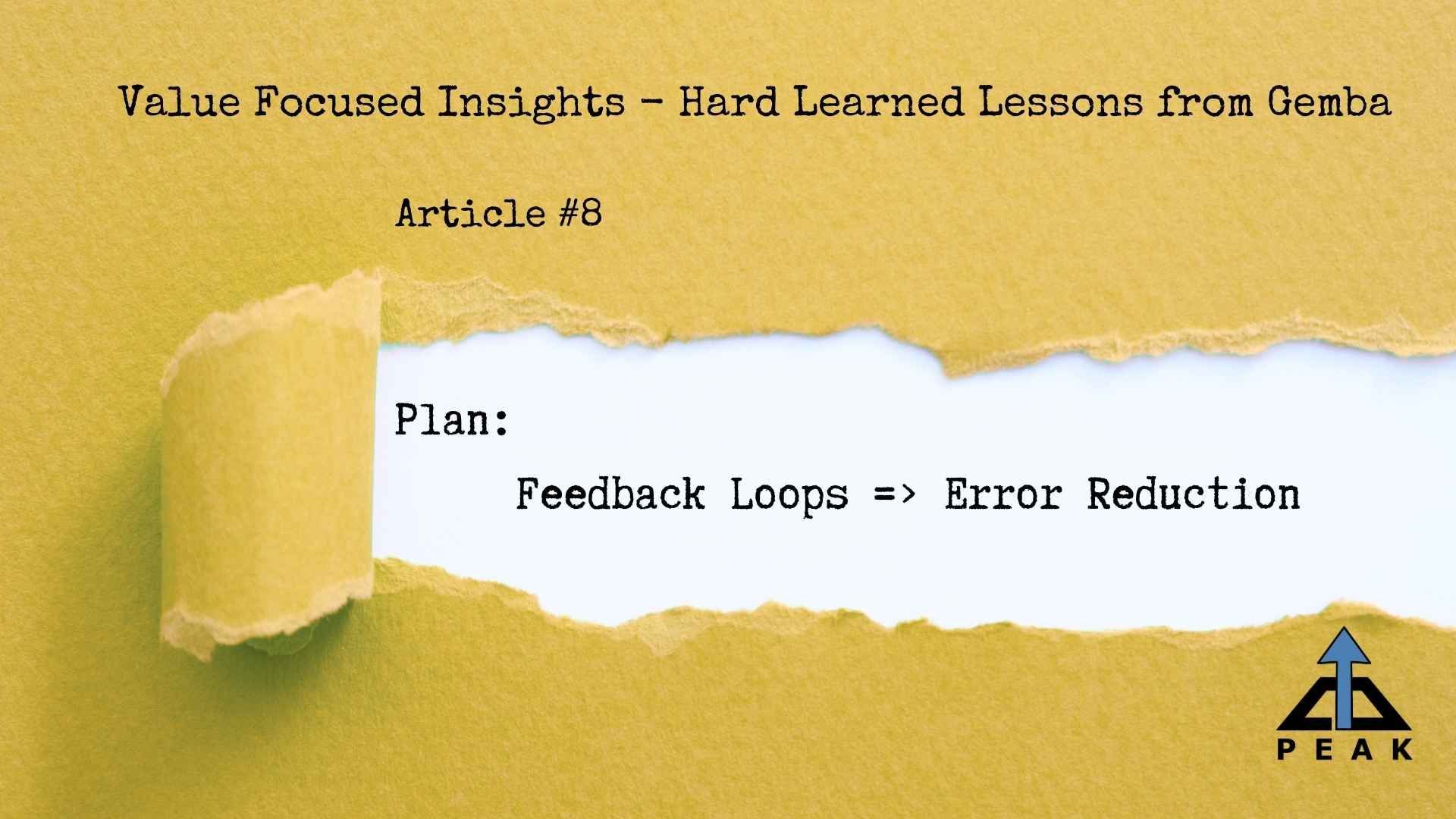
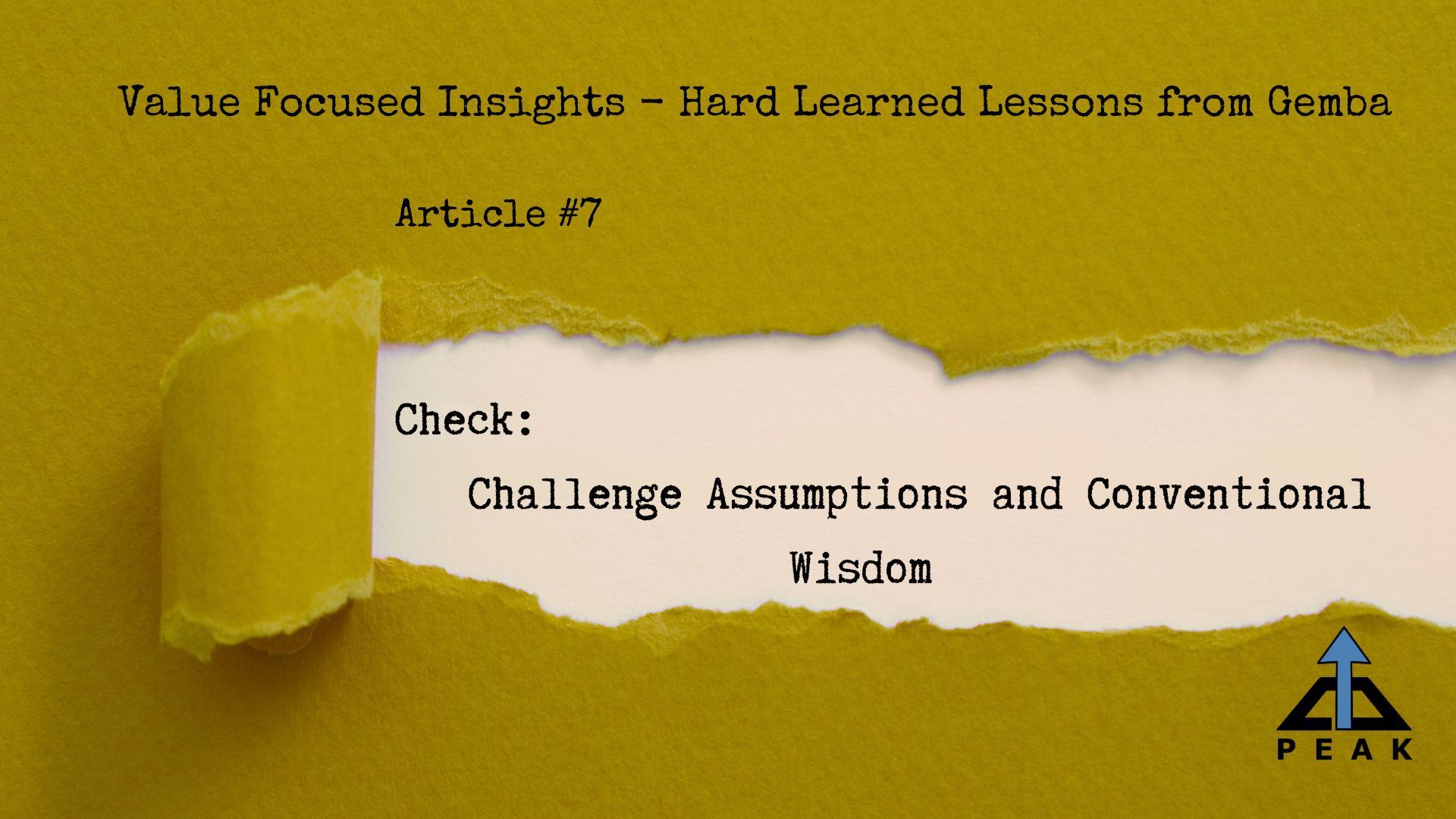
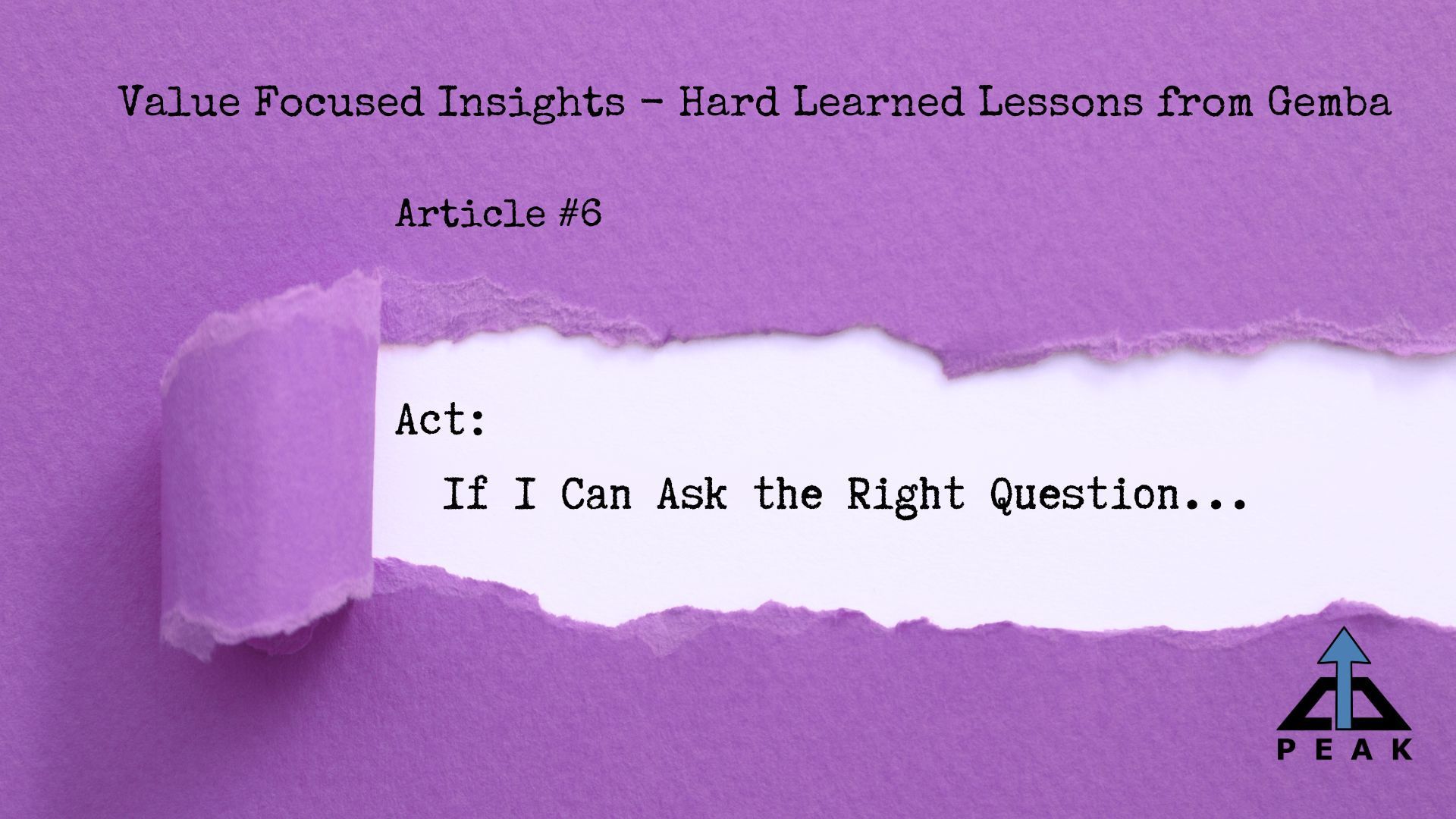
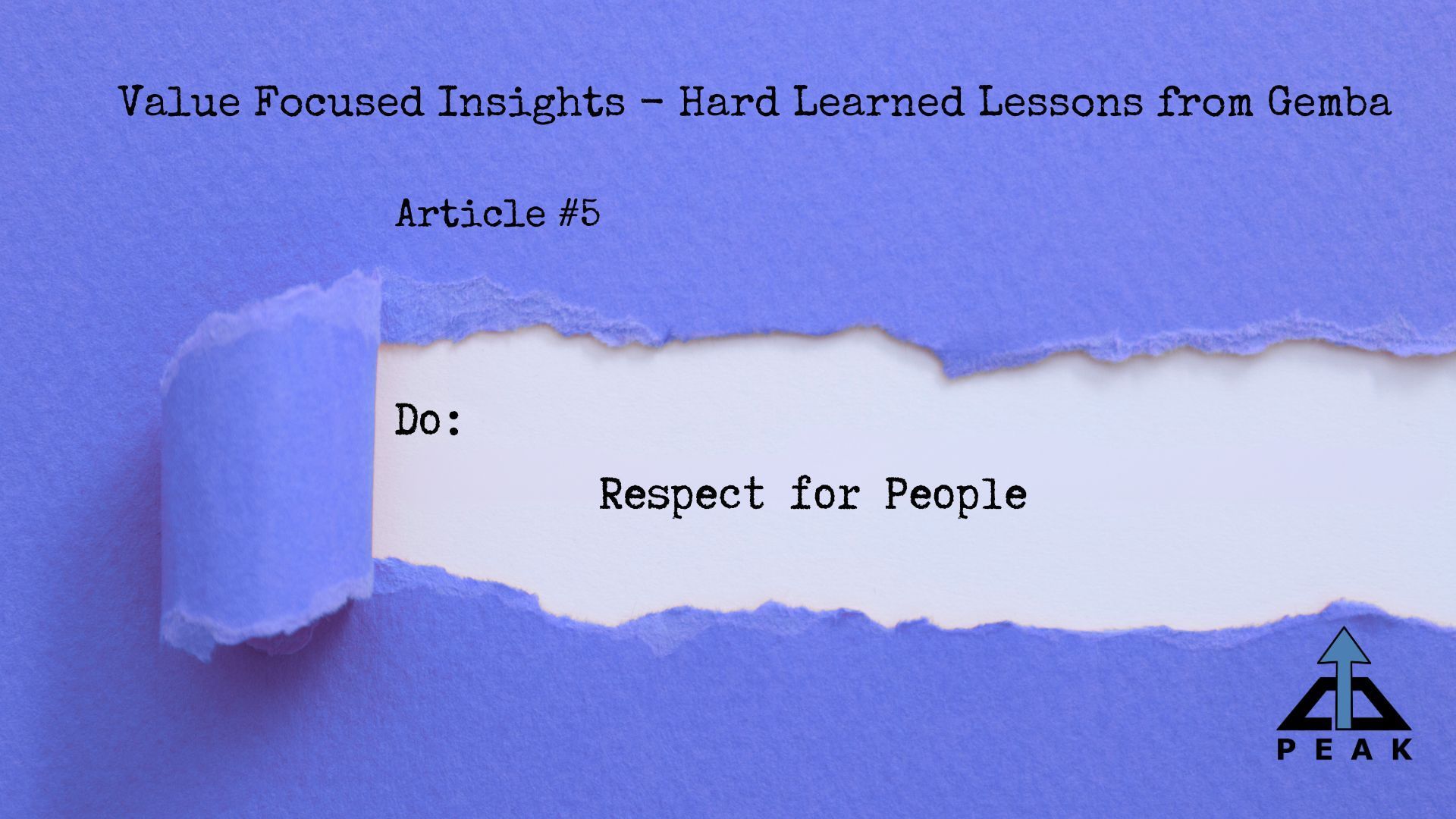
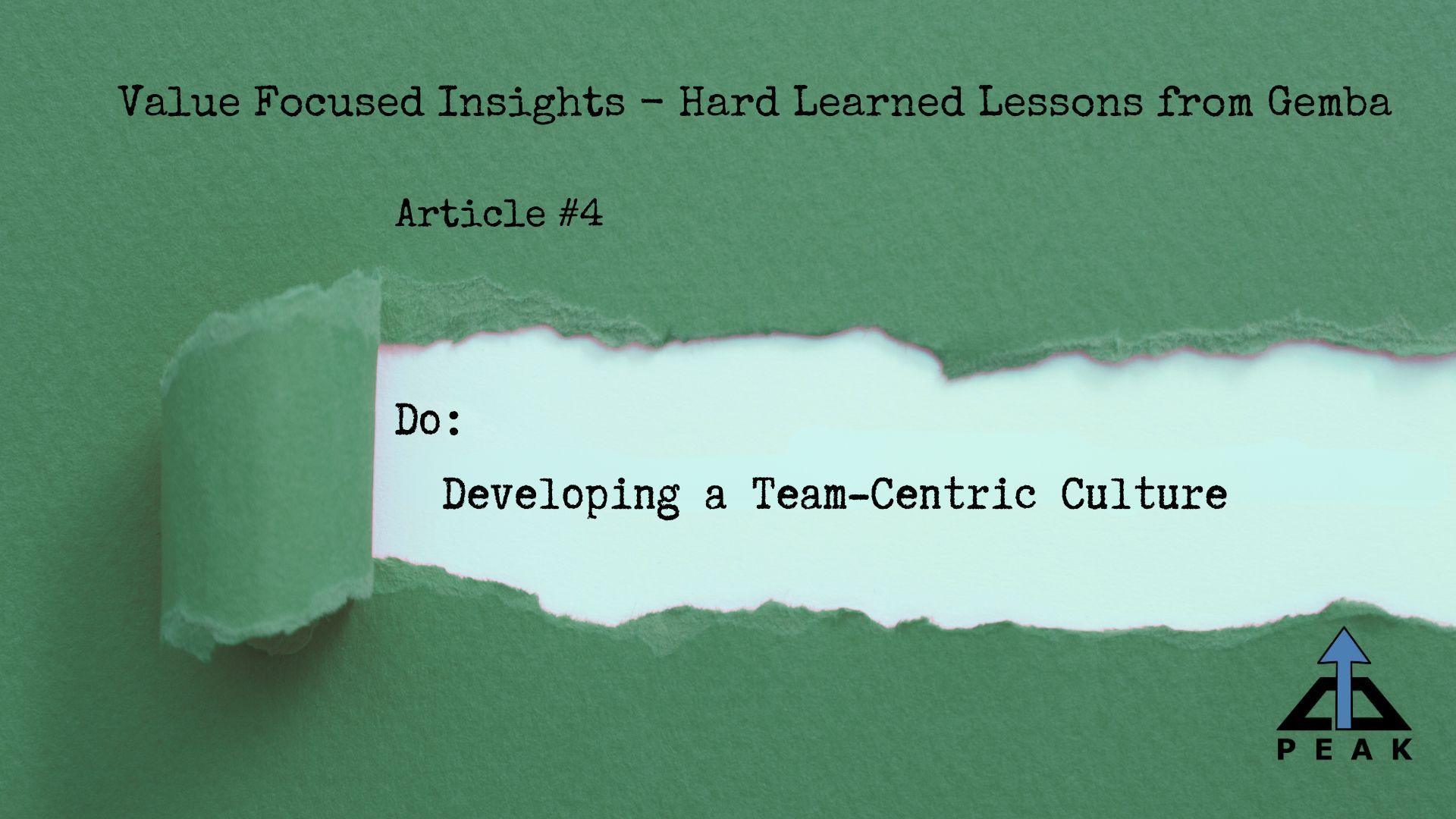
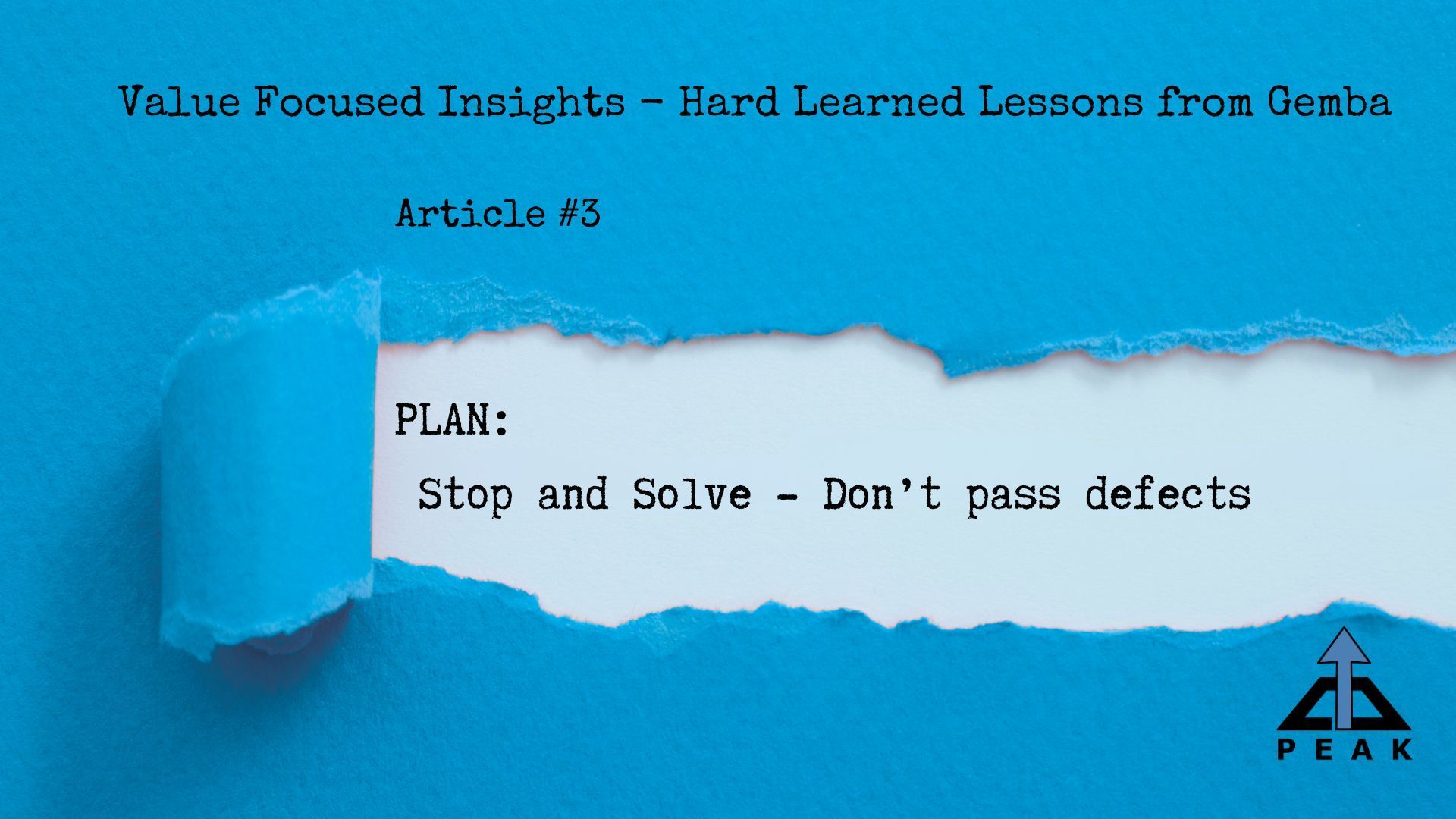
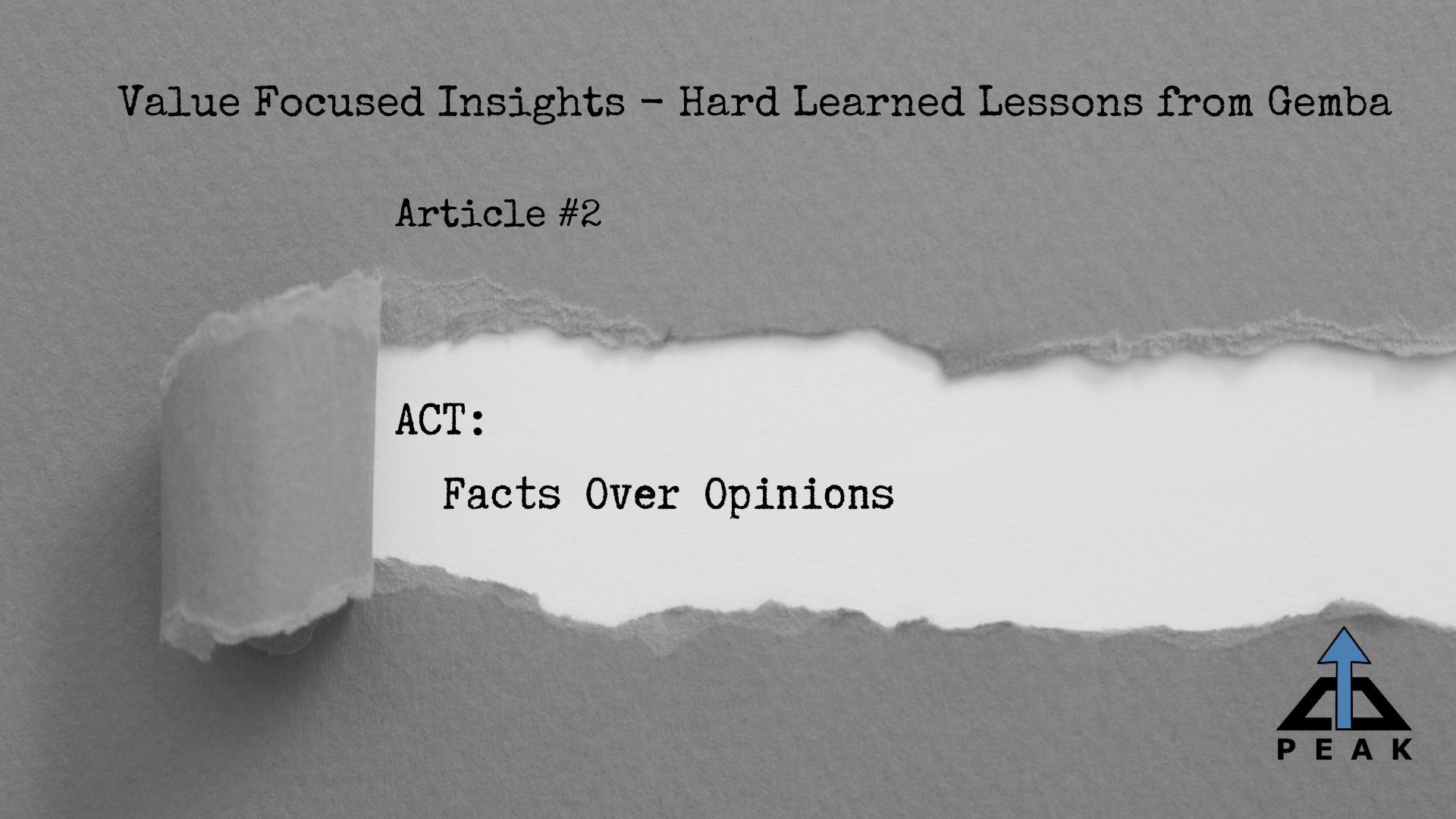
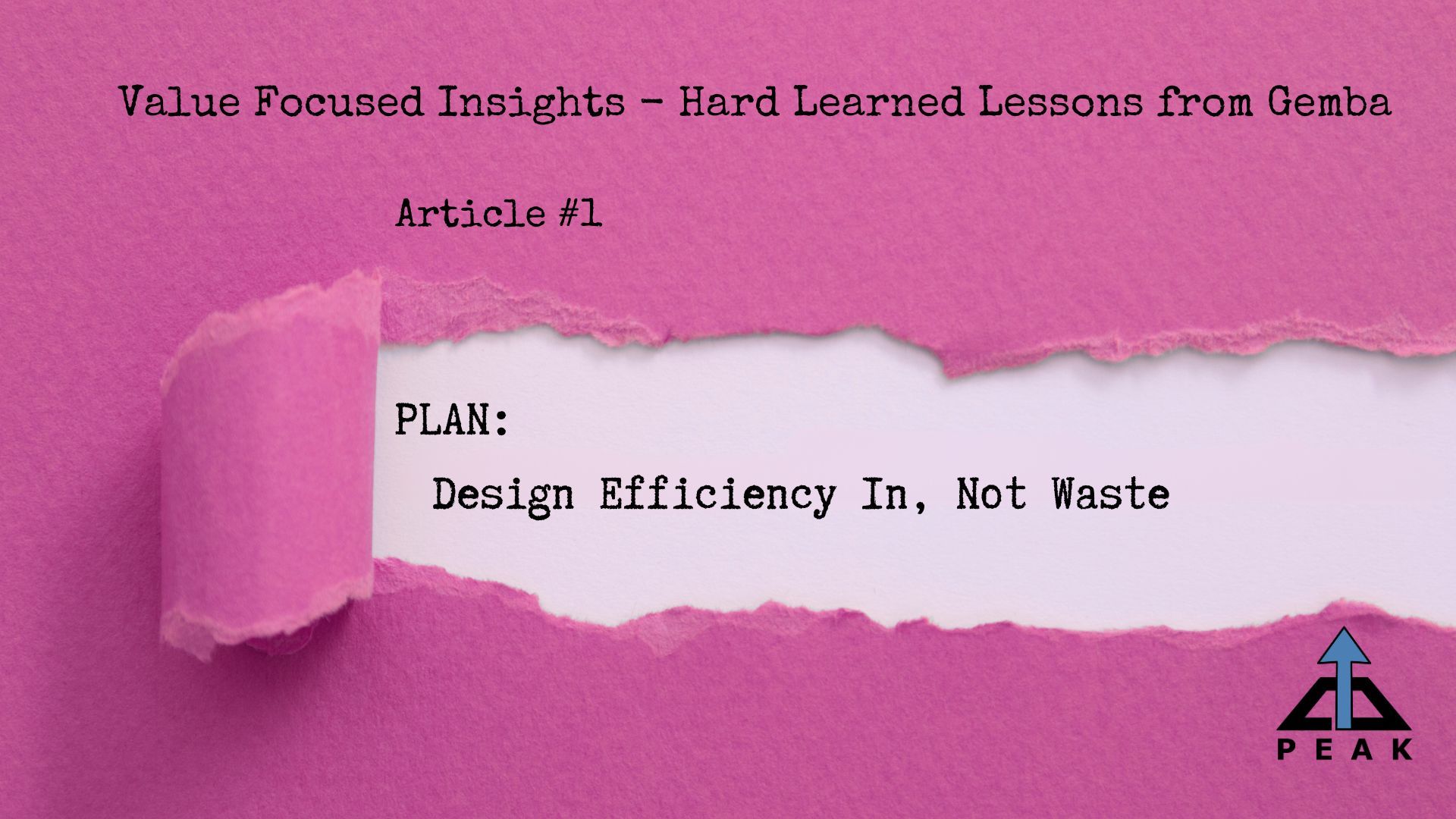