Embracing Slower Times - Part 8: Unleashing Efficiency through Total Productive Maintenance (TPM) Applications
Tim Upchurch
Unleashing Efficiency through Total Productive Maintenance (TPM)
Hint: It's NOT about just checking the boxes....
Welcome to the next installment of our series on building resilience during periods of lower demand. This article will address some practical applications and strategies for implementing Total Productive Maintenance (TPM) in your organization. This is a key toolset for enabling process stability and helping your team on the path to continuous improvement.
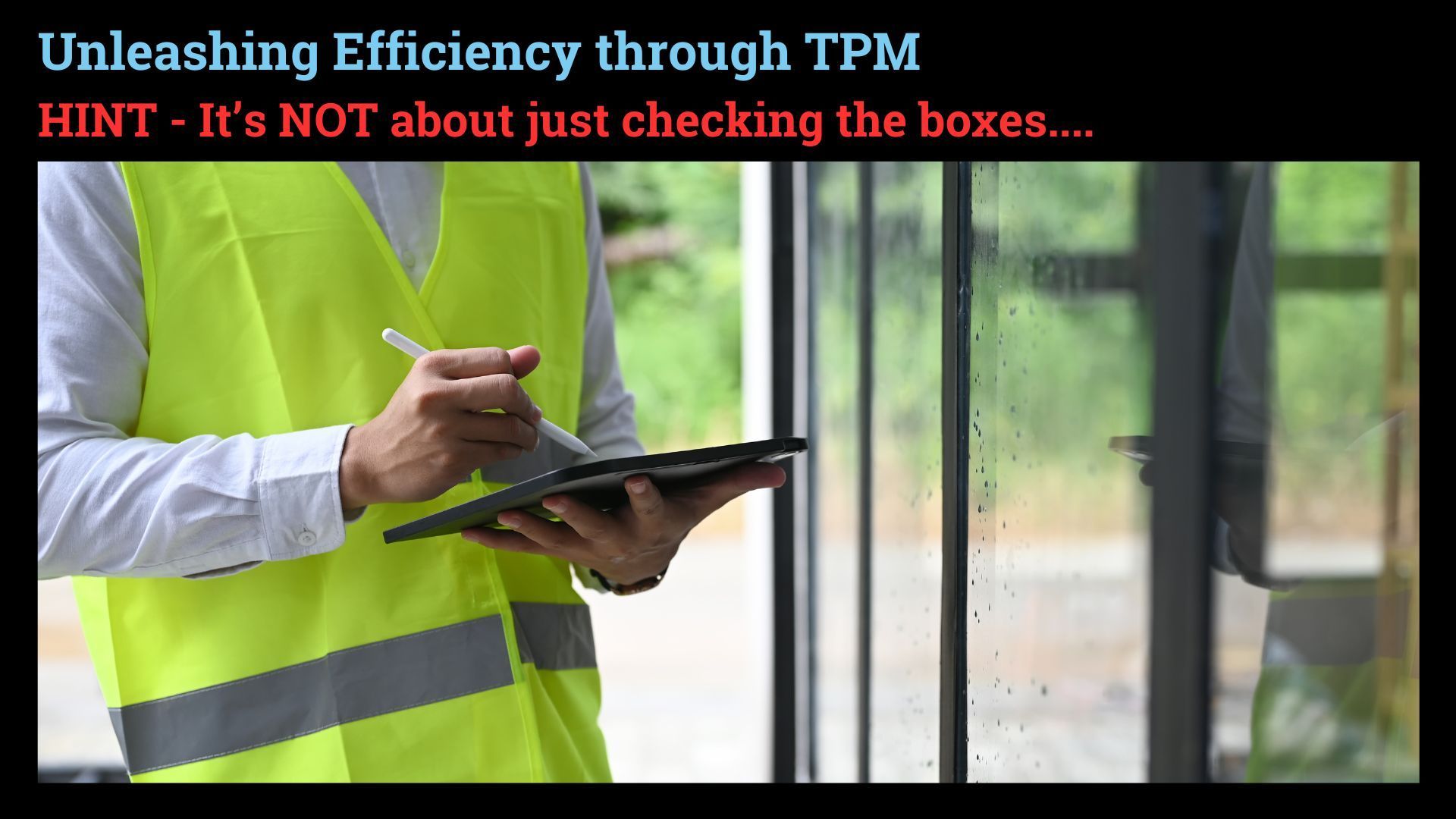
In this article, I will be discussing Total Productive Maintenance (TPM) – a comprehensive approach to increase equipment reliability, boost productivity, and drive continuous improvement. For machine-based processes, TPM provides a solid foundation for organizations seeking stability and long-term success.
Without stable equipment to support your processes, output can vary greatly due to downtime and yield losses. If your current environment is one of constant firefighting – then perhaps TPM is a toolset you should consider looking into during slower times.
There is a vast amount written on TPM that is readily available for your team to access. I would suggest that before you seek to copy/paste these tools, you look closely at your specific business case. I would approach the application of TPM tools just like any other. I would look for ways that support my unique processes and equipment, while providing an excellent return on any investment. I will focus this article on those tools that can pay the quickest returns for your efforts.
Your customer wants good quality products, on time and at a reasonable cost. They normally are not willing to pay extra for you to have a TPM system. So, you will need to develop solid financial analysis to justify the cost of implementation to your management team. Without good historical data, this can be difficult. I recommend you start with a simple understanding of your true output capacity for each step in your process. If you’ve followed our series, you should have a good understanding from our Value Stream Map article. Assume no restrictions at first – unlimited demand, with unlimited inventory to run, no yield or startup losses, and your current process mixture with zero setup and changeover time. It should be your total scheduled time multiplied by your designed output rate. This is your Scheduled Calculated Capacity for each step in your process. Your Total Calculated Capacity is your output if you ran 24X7.
Compare the scheduled capacity to what you are currently producing in shippable product. The difference is your potential opportunity. You have also just provided yourself with a simple means of approximating your Overall Equipment Effectiveness (OEE), and your Total Asset Utilization (TAU).
- Your OEE = Current Good Output / Scheduled Calculated Capacity
- Your TAU = Current Good Output / Total Calculated Capacity
Your final number will be a percentage less than 100%. Your total opportunity is 100% - Your TAU.
OEE and TAU: Measuring Performance and Downtime
If you want to calculate your OEE and TAU exactly, then you will have to first calculate the component metrics and then multiply them all together. There are many common misconceptions about these metrics that can hinder your improvement initiatives. I’ve included some key points to always keep in mind when communicating them.
OEE measures the efficiency of equipment by assessing the product of the availability, performance, and quality. OEE provides a comprehensive view of equipment performance compared to the organization’s plan and helps identify improvement opportunities. You can perform the calculation for a specific piece of equipment or combine for a collection of machines.
OEE = OA X PR X QR, where:
Operational Availability (OA) = Actual Runtime / Total Available Time
Productivity Rate (PR) = Actual Output Rate / Designed Output Rate
Quality Rate (QR) = Good Product / Total Product Produced
When you calculate OA, you are allowed to make allowances for exceptions when the machine is scheduled to be down. An exception might be for scheduled downtime to perform maintenance or because you don’t work on Sunday. These are planned events by management. The exceptions are removed by subtracting all excepted time from the total time – leaving you with the Total Available Time in the denominator. OEE tells you how well you operate when you’re scheduled to run.
Total Asset Utilization (TAU): Is very similar to the OEE calculation but does not allow for any downtime exceptions. It assumes that you are paying for the machine 24X7 and tells you how you are running to an absolute reference (perfection). Once again, it can be calculated for one or a group of machines.
TAU = UT X PR X QR, where:
Uptime (UT) = Actual Runtime / Total Time
Productivity Rate (PR) = Actual Output Rate / Designed Output Rate
Quality Rate (QR) = Good Product / Total Product Produced
The only real difference between OEE and TAU is that OEE takes your defined exceptions into account. Each metric tells you different things – OEE about how well you are operating when you are scheduled to run and TAU about how well you are performing absolutely. They should be used to compare “like machines” to themselves between time periods. They are not as effective in all cases when comparing different types of machines for several reasons.
These metrics are intended to empower organizations to analyze downtime, identify patterns, and prioritize improvement initiatives that directly impact production efficiency and quality. In my experience there is significant misunderstanding of what these metrics mean and what they tell management about the current condition. There are many written references about “World Class OEE” is equal to X%. Unfortunately, this can lead some management teams to set the target at an arbitrary level. Recall from earlier that OEE and TAU are not as effective when used to compare dissimilar resources. The metrics are very effective when used to compare similar machines in time A to the same equipment in time B. However, it would be irresponsible to compare the TAU of a continuous flow furnace to a highly manual set up machining process. They are two very different processes. We need apples to apples comparisons to determine “goodness” and to evaluate true opportunities. I strongly suggest you use the metrics to compare machines to either themselves or similar machines – with the baseline before improvement and after improvement to determine what you’ve gained.
Seeking to achieve some artificial target number can lead to overproduction because operations may continue to produce more than required just to achieve the arbitrary target. Your target level for OEE or TAU (including how much improvement you seek) should be based on your business needs. Any excess improvement could be considered overprocessing if not balanced in the process.
A dirty secret – if you increase your design speed on the line but not your output target, your OEE or TAU will actually DECREASE. By running the line faster, you will achieve your target output sooner. So now you will need less time to run – so your OA or UT will be lower. That’s perfectly OK – but oftentimes it is misunderstood by management as a step back. You will need to be able to explain how your improvement will impact OEE, in this case negatively. By increasing the speed of the equipment, you don’t need as much runtime to produce the same amount of output. So, you should also lower your target for OEE and TAU.
Now that you’ve established your current condition, you should compare your current output levels to your business needs. You can now calculate backwards to determine what improvement level is needed for OEE/TAU. As noted, if you plan to change design speeds, keep in mind that OEE/TAU changes may counterintuitively be affected.
To achieve your production stability, I suggest initially striving to meet the daily goal for 19 out of 20 days. This means you will need to build some level of excess capability into your OEE/TAU target so that you have enough of a passing gear to overcome minor disruptions and failures that always are present at gemba. How much excess you will need is based on how much noise you currently have in your processes. As you start to make improvements it is important to track your outputs for signals – what is the data telling you. Make use of simple statistical analysis to determine how your output levels are changing over time – you may need to both reduce your variation and increase your performance to achieve the required target levels. You can also perform simple simulations to test different target levels to improve your predictability in meeting business needs.
The 6 Big Losses: Where to Find the “Gold Nuggets”
TPM activities focus on eliminating six major losses that hinder equipment effectiveness:
- Equipment breakdowns
- Setup and adjustment losses
- Idling and minor stoppages
- Reduced speed losses
- Defects and rework
- Start-up and yield losses
By meticulously addressing each loss with tailored countermeasures, organizations can regain control over their equipment's performance and dramatically enhance overall efficiency. TPM's proactive approach emphasizes continuous monitoring, early detection, and swift resolution of issues, ensuring optimal equipment availability.
If you have good data for downtime, this can be very easy. If not, there is no better time to start than now. But it comes at a cost – my suggestion is going for speed with some accuracy instead of 100% accuracy in 6 months with some fancy automated system. Don’t seek perfection. A simple paper chart or log will be fine. Have the production team perform a quick sniff test to see if the data reflects their understanding of gemba. Develop pareto charts or similar visuals and go after the repeat issues and larger downtime problems first.
Equipment Breakdowns:
If you don’t have standard work and setup documentation for both operations and typical maintenance repairs – this should be addressed immediately. This should include troubleshooting instructions for the most common issues that negatively impact productivity.
Your maintenance record database should tell you what is breaking, where it’s breaking and how frequently it’s breaking. Engineering and maintenance leaders should already be using that data. Augmenting their efforts with operators and maintenance personnel can provide interesting results – it’s not uncommon for log entries to be misleading or not filled out completely. Getting your data validated is important before you jump in and start to solve any problem. Most decent systems will allow you to develop pareto charts by process, downtime reasons and date ranges. Work with the production team to understand operational constraints and focus improvement efforts there first. You can also use metrics such as Mean Time Between Failure (MTBF) and Mean Time to Repair (MTTR) to track maintenance team improvement.
Setup and Adjustment Losses:
The best way to understand these losses is by simple observation and documenting what you find. Include your most experienced operators here. They can probably identify multiple sources of variation occurring on the shop floor. Their insight can provide key information on what tools or improvements need to be made to simplify or stabilize changeovers. A good metric to track is the total time from the last good part completed to the first good part completed after the changeover.
Operators can have difficulty adjusting to SMED or team-based changeovers if they have spent many years working alone. You should recognize that these types of initiatives are just as much cultural changes as procedural changes. You will need to lay the groundwork and spend time on the reasons behind the changes, team skills, and the need for urgency. You may be tempted to skip this step, but don’t – hours spent upfront will save months later. Help them understand the “why” and then worry about the “how”. I’ve found that the pit-stop analogy works well if there is a strong business need connected to it.
Idling and Minor Stoppages:
Once again, observations are great if you don’t have a system in place to track these minor issues. Another really good way to build this dataset is if you have process cameras installed in the production areas. This can allow you to fast forward and skip normal operations and only focus on start-up where most issues are likely to be found. Make sure you have cleared the use of video for identifying productivity, quality, and safety issues with Human Resources to prevent any misunderstanding. Experienced operators have a wealth of knowledge here – they can tell you not only what the more common issues are, but also which machines tend to run worse. Issues resolved in this category can have a significant carryover to improving other loss factors – so they are attractive to focus on.
Reduced Speed Losses:
These are primarily linked to machines that can’t produce good quality products at their design speed due to various factors. There are also a few operational issues that can be found. Some of the more common I’ve seen are:
- Variation in raw materials
- Variation between machines
- Slowing down the line due to breaks, shift changes, etc...
- Training gaps – operator doesn’t feel comfortable at full speed
Once you understand the issues, there are numerous solutions and countermeasures available to correct them.
Defects and Rework:
You should already have a team working on defects. This is quite commonly performed by engineering and quality functions. When times are slow everyone automatically starts to focus internally and worry more about defect scrap since it’s very expensive. Most teams will focus their entire efforts on NET YIELD (NY%) and the costs associated with them.
My suggestion is to have a separate team focus on correcting your FIRST PASS YIELD (FPY%) to reduce REWORK. Most organizations have a very large hidden factory filled with non-standard/abnormal flow paths and rework processes that greatly impact stable output. It is not uncommon to have zero resources connected to solving this issue. I would assign a manufacturing leader and small team to look at the top rework reasons. A few quick and simple solutions here can often have a significant impact on variability of output. Many of the solutions for FPY% issues also improve the overall NY% because items are not scrapped during rework operations. This should be a key focus for your TPM efforts.
Start-up and Yield Losses:
One of the worst things that lower production levels bring is that you don’t need to run the equipment full-time. Many organizations will reduce headcount and even consolidate shifts for cost and control reasons. That can lead to higher running costs and greater yield losses.
Most production machines “like” to run and they perform better when in a stable production environment. Constantly shutting down, starting up and coming into process tolerances can negatively affect machine performance, quality output and raw materials wasted. It is likely better to run fewer lines, but to do so continuously. For example, if you cut out your night shift you will waste time at the start of the shift warming up machines, and at the end of the shift shutting them down and purging. If you must eliminate shifts for financial reasons, then you should consider small skeleton crews assigned to machine ramping or preheating.
Your more experienced operators can provide details on how this type of production scheduling will affect productivity and process yields. There are many countermeasures your team can use to limit the overall impact. However, this is an example of how your reaction to the slowdown in production could potentially be more detrimental to cost efficiency than just the loss of volume.
Empowering Operators: Autonomous Maintenance
Autonomous Maintenance empowers operators to take ownership of equipment care, fostering a sense of pride and responsibility. This approach involves cleaning, inspection, lubrication, and minor maintenance tasks, enabling operators to detect abnormalities and address issues promptly.
This is a great program to install if you have the bandwidth and the managerial courage to sustain it. However, any benefits you gain will be quickly lost if you push this initiative to the side once production demand returns. I have seen this happen many times, and loss of morale in the production and maintenance group can take a long time to recover. I do not recommend implementing this just because you have the time. Autonomous Care is one part of a larger site wide TPM initiative and needs to be developed in due course within the larger rollout schedule.
There are many ways to include the autonomous care mindset within the production and maintenance teams during periods of lower demand. One of these is to develop an overhaul schedule for production machinery. This can range from deep cleaning of machines to a complete tear down to bare metal and rebuild. During this initiative you can introduce basic systems to promote autonomous care practices such as early detection, lubrication, and cleaning procedures. Any significant downtime should also include many other types of improvements to the equipment in parallel:
- Safety: guarding and power isolation for lockout/tagout initiatives
- Quality: control systems, poka-yoke, inspection systems and presets for process controls
- Productivity: SMED conversion, automation systems, and speed increases
- Maintenance: Overdue and long cycle maintenance tasks, component upgrades, projects for ease of maintenance, early detection/predictive maintenance systems.
Conclusion:
TPM offers a comprehensive framework for organizations seeking stability and resilience, regardless of market fluctuations. By addressing inefficiencies, maximizing equipment performance, and fostering a culture of proactive maintenance, TPM lays the groundwork for long-term success. As you navigate the challenges of slower times, consider how TPM can empower your organization to optimize operations, drive continuous improvement, and thrive in the face of uncertainty.
Whether you need to embark on your own TPM journey, or just take advantage of some of the items we’ve explored in this article, reach out to us at Peak Productivity to discuss how we can support your team. Together, we'll pave the way for a leaner, more efficient future.The body content of your post goes here. To edit this text, click on it and delete this default text and start typing your own or paste your own from a different source.
Peaks and Valleys.....
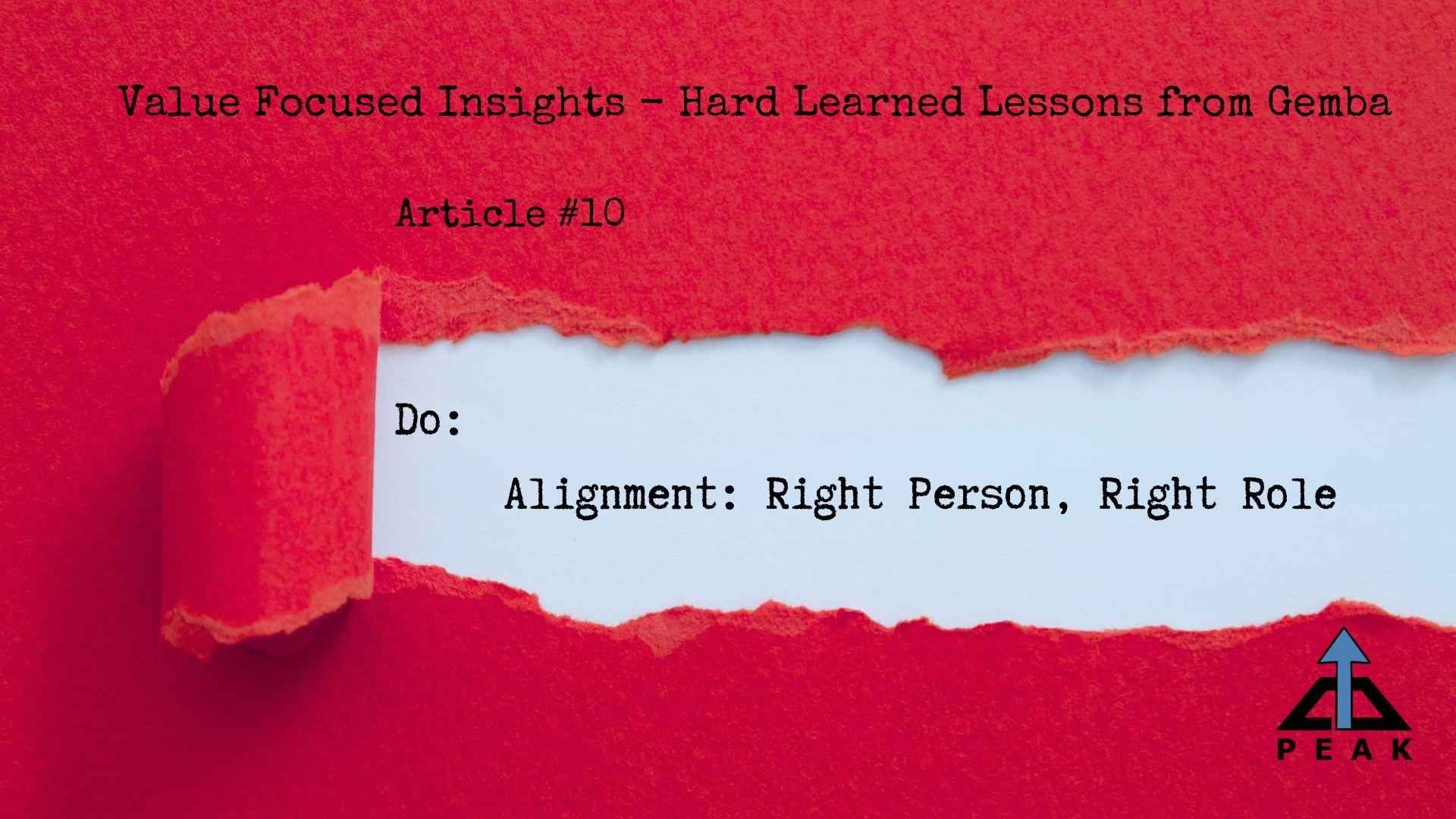
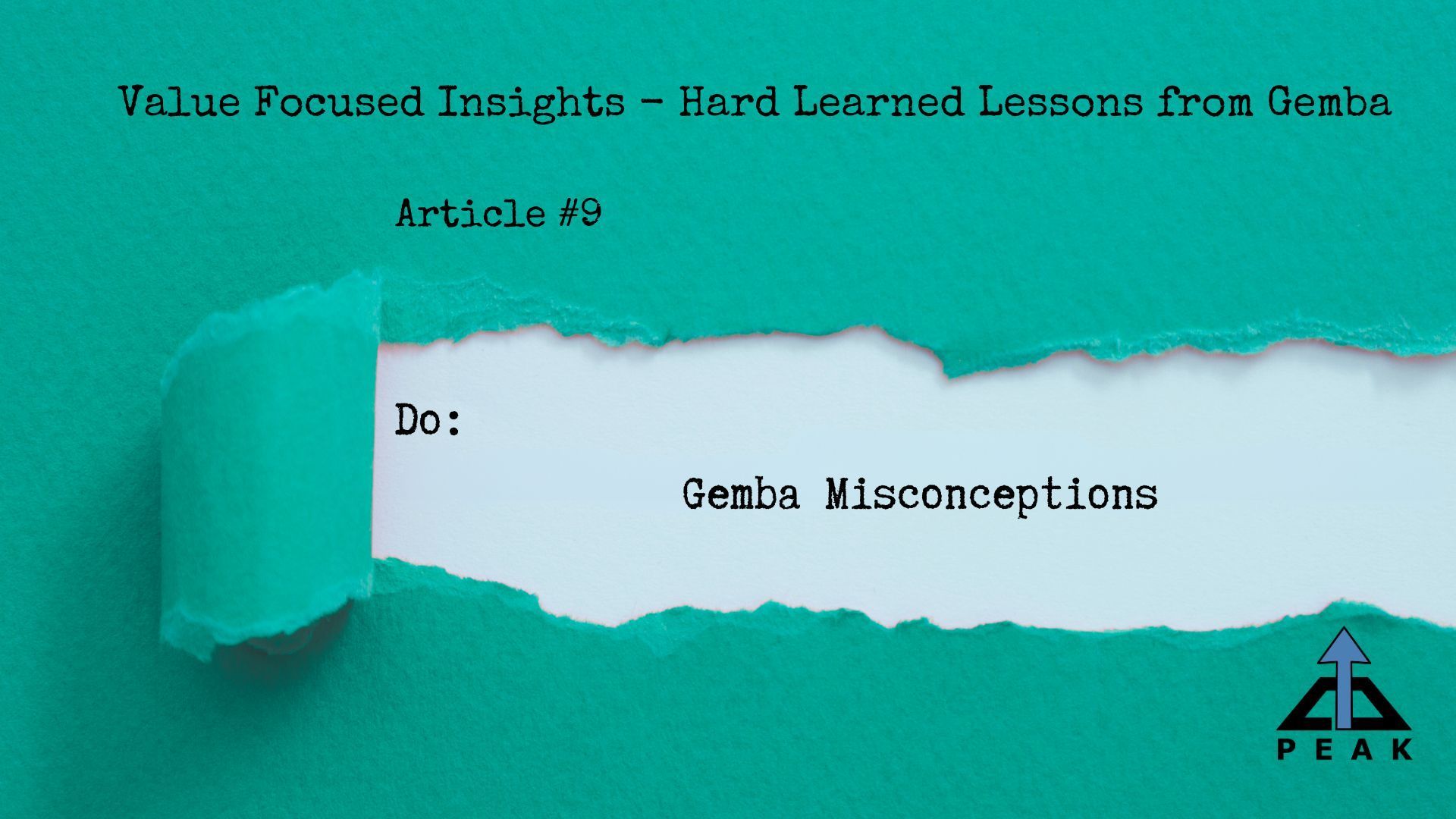
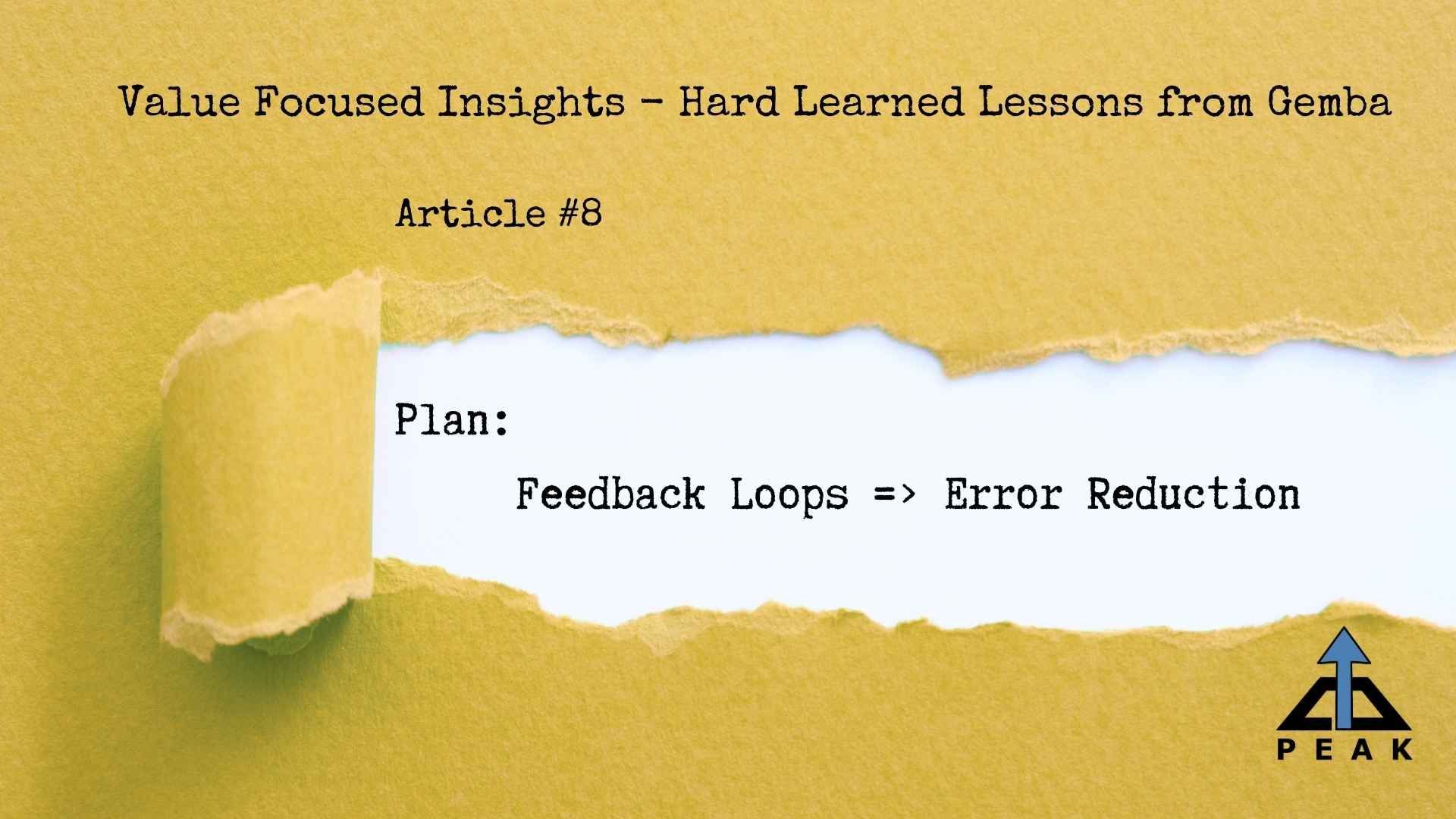
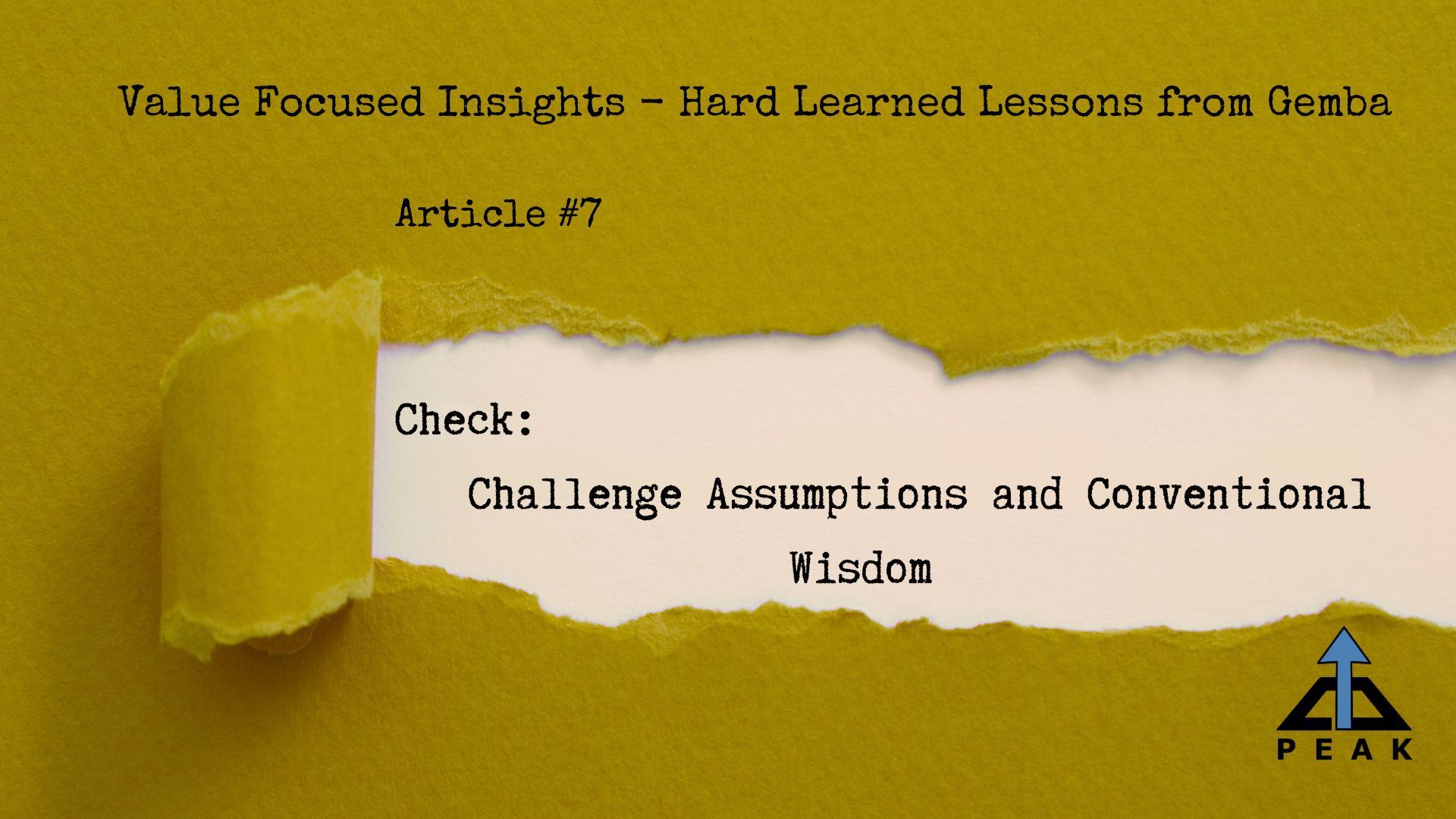
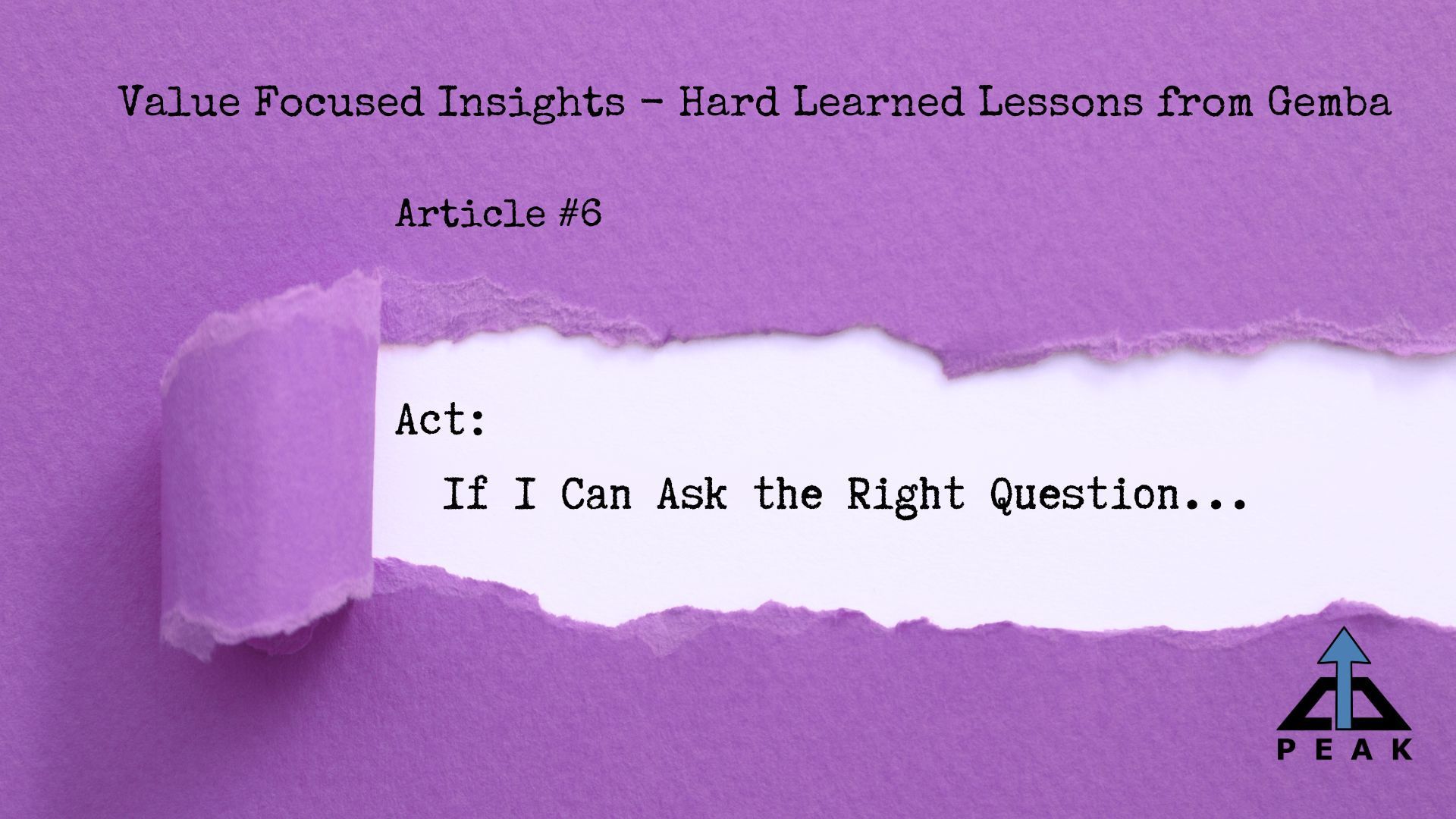
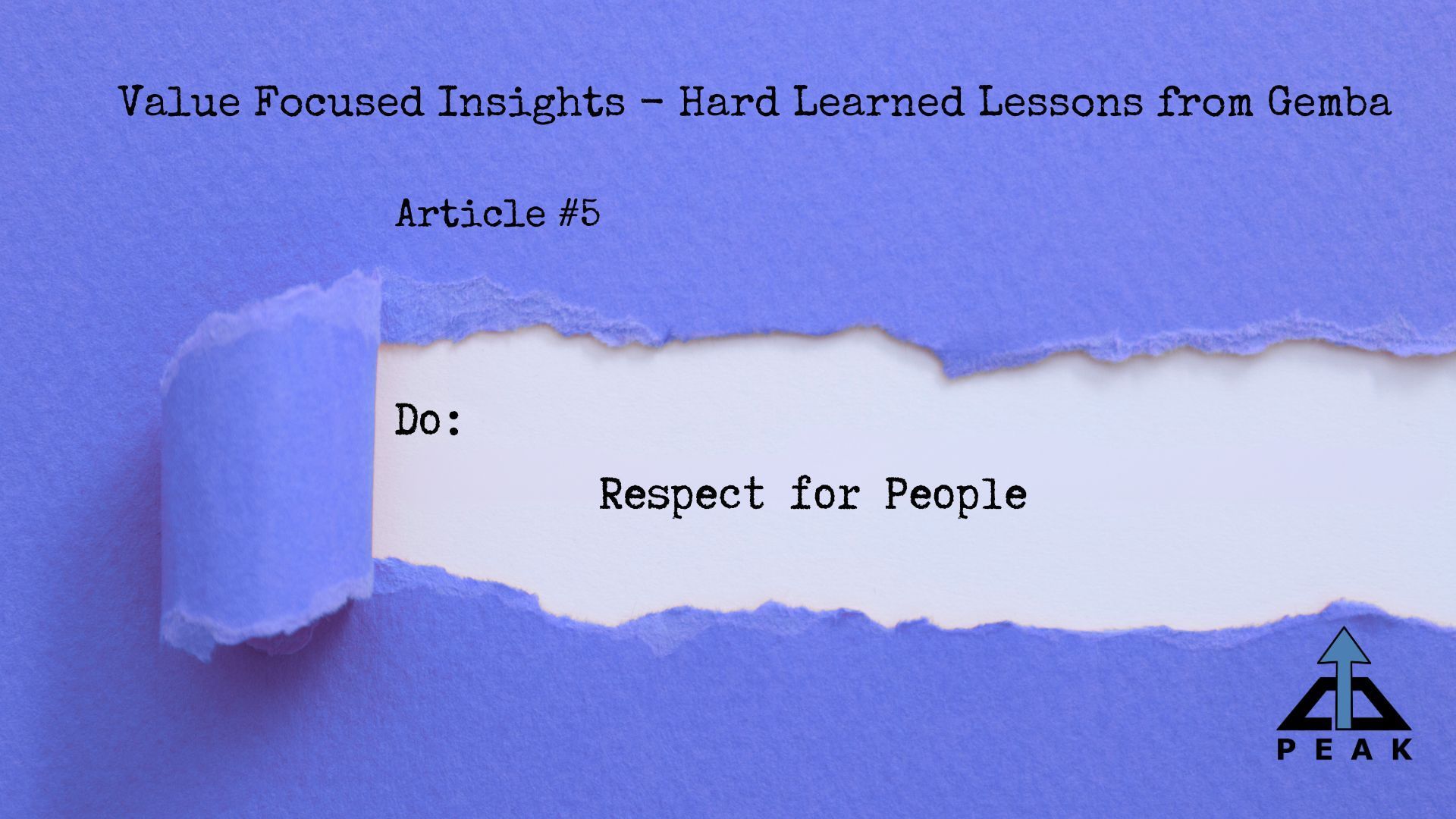
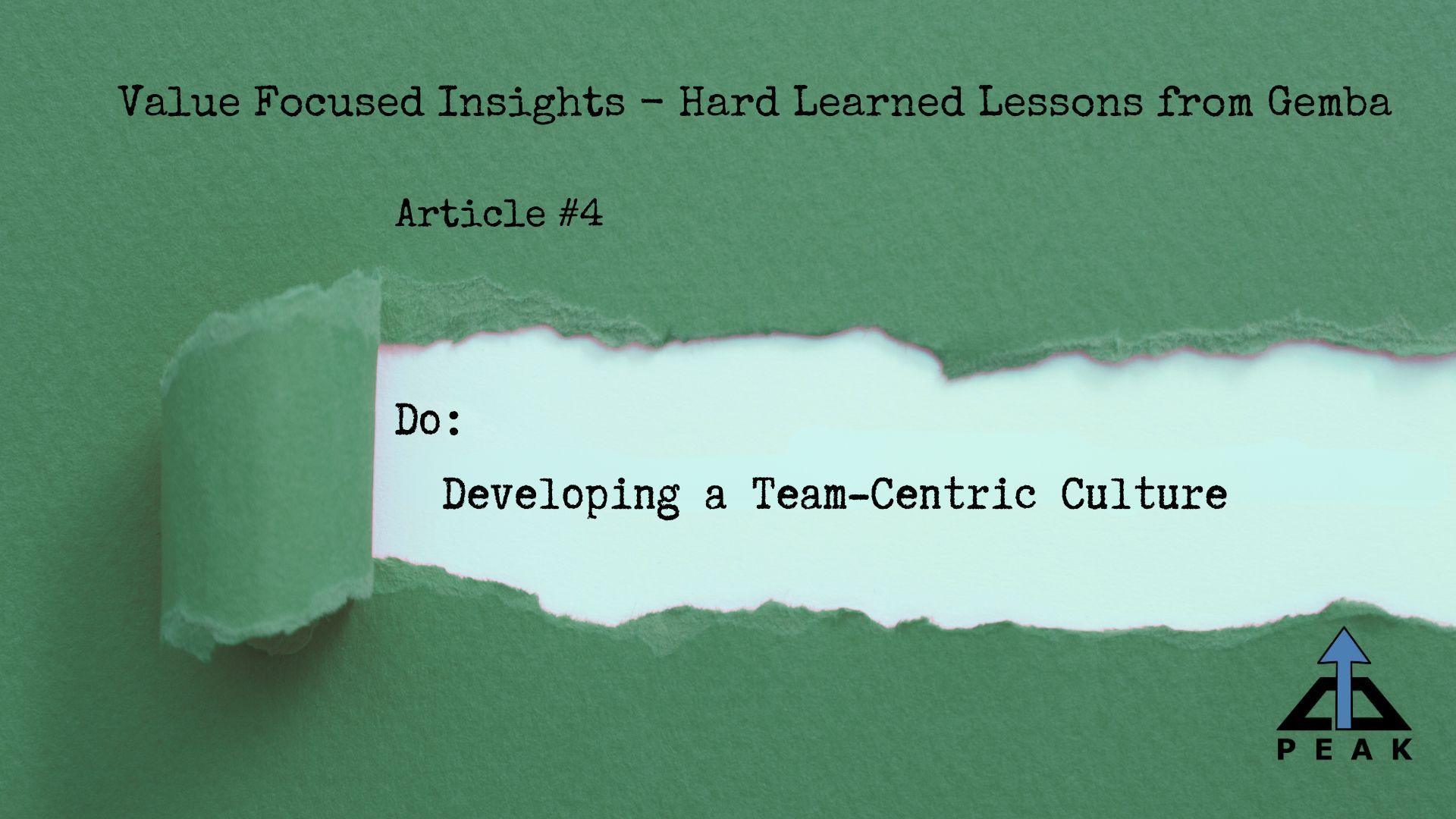
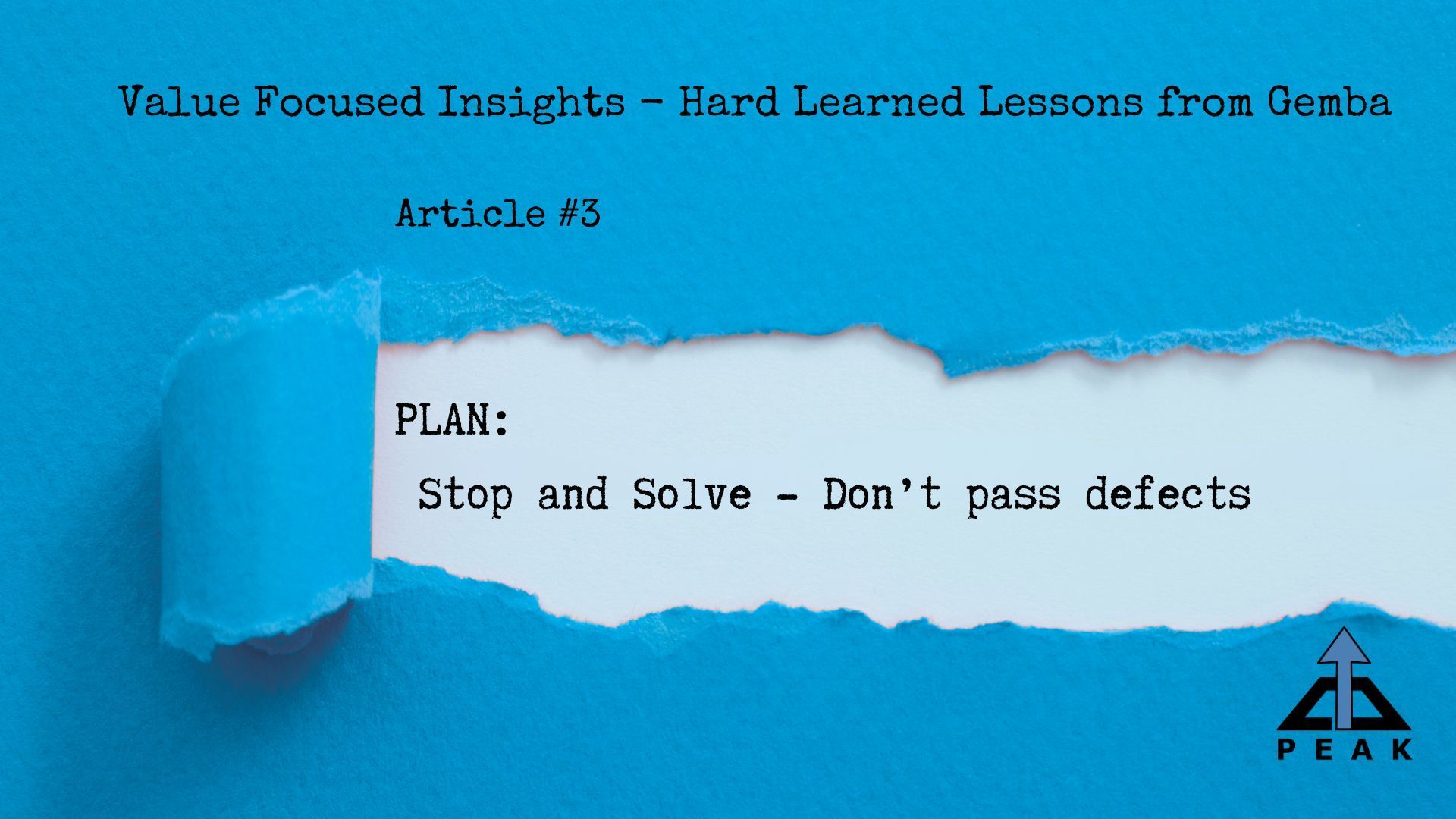
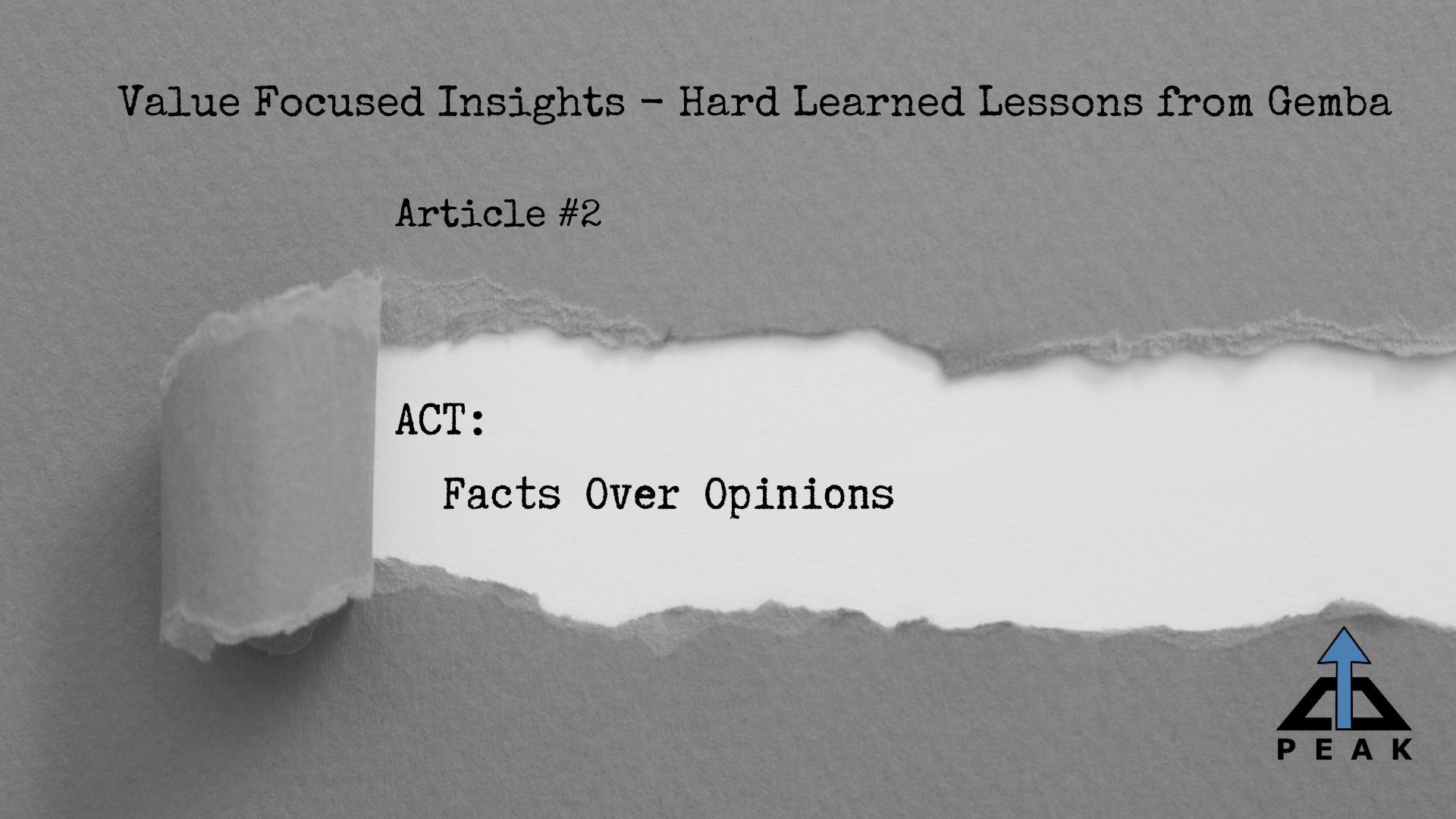
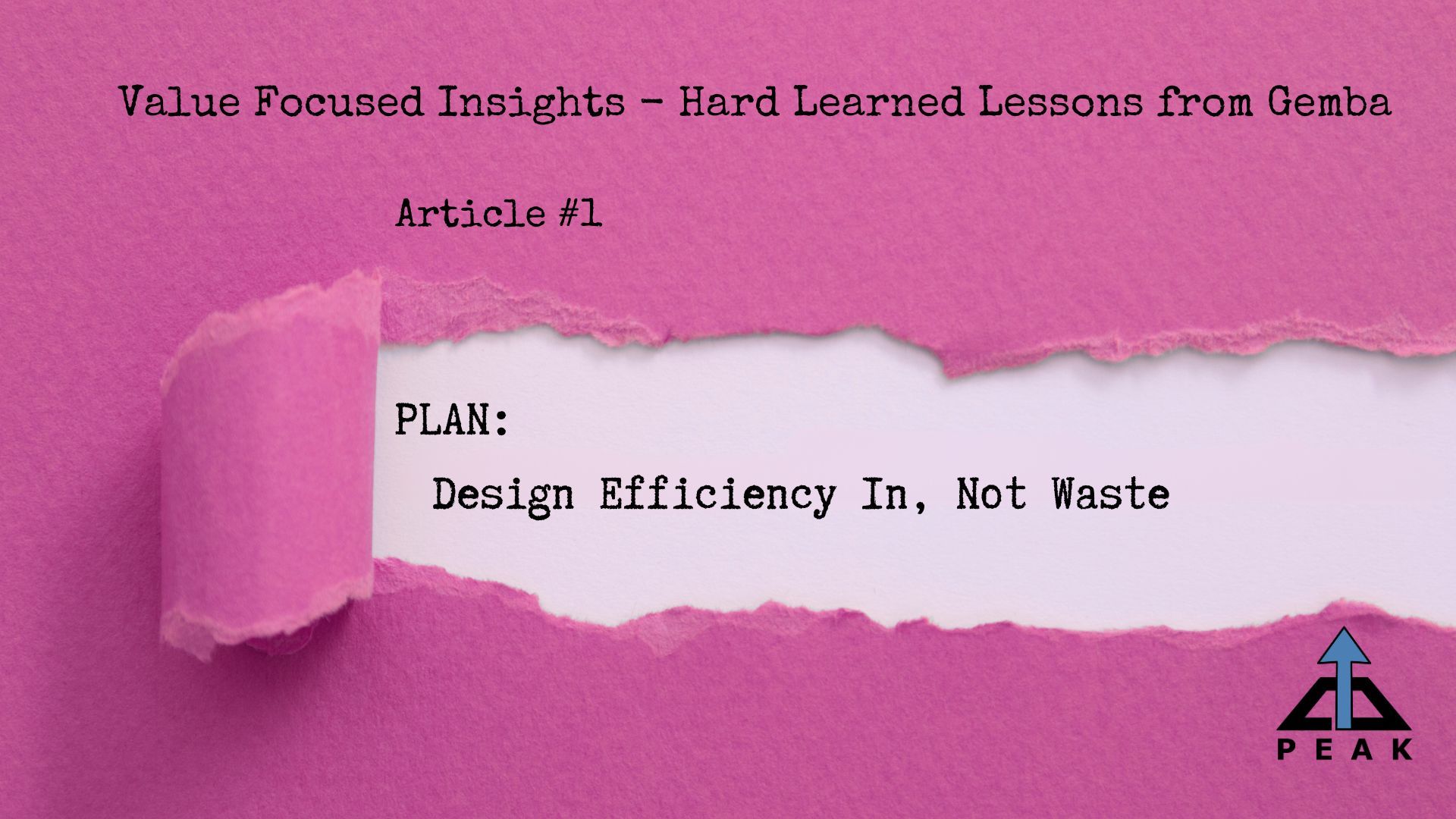